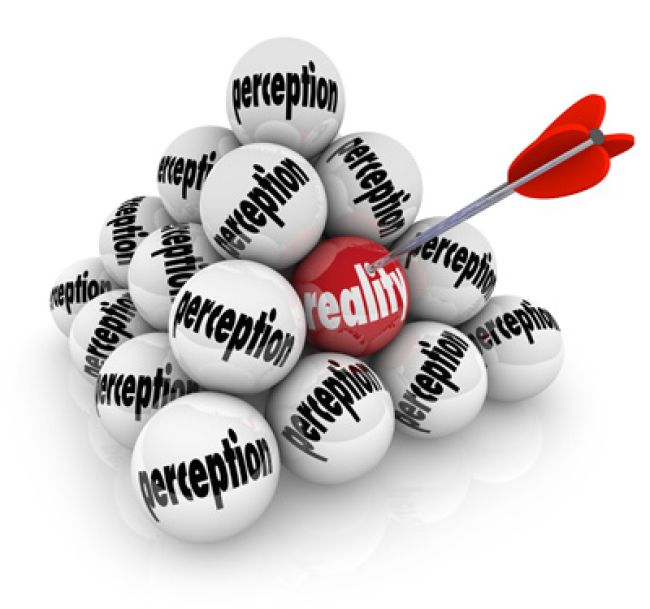
Understanding Safety Culture Through Perception Surveys
If you asked workers at your company who is responsible for their safety, how do you think they would answer that question? Would they say the safety director is responsible, or would they tell you they’re personally responsible for their own safety? You might be surprised by the answers you receive. While the reality is that we are all responsible for our own safety, some employees may perceive that the safety director bears that responsibility.
What if you asked them about your safety program in general? Do employees think it’s strong or weak? Again, you may receive answers that widely vary. For example, management may perceive the company’s safety program to be among the best in the industry because very few accidents have occurred. On the other hand, field employees may feel like no one cares about them or their safety.
In a nutshell, an employee’s perceptions often dictate his or her attitude toward on-the-job safety. And if perceptions about safety in your organization differ greatly from employee to employee, this can indicate that your company’s safety culture isn’t as strong as it needs to be.
So, how can management formally discover how employees perceive safety in your organization? How can they tell if safety programs and processes are working well or falling short? Improvement audits are one tool that many proactive companies use in an attempt to achieve these goals. A comprehensive improvement audit identifies gaps between an organization’s existing state of safety and its desired state. The desired state is typically determined by regulatory and industry best practices related to safety management systems, training systems and written rules and procedures. An in-depth article about improvement audits will be featured in a future issue of Incident Prevention.
Safety Perception Surveys
Another tool organizations can use to identify the reality of their safety programs and processes is the safety perception survey. Its purpose is to gather feedback from employees so management can gain a clearer understanding of actual working conditions and employees’ perceptions and opinions. Through this feedback, management can better identify safety program strengths as well as weaknesses to be addressed via safety management systems. A safety perception survey can be used either as part of a comprehensive improvement audit, or it can be used as a standalone tool.
One of the benefits of safety perception surveys is that those taking them can respond anonymously. Employees are given the opportunity to deliver candid feedback, providing management with a more accurate view of how workers perceive the organization’s safety processes. And the more honest the feedback that management receives, the easier it is for them to determine the reality of the company’s safety culture.
Although the composition of safety perception surveys can vary, they commonly consist of statements that those completing the survey rate on a scale of “strongly agree” to “strongly disagree.” Some typical survey statements include:
• “We always have our scheduled safety meetings.”
• “I can refuse to do a job if I know it puts me or someone else at risk.”
• “I have adequate time to prepare for and finish my tasks.”
Statements are often written several ways and then placed in different spots throughout the survey to ensure respondents provide honest answers. For instance, one statement may read, “Individuals in my department are willing to report violations of standard operating procedures or safety rules.” Another may read, “I am not comfortable reporting a safety violation because people in my department would react negatively toward me.” Both statements suggest the same thing, but each is written with a slightly different tone. If an employee responds to each statement differently, that’s an indication that either the employee did not understand what he or she read or the employee did not provide truthful feedback.
Surveys can be developed within the company, or utilities can opt to partner with a third-party provider. This is often a smart idea in the initial stages of survey development, as third-party providers who specialize in this area already have a well-developed set of statements and/or questions. Regardless of how a survey is developed, management should review all draft questions and statements to ensure they are easy to understand and appropriate for the work environment. In particular, it is critical that employees understand industry terminology used throughout the survey. For example, a survey may use the words “management” and “supervisors,” but employees may be more familiar with the terms “director” and “crew leaders.” Developing a survey that is easily understood by respondents will help to ensure the best results once the survey is distributed. If employees are confused about titles and terms, the data that management derives from the survey could quickly become worthless.
Online Surveys
In the past, surveys were much more cumbersome and costly because they were generally conducted in an in-person, one-on-one format. Fortunately, today’s technology has enabled organizations to distribute surveys online, resulting in easier administration and lower costs. Another benefit of online surveys is the flexibility they provide. As long as respondents have Internet access, they can complete a survey anywhere at any time. Additionally, employers may now get more honest answers from workers because they no longer have to participate in one-on-one interviews.
As with anything else, surveying workers using an online method is not without its challenges. If a company uses a third-party online service – like, say, Constant Contact or SurveyMonkey – to distribute surveys, there’s the potential that some employees may not receive the email containing the survey link because the email may get flagged as spam. To avoid this, one solution is for an internal employee to send out the survey link from his or her company email account.
Another challenge posed by online surveys is getting employees to complete them once they’ve been distributed via email. Even when people are given ample time to do so, responding to a survey may be the last thing on a worker’s mind given all of his or her other professional responsibilities. So, it’s important for management to communicate why the survey is being conducted, and they must also make known their expectations regarding survey completion, including the deadline. It is helpful to send out an occasional reminder so people are less likely to forget to respond. Without management’s involvement, employees may not have a strong understanding of their responsibilities for completion, and thus survey results can suffer.
Results and the Final Report
Once a survey’s results have been received, three calculations are typically used to analyze the data: mean, mode and standard deviation. The mean or average of the numeric response to each statement establishes a relationship between statements. The mode represents the most frequently given answer, which is useful in evaluating what the majority of employees believe. The standard deviation is used to determine variation in the answers. The smaller the standard deviation, the less variation in the answers; the larger the standard deviation, the wider the disparity between answers.
A final report based on survey results should address strong themes throughout the data. As an example, a final report we are aware of included the following: “There is a general opinion that safety training is inadequate. This opinion ranges across all departments, all job classifications and all levels of experience. The results also revealed a high standard deviation for the statement, ‘My department ensures the uniform enforcement of all safety operating standards among department members.’” This information indicates quite a bit of variability in the enforcement of the safety rules.
The purpose of the final report is to identify the good, the bad and the ugly. When employees respond to surveys in a truthful manner, the analyzed data can provide management with a great sense of how the company is performing from a safety perspective, including any possible deficiencies. Once those deficiencies have been identified, a management plan can then be developed and implemented to address them and help strengthen the organization’s safety culture.
About the Authors: Matt Edmonds, CHST, is the vice president of consulting services at SET Solutions and has more than 10 years of field safety management expertise. He has helped clients develop and deliver safety perception surveys and worked extensively with clients to develop, implement and manage their safety processes. Edmonds is also an authorized OSHA Training Institute trainer for the construction and general industries.
Pam Tompkins, CSP, CUSP, is president and CEO of SET Solutions and a 37-year veteran of the electric utility industry. She is a founding member of the Utility Safety & Ops Leadership Network and presently serves on the executive board. Tompkins has authored and presented technical papers on high-voltage electrical safety issues at iP conferences, IEEE workshops, ASSE conferences and for many other organizations. She is an OSHA-authorized instructor who specializes in helping small- to medium-size electric power organizations in the U.S. and abroad comply with today’s safety and training requirements.