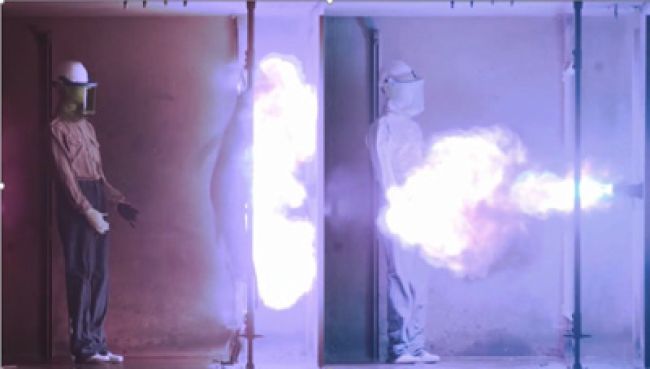
Using Arc Protective Blankets as an Engineering Control Method
While engineering controls are preferred over personal protective equipment for worker protection, many engineering controls, such as arc-resistant switchgear, require the purchase of new electrical equipment in order to fully implement them. When replacing equipment, this type of installation makes total sense, but it rarely can be the only company policy to mitigate arc flash in all facilities.
OSHA always prefers that organizations use the highest option possible on the hierarchy of controls. This is clear in the preamble to 29 CFR 1910.269, in which OSHA states the following: “NFPA 70E-2004 warned that ‘[d]ue to the explosive effect of some arc events, physical trauma injuries could occur’ … OSHA expects that the hazard analysis required by paragraph (g)(1) in the final rule will identify nonthermal hazards, including physical trauma hazards posed by flying debris, associated with employee exposure to electric arcs. … [OSHA requires] employers to address [these hazards] … [and] provide shields and barriers necessary to protect employees from physical trauma hazards. However, as noted by NFPA 70E, not all arc events pose physical trauma hazards from flying debris; therefore, this protection will not always be necessary …”
The 2018 NFPA 70E standard rightly took out the reference to 40-cal/cm² exposures posing a hazard from arc blast, since arc blast is more a function of containment and current than calories. In fact, our recent research surveyed the literature on arc blast pressure waves and found that many of the formulas did not come close to predicting our lab data from 4,000A to 12,000A (E. H. Hoagland, C. Maurice, A. Haines and A. Maurice, “Arc Flash Pressure Measurement by the Physical Method, Effect of Metal Vapor on Arc Blast,” in “IEEE Transactions on Industry Applications,” vol. 53, no. 2, pp. 1576-1582, March-April 2017). New work continues to expand this knowledge and will be presented to the IEEE Electrical Safety Workshop this March in Fort Worth, Texas.
The preamble to 1910.269 further states the following:
“Two commenters requested that OSHA clarify the meaning of the phrase ‘shields or other devices that are capable of containing the adverse effects of a fault’ …
“For example, a ballistic blanket wrapped around a defective splice can protect against injury from the effects of a fault in the splice. The energy that could be released in case of a fault is known, and the energy absorbing capability of a shield or other device can be obtained from the manufacturer or can be calculated. As long as the energy absorbing capability of the shield or other device exceeds the available fault energy, employees will be protected. The proposal would require employees to be protected, regardless of the type of device used and of how it is applied.”
A relatively new concept – using ASTM F2676, “Standard Test Method for Determining the Protective Performance of an Arc Protective Blanket for Electric Arc Hazards” – has been implemented at a few utilities across the U.S., including Sacramento Municipal Utility District and DTE Energy. But many utilities have yet to broadly implement the use of arc protective blankets since, until recently, there had been little guidance on how to use them, even though the test method offers current ratings for a specific clearing time.
A New Standard
Now, ASTM F3272-17 – “Standard Guide for Selection, Care, and Use of Arc Protective Blankets” – has been released to guide utilities. The new standard provides many features to help readers decide when and how to use arc protective blankets as an engineering control for arc flash. Those features include:
- Practical blanket installation methods.
- Guidance on the limits of each method of installation and warnings about wrapping cable splices with arc protective blankets.
- PPE reduction guidance with proper blanket use.
- Care recommendations.
- Clearer explanations about the meaning of the break-open threshold performance ratings from the F2676 standard.
The temperature for different cable splices and other equipment to guide readers as to when blanket use might be considered prudent before entering a vault, manhole or other enclosed area.
A Common Misunderstanding
A common misunderstanding about arc protective blankets is the expectation that they will have cal/cm² ratings, as with clothing. The blankets are rated for a maximum fault current and a current-clearing time in kA cycles, referred to as break-open threshold performance, or BTP. This means that at the maximum current, the blankets – if properly installed – will hold back even an ejected arc for 10 cycles or more, and at lower currents an engineer can use a blanket to completely hold back the arc, up to the function limit.
So, if a blanket is rated at 400-kA cycle BTP and rated for 40 kA – the highest test current in the ASTM F2676 test standard – the blanket can stop an ejected arc under the following conditions:
- 40 kA will be stopped for 10 cycles.
- 20 kA will be stopped for 20 cycles.
- 10 kA will be stopped for 40 cycles.
- 5 kA will be stopped for 80 cycles.
The ASTM F2676 test ejects an arc at the test current – and two additional lower currents – to assure the full integrity of the blanket at different currents, and the lowest average is used for the BTP rating. Most blankets currently on the market are made of flame-resistant materials in multiple layers; many contain or are totally made of ballistic Kevlar. In the past few years, a new blanket has come to market. It consists of silicone-coated fiberglass and offers lower after-flame times and a substantially lower cost, resulting in some utilities considering the use of more blankets or even leaving blankets installed. While the silicone-coated fiberglass cannot be folded – it must be rolled – it is an improved technology when compared to a high-tech welding blanket. Overall, the silicone-coated fiberglass blanket has its pros and cons, but it retards solvents and water, so in some applications it would be an excellent choice. The Kevlar blankets can be easier to handle in some larger applications since they can be folded.
Proper installation of arc protective blankets requires an engineering estimate of the maximum fault current and clearing time of the fault to assure the blanket will block the energy. Even if a blanket fails, it usually will prevent some of the energy from reaching a worker.
Proper installation also may require a structural engineering assessment to assure the channel, wall or support structure the blanket is attached to will sustain the pressure from the arc blast pressure wave.
The ASTM F3272 use standard warns against ever allowing use of a blanket that isn’t arc-rated, even if it is properly installed, so that – in the event that an arc is greater than calculated (e.g., the breaker fails) or the blanket fails (e.g., due to improper current rating, or failure of suspension method or support structure) – workers do not receive additional burns from ignited clothing.
Reducing PPE or Reducing Risk?
When workers are in an area working on other de-energized parts, most utilities that have implemented them use arc protective blankets to temporarily cover cable splices, transformers and other equipment that have high incident energy potential. No company we are aware of removes their requirement for arc-rated daily wear when a blanket is in use. Most companies have started using a blanket to mitigate a portion of the PPE needed because, in the event of a failed cable splice or other energized part, it will prevent some or all of the arc flash energy from reaching a worker. A blanket is not used if a part is being tested. It is used to mitigate parts that are in the vicinity but not being worked on, such as cable splices in the same vault where a de-energized cable is being spliced. In the past, a cable splice often was wrapped with a dielectric blanket or an arc protective blanket, but this method has been shown to provide much less protection unless the wrapping technique is very specifically done. Many utilities do not recommend wrapping because of a firecracker effect or the risk of the wrapping causing a splice to fail due to mechanical movement, but testing showed that wrapping can reduce some of the energy when done properly. However, installation by wrapping also can disturb a cable splice in some applications and would introduce a new risk, which must be considered.
The techniques in the ASTM F3272 guide include the following:
- “J” Type Shielding
- Clamshell “C” Type Shielding
- Suspended Blanket Wall
- Arc Cube Method
- Portable Barrier Method
- Woven Method
- Wrapping
Additionally, in the annex to the standard, there are some temperatures recommended for use in measuring surface temperatures of cable splices and swollen sleeve circumference as an indication of when to use an arc protective blanket. Other indications also are listed, and the reference table may provide electrical installation owners a guide for building internal policies.
Prevention of incidents and lowering employee risk and hazard levels are our primary goals in the electric utility industry. To mitigate the risk of arc flash, one utility we are aware of installed blankets in dual-use vaults during the summer while fiber-optic crews were working in high-risk situations near splices. Now it’s your turn to ask yourself this question: In what ways can you potentially use arc protective blankets to protect employees against arc flash energy in the event of an arc?
About the Authors: Hugh Hoagland and Zarheer Jooma, BSEE, M.S., members of ASTM Committee F18 and IEC TC78, are part of e-Hazard, a company that provides consulting and training on arc flash, electrical safety, protective coordination, written electrical safety programs and on-site safety audits. Hoagland also conducts accident investigations for electrical customers, as well as arc flash testing on blankets and PPE at both Kinectrics, via the FlashCert consortium, and ArcWear.