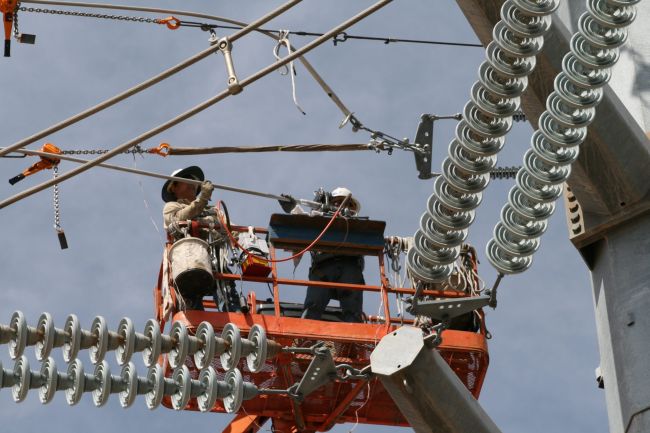
Salt River Project: Devoted to Safety Excellence
It makes sense that an organization that helped turn an untamed portion of the American West into one of the nation’s great metropolitan areas would have a handle on how to keep people safe.
Salt River Project is a major water, power and telecommunications utility located in metropolitan Phoenix. SRP was created in 1903 through provisions of the National Reclamation Act to realize a dream of economic and civic growth in a rugged desert.
Today, SRP is one of the nation’s leading public power utilities and central Arizona’s largest raw water supplier. The utility also leverages its power transmission network to support one of the largest fiber-optic networks in Arizona.
SRP serves more than 2 million people in a water service area of 375 square miles and an electric service territory that spans three counties. SRP also oversees a 13,000-square-mile watershed in the mountainous regions north and east of metropolitan Phoenix; precipitation runoff feeds into a series of six SRP reservoirs and a seventh supplemental source. The utility operates or participates in 12 major generating stations and numerous other facilities in the Southwest.
In short, it’s a big operation. SRP’s 4,700-plus employees typically drive more than 17 million miles annually and log close to 12 million worker hours of exposure according to OSHA standards. So, safety is a major consideration.
Integral Safety Culture
Safety has been a top priority at SRP for decades. The utility has been recognized for its safety practices by a variety of organizations and publications. For example, last year SRP placed first in the large utility (Group H) category of the Electric Utility Safety Awards of Excellence presented by the American Public Power Association, which represents more than 2,000 public utilities nationwide. This was the ninth time in 25 years that SRP achieved first place in the APPA competition. Last year, SRP’s incident rate of 1.02 was the lowest level recorded in the category in three years.
One of the reasons for SRP’s solid record is the spirit of collaboration and personal responsibility for safety that permeates the organization. To reinforce this spirit, SRP has adopted a commitment-based safety approach in recent years that involves safety basics such as awareness, observation and dialogue. Commitment-based safety is a personalized style designed to engage each employee; it is used worldwide by companies from South Africa to the North Slope of Alaska. The concept was developed using ideas from the fields of psychology, quality, organizational development and leadership.
Commitment-based safety involves each employee making a personal choice every day about three to four specific risk management activities that he or she will work to accomplish perfectly. These activities help to ensure an employee’s individual safety as well as the safety of those who work near the employee.
To fortify the effort, employees meet with a small group of peers daily to discuss safety progress. There is no punishment, only helpful support, encouragement, and appreciation from peers and managers. Many employee groups already were doing some form of this prior to the adoption of the commitment-based safety approach.
Another aspect of the approach is the employment of valuable tools available to SRP employees such as S.T.O.P and the Smith System. S.T.O.P. – which stands for Safety Training Observation Program – teaches workplace safety auditing skills for observing people while they work, with steps to reinforce safe practices and correct unsafe acts and conditions. When properly implemented and used, S.T.O.P. is a real-time, collaborative learning process. The Smith System is a results-oriented driver safety training and education program that has been used by more than half of the Fortune 500 fleets in the past decade. Training focuses on the core driving fundamentals of space, visibility and time.
Safety Services: A Versatile Group
Supporting employee safety efforts and education is the role of SRP’s risk management staff, including the industrial hygienists and safety and health specialists of the safety services group. The group, comprised of boots-on-the-ground professionals with impressive trade and leadership experience, serves a variety of needs throughout SRP.
To promote professionalism and leading-edge safety skills, safety services staff and key safety leaders among field and shop employees are strongly encouraged to earn the Certified Utility Safety Professional (CUSP) credential through the Utility Safety & Ops Leadership Network (www.usoln.org). The CUSP program is the only program that offers utility-specific safety credentials to meet the unique requirements of utilities and related contractors. It promotes utility safety leadership by recognizing individuals who meet specific eligibility requirements and pass the CUSP exam, which tests a broad-based understanding of utility safety regulations, competencies and task-directed skills.
The safety services group also has increased focus throughout SRP on field observation processes to identify and report repetitive unsafe or noncompliant behaviors and hazards, and to quantify leading indicators. This information helps SRP to reinforce good behaviors and address hazardous behaviors through a variety of training programs and means.
One example in which observations have paid dividends is the recent revamping of SRP’s essential safety text, the “Accident Prevention Rules” booklet. The editing process was guided by SRP management and leaders from the union that represents SRP hourly employees, who worked together to compile and review rules to keep safety standards current and relevant. The committee reviewed all sections, employee input, and related work practices to eliminate redundancies and unneeded material while updating applicable issues throughout the company. Revisions were based on employee suggestions and changing industrial and OSHA standards. The result is the most comprehensive version of the booklet ever produced.
Segmenting Audiences, Targeting Individual Needs
SRP management understands that successful safety education and support efforts depend on knowing your audience and their motivations, and targeting content that fits their learning styles. The company has four primary audiences of focus for safety communications: field and shop employees, office/professional employees, foremen and frontline supervisors, and middle and executive management.
Field and shop employees, by and large, understand the need to work safely. They also are concerned with productivity and want to be sure that the safe way is also the most expedient and industrious way. Safety communications for SRP field and shop employees rely heavily on face-to-face interactions. Electronic communications and social media are largely unavailable during the workday, and printed communications are read before or after shifts. During shifts, communication comes through the frontline supervisor or foreman in the form of tailboards and other informal meetings.
Office and professional employees can be a tough sell where safety is concerned because many of them believe there are few hazards where they work. Injuries and incidents often are the result of accumulative indifference. These employees must be constantly educated about the importance of ergonomics, reducing office clutter, placement of office furniture and good driving habits.
SRP has a variety of electronic and print channels, so its office and professional employees receive a variety of messages each day. There are weekly commitment-based safety features in the employee newsletter and on the company intranet. Additionally, all meeting leaders are strongly encouraged to select a volunteer to talk about an individual safety commitment during company meetings.
Frontline supervision is an essential audience. While productivity and costs are major focuses for this SRP audience, safety planning and education are paramount. Safety planning means heavily considering the proper way to complete a job. Safety education is critical, as frontline supervisors are usually the most important informational resource for the employees they supervise. That means frontline supervision is in constant need of information, which is provided by a monthly online newsletter emailed to them.
The company’s middle and executive management tend to take the “30,000-foot” view of safety – they want to know what the numbers are and what they mean. This audience is interested in the return on investment for all programs and initiatives, as well as all incident-related costs such as lost work hours and any damaged equipment or materials. These and other safety issues are periodically discussed at big leadership team – or BLT – meetings, which include the extended SRP management team.
The Significance of Safety Committees
Among all the audiences at SRP, some of organization’s best safety training content in recent years has originated in safety committees. The work areas that have outstanding safety records also have safety committees that consist of engaged employees who collaborate to conduct focused, peer-review activities. Within SRP, there’s been a movement in the last decade or so to evolve its safety committees from largely management-heavy groups to employee-driven teams.
The most effective safety committees have monthly meetings to review trends – good and bad – to see if there are any gaps in training, information, tools or equipment. Larger teams also hold quarterly all-hands safety meetings where invited speakers attend and specialty programs are presented.
For the regular safety review meetings, committee members discuss any issues arising from tailboards or S.T.O.P. cards issued within recent months. S.T.O.P. cards are issued from one employee to another when an unsafe work practice is observed. Rather than being a punitive process, the use of S.T.O.P. cards emphasizes cooperation and dialogue to identify and correct safety issues while addressing work process improvements.
Additionally, committee members conduct safety audits by touring facilities and inspecting SRP vehicles to ensure compliance with the “Accident Prevention Rules” booklet and departmental guidelines. They also work with the safety services group to ensure employees have received all notices and informational updates, as well as survey safety practices across SRP to see if another work group has an activity or practice that other safety committees may want to adopt.
All of these safety processes might seem a bit excessive to some, but they have reaped a number of benefits for SRP. Besides reducing lost-time and OSHA recordable accidents, customer satisfaction has increased in recent years. A major consulting group has been surveying electric utility customer satisfaction since 1999. SRP results during this time include:
• The highest score for residential customer satisfaction in the West in 14 of the past 15 years. SRP also has had the highest total among the nation’s largest utilities for the fifth consecutive year.
• Being first in the West for business customers of large utilities in four of the past five years, with the highest score in the nation in three of the past five years.
SRP’s bottom line is that the safe way to work is the best way to work.
About the Author: Barry Kropp, CUSP, started at Salt River Project in 1984 as a temporary laborer. He soon transitioned into a full-time position and eventually became a crew lead. As he gained experience, Kropp moved on to oversee water maintenance and, later, civil construction and maintenance work groups. He became a senior safety and health specialist for SRP’s risk management department in 2011. Kropp holds a bachelor’s degree in business, is authorized by OSHA to teach general and construction industry classes, and is currently working toward his master’s degree in business administration.