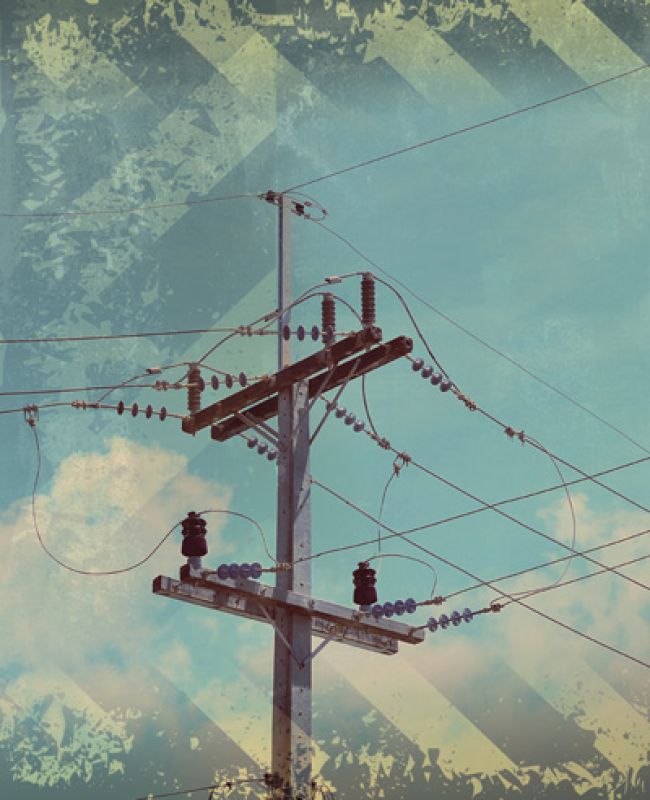
Five Essentials of Successful Safety Programs
Recently my teammates and I were given the opportunity to evaluate the safety programs of a cross-section of contractors conducting potentially hazardous work for a large utility. It was our goal to help those contractors identify the vulnerabilities of their safety strategies and to help them become even more reliable partners to the utilities they serve.
In my line of work, I am often asked what commonalities I see among the most effective safety programs. The temptation is to think that bigger is better, or that world-class safety requires an enormous investment of resources. I wrote this article to dispel some of those notions, and to let smaller contractors know that they, too, can have highly reliable safety programs without huge investments.
Following are five principles my teammates and I have observed in every effective safety program we have evaluated. Please note that none of the following ideas are originally mine. I am indebted to my team and the contractors with whom I have worked. The ideas are theirs, and so the credit must be as well.
Principle One: Safety Expectations are Clearly Defined
Many of our contractor engagements begin with a meeting in a conference room where the safety director brings in a large stack of safety policies. The expectation is that we will be impressed by the sheer magnitude of their documentation and that perhaps we will evaluate the effectiveness of their safety program by the literal weight of their policies. We are tempted to suggest that we visit one of their work sites and ask for a show of hands as to how many on the crew have actually read, or even seen, the documents in question. The results would most likely be humbling.
By no means are we saying that thorough documentation is unimportant. In fact, it’s quite the opposite. We believe that your safety policies should cover your entire scope, be updated every year, and reflect the latest regulatory requirements and industry best practices. However, when it comes to clearly defining your safety expectations so that those doing the work know what you expect, we have found that the most effective safety programs distill expectations into critical observable actions.
One approach to creating critical observable actions is as follows:
- List all of your activities (e.g., overhead distribution, underground distribution, etc.).
- For each of your activities, list each primary hazard, that is, those hazards that – if left unmitigated – could lead to serious injury or a fatality (e.g., electrical contact, fall from height, dropped objects, hazardous atmosphere).
- For each primary hazard, list at least one critical observable action, which is a visible mitigation action that can be clearly communicated and readily observed.
The resulting outline is your code of safe practices. Many contractors incorporate these safe practices into a field guide used to remind their crews, leaders and safety observers of their specific expectations. This code becomes the link that binds every system within their safety program.
Principle Two: Safety Expectations are Clearly Communicated
Employees should understand and agree to comply with your safety expectations from the first day of their employment. While my teammates and I have been impressed by many of the extensive training programs and facilities we have seen, we are even more impressed when organizations clearly communicate each of their critical observable actions in the context of both primary hazard and activity. We are deeply impressed when we receive a crisp, clear answer from a field employee when we ask what must be true for this activity to be safe in this environment.
In his book “Start with Why: How Great Leaders Inspire Everyone to Take Action,” Simon Sinek states that great leaders always start their communication with why, then how, and finally what. Our brains are wired to search for why we are supposed to do something, and if we are not convinced early in the communication, we often will ignore what is being asked of us. Unfortunately, many safety programs communicate what is expected with little attention to the why, thus rendering their communication ineffective early on. As safety leaders, we should always lead with why.
Effective safety programs link their safety communication with the rest of their safety strategy through their code of safe practices. Weekly safety topics that thoroughly explain a primary hazard in the context of a specific activity and go into detail regarding critical observable actions have proven very effective.
In addition, effective safety programs confirm the effectiveness of their communications. The most common confirmation method is to test for comprehension. If someone does not understand your expectations, no matter how well distilled, we have little reason to believe they will comply. The second way truly effective safety programs confirm the effectiveness of their communications is by capturing intent to comply. Done properly, this approach is the equivalent of asking a worker for his or her word that he or she will operate according to each of your critical observable actions. Thus, observed at-risk behavior is no longer just a violation of a rule; it now takes on the significance of a broken promise. We have seen this subtle nuance shift entire cultures.
Principle Three: Hazards are Identified Prior to the Start of Work
Tailboards are one of the best tools available to understand the risks experienced by crews in real time. However, their effectiveness often is degraded due to logistical inefficiencies and inconsistent application. Most utilities and contractors complete tailboards each day prior to work. Optimally, tailboards also should be completed after lunch and whenever the job scope or environment changes.
More advanced safety programs use their tailboards to collect real-time hazard data. For example, they use tailboards to understand how often their crews are working on energized conductors, or are adjacent to traffic, or have crews that include apprentices. This level of analysis requires technology beyond paper. Advanced safety programs adopt an electronic platform for all of their forms, especially tailboards and field observations. The data from those programs informs other components of the company’s safety program, thus enabling their system to become increasingly effective.
Effective tailboards should include a post-job review, which allows you to record and communicate what went well and what didn’t. My teammates and I also have found that the post-job review is an excellent time during which to capture the ever-elusive near miss. There are near misses just about every day on every crew. If your crews are in the habit of reflecting on their day before signing off, and they realize that reporting near misses is contributing to the collective knowledge of their team, then your near-miss program is likely to gain exponential traction.
Principle Four: Safe Work Practices are Confirmed
Your observation program is the sight of your safety strategy. Quite literally, if you are not formally observing your crews, your safety program is blind. So many contractors we work with have neglected this vital component of their safety program, or they have reduced it to a series of robotically checked boxes on paper forms filed in a place no one can locate. We encourage you not to fall into this compliance trap. Instead, design your observation program to be the eyes of your safety strategy.
Limit your observations to your code of safe practices developed earlier in this process. Organize your observation form by activity, primary hazard and critical observable actions. Only observe what you have thoroughly discussed with your crews. The most disruptive place for an employee to find out about your expectations is during an observation. If you have communicated your code of safe practices well, confirmed comprehension and captured a commitment to comply, then your observers will spend the majority of their time confirming safe work practices as opposed to addressing at-risk behaviors.
How many observers should you have in the field? Our quick answer is as many as possible. However, we have found that the most effective safety programs have approximately one dedicated observer for every 50 field workers. In addition, we have found that effective programs include observations from every level of the organization – literally training every employee to be an observer.
The most advanced safety programs have integrated their observation program into their entire safety system. Electronically tracking and trending your observation data will allow you to be more responsive to emerging primary hazards or at-risk trends that are developing. Electronically capturing observations and then streaming the data into an analytics platform will enable you to integrate your data into your safety strategy as well as communicate your key performance indicators to every level of your organization.
Principle Five: Participation at Every Level is Encouraged
It is not uncommon for us to see the lone safety manager shouldering the entire burden of safety for an organization. We think this is a very outdated and increasingly inefficient model. Successful safety leaders are just that – leaders, no matter their job title. They inspire participation, involvement and commitment. Following are the best practices we have observed for promoting participation.
Create a safety leadership team with representatives from every level of your organization. While this often is a step associated with a more mature safety program, we list it first because of its importance. In fact, this typically is the first step we recommend for any safety improvement effort. It is vitally important to capture the perspective of everyone from top leadership to the newest employee. Leadership must understand that they cannot delegate safety, and field workers must take ownership of their own program.
The most effective safety leadership teams meet weekly, usually via conference call. These meetings are an excellent opportunity to discuss the hazard information and lessons learned from your tailboards, as well as data from your observations.
A major part of increasing participation is recognizing safe work practices and safety excellence in the field. Positive reinforcement generally encourages workers to participate more avidly in safety leadership.
A Final Principle
There is one last important principle I want to briefly mention: integration. The most advanced safety programs my teammates and I work with, perhaps those considered world-class, intentionally and effectively integrate the components of their safety programs. Their critical observable actions link their systems. Their tailboard and observation programs inform their training. Their training program introduces and confirms their critical observable actions. Their programs are holistic, and their results are impressive. We are confident that you can achieve the same results.
About the Author: Thomas Arnold, CSP, CUSP, MBA, has been a principal consultant with Professional Safety Solutions since 2009. He can be reached at tom@prosafellc.com.