Mack Turner, CUSP
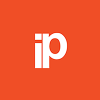
Mack Turner, CUSP
Am I My Brother’s Keeper – Or Not?
I am sure that the safety leaders reading this Tailgate Topic have heard some or all of the following phases: “I’m my brother’s keeper,” “Don’t get hurt,” “Work in a manner that prevents injury,” and “Keep your head in the game.” These phrases are well-intended; they serve as a reminder to keep safety top of […]
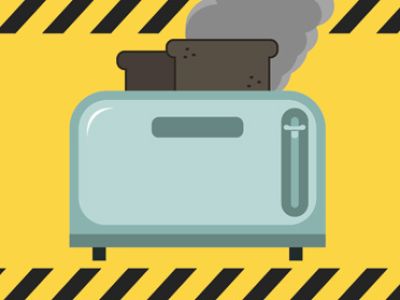
Overcome ‘Burnt Toast Syndrome’ to Improve Safety and Training Results
I have a beautiful and caring better half. She is always there for me. One of the things she does for me is make breakfast. Now, I am an old country boy, so any old breakfast won’t do. I want meat, eggs, potatoes and toast, and she is happy to prepare them for me.
4 Actions to Combat ‘Sheepeople Syndrome’
I was recently consulting with a client’s safety committee about updating their safety handbook and standard operating procedures. During a discussion of work positioning and work methods, it was discovered that their policies were in violation of OSHA’s minimum approach distance rules. Their initial response was, “Well, we’ve always worked that way, and so do […]
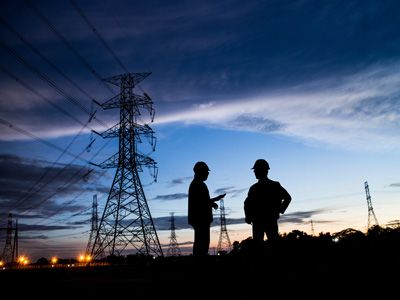
Feedback and Accountability in the Disciplinary Process
Disciplining employees is always a tough task to handle, so it’s not surprising that many leaders and employees have a fear of the disciplinary process. However, discipline is a necessary part of business. That’s because sometimes, despite people’s best intentions, course correction must occur. As leaders who are tasked with doling out discipline, we should […]
A Can of Soup: What We Say and How We Say It
If you look closely at the label on a can of soup, you likely will notice the ingredients section, which lists the soup’s contents from those with the greatest volume or weight down to the ingredient with the lowest volume or weight. This information is good to know before you decide whether to buy the […]