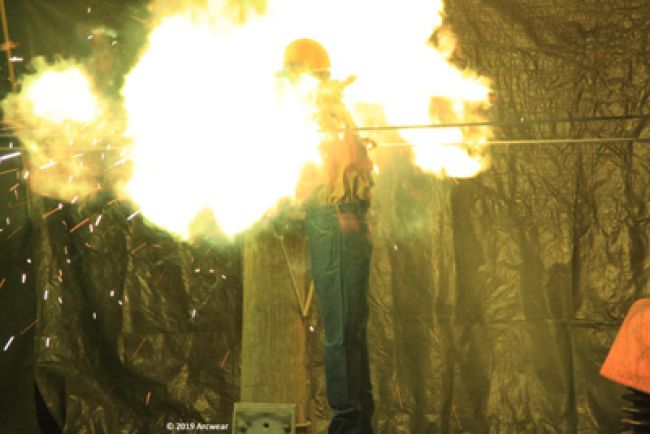
Arc Flash Considerations for Utility and Construction Activities
Electrical safety-related work practices are governed by different OSHA regulations for utilities and construction companies. Utilities follow 29 CFR 1910.269 and construction companies follow either 1926 Subpart K or 1926 Subpart V, depending on the job site. It wasn’t until the 1910.269 revisions in 2014 that OSHA used direct wording mandating arc-rated clothing. And while it may seem that five years is enough time to install an organization-wide PPE program, it is not uncommon to find such programs lacking. Recently, a utility’s operational team confirmed that they normally operate a piece of equipment while wearing street clothing. While this practice may not be a problem in certain limited cases, in this instance the garment labels prohibited any energized work based on the high arc flash energy. The problem was, these workers failed to realize that switching off is considered energized work. Serving as independent safety consultants to various construction companies and utilities has offered us a great deal of insight into similar hazardous operating conditions, but at the same time has allowed for testing and implementing what works in these environments. This article, the first in a two-part series, introduces the concepts of arc flash and shock hazards, followed by a discussion about personal protective equipment (PPE) that guards against those hazards. The second article in this series will provide guidance on how to effectively communicate the adequate level of protection to workers.
Arc Flash and Shock Hazards
In low-voltage networks (<600V), the safe shutdown of equipment is followed by applying a padlock at the correct location and testing for the absence of voltage. The act of shutting down (switching) is considered live work and presents an arc flash hazard. The act of testing also is considered live work and presents both a shock hazard and an arc flash hazard. Additionally, in certain high-voltage applications (>600V), OSHA requires the system to be considered energized – even after the correct switches are opened, padlocked and tested for the absence of nominal voltage – until it is adequately grounded.
Switching, racking, inspecting and cleaning are examples of interacting with energized equipment, and all present an arc flash hazard. Testing, repairing (maintaining) and grounding are examples of contact – either direct or indirect – that present both a shock hazard and an arc flash hazard. OSHA doesn’t require that the hazard never be present; instead, it requires that the employer eliminate the hazardous energy as the first option. If eliminating the hazard is not possible, only then can the employer consider risking injury and reduce the risk to a tolerable level. Examples of when energized work is permitted include troubleshooting that requires voltage and when shutting down creates a greater hazard. OSHA does not permit energized work simply because it may be inconvenient or production-inhibiting to de-energize.
Personal Protective Equipment
Different types of arc-rated PPE work in different ways to protect workers against the thermal effects of an arc flash. The arc rating, as either the arc thermal protective value (ATPV) or the energy breakopen threshold (EBT), of the PPE is listed in calories per centimeter squared (cal/cm2) on the label. Neither result indicates better performance against the thermal effects of an arc flash, but rather, each is the outcome of the test method stipulated in ASTM F1959, “Standard Test Method for Determining the Arc Rating of Materials for Clothing,” and the performance specification, ASTM F1506. The ATPV provides the point at which the test samples resulted in a burn with a 50% probability, while the EBT provides the 50% probability at which the test samples indicated an opening of more than 0.5 in2 in area or 1 inch in any direction, which creates exposure. If the working conditions are better suited to fabrics that are more insulative than strong, fabrics with an EBT (i.e., knit fabrics) would work well. If strength is chosen over insulative qualities, then a fabric with an ATPV rating may be more suitable. If still unsure, acquire different samples and provide them to workers for feedback to support the PPE program. Keep in mind that different garments will be required for the different seasons, especially in areas where extreme temperature fluctuations occur between the summer and winter months. Whatever the decision, always source from a reputable and established supplier and ensure that the fabric can be traced back to the ASTM F1959 test report. The garment label should mention the ASTM F1506 standard, as shown in Figure 1 below.
Figure 1: Garment label showing the ASTM F1506 standard.
Incident energies less than 1.2 cal/cm2 are the industry standard for the safe lower limit of energy, while OSHA uses 2 cal/cm2. The difference is due to the fact that NFPA 70E and OSHA have used different heat transfer models. Practical testing of protective fabrics does not show much difference between these two values; however, most of the industry has opted to use 1.2 cal/cm2 as the lower limit. Users must be protected once that limit is exceeded. If the energy is between 1.2 cal/cm2 and 12 cal/cm2, the worker typically will require a hard hat; arc-rated balaclava and face shield; safety glasses; hearing protection; long-sleeved arc-rated shirt; arc-rated pants; gloves for shock protection; leather overprotectors; arc-rated or natural-fiber innerwear and underwear; and leather shoes. No metallic or conductive items or parts should be exposed to the potential arc flash. This ensemble is generally known as arc-rated daily workwear. When the energy exceeds 12 cal/cm2, a flash suit is used over the arc-rated shirt and pants combination. The face shield and balaclava combination is replaced with a flash suit hood.
Daily Workwear
A somewhat dated study by the American Burn Association found that almost all arc-flash-related fatalities in recent times have been due to the ignition of garments that were not arc-rated. Commonly used acrylic blend, poly-cotton or 100% untreated cotton street clothing ignites relatively easily and continues burning long after the arc is extinguished. Based on data from arc flash accident investigations, arc-rated clothing decreases the extent of the injury and, when adequately selected, does not cause burn injuries. From limited in-house testing, we know that the performance of arc-rated fabrics does not appear to diminish after the equivalent of a year’s worth of regular washing and is likely to outlast cheaper non-arc-rated uniforms. This provides both safety and financial incentives to change daily worker uniforms to arc-rated daily workwear. In many instances, time lost changing into arc-rated clothing should be factored into the overall costs of arc-rated PPE. These days, combination-rated clothing means that workers are protected against both flash fire by NFPA 2112 and arc flash. This may be an important consideration for individuals working around gas (e.g., natural gas plants, propane and acetylene tanks), insulating oils and grease. The greatest benefit of adopting arc-rated uniforms for workers is that the arc-rated protection is always available and is not something that has to be fetched from a truck and changed into. In addition, it eliminates a huge source of human errors and omissions. If high-visibility clothing is needed, most arc-rated shirts can be supplied with high-visibility tape on the sleeves. However, complete high-visibility shirts are available, as are add-on high-visibility vests. Ensure that the label states both ANSI/ISEA 107 for high visibility and ASTM F1506 for arc-rated protection. Innerwear – such as T-shirts and vests – and underwear cannot be of a melting substrate. Acrylics, polyester, poly-cotton, spandex and similar materials are prohibited. Natural fibers, such as cotton, silk, and wool innerwear and underwear, are acceptable. Arc-rated innerwear and underwear, although preferred, are not mandatory.
Gloves
Size and rating are two common problems with worker gloves intended to protect against arc flash and electrical shock. It is still common for employers to procure gloves for workers without sizing the workers’ hands. Gloves become difficult to use if they do not fit correctly. At a recent national electrical safety conference, it was mentioned that more than 80% of arc-related injuries occur to the hands and head/neck area. Another problem is purchasing one set of gloves for the maximum voltage a worker may be exposed to. ASTM D120, “Standard Specification for Rubber Insulating Gloves,” provides for six glove classes based on the maximum voltage use. The gloves become thicker as the voltage increases, impacting finger dexterity. It is now common to find workers issued two classes of glove: one for low-voltage work and another for high-voltage work. Since the rubber insulating glove is dielectrically tested every six months, utilities provide workers with two pairs of each class of glove. Different colored gloves are a good option to ensure that workers are not unintentionally using an out-of-date glove. For example, everyone uses a blue rubber glove from January to June and a black glove from July to December. This way, fellow workers and management can easily identify a noncompliant glove. Rubber insulating gloves must always be used with leather overprotectors. Overprotectors offer mechanical protection to the rubber insulating glove and increase the arc flash protection level on the hand. Recent changes in ASTM F496 regarding the in-service care of protector gloves require that leather overprotectors be in a clean and dry condition before being stored. It was found that wet leather may leach byproducts from the tannery process onto the insulating glove. This condition is exacerbated when the insulating glove is stored inside the overprotector glove. The standard allows for the storage of the insulating gloves inside the overprotectors if the clean and dry conditions are met.
Head, Face and Neck Protection
As mentioned, the majority of arc-related injuries occur in the hand, head and neck areas. OSHA requires that workers be protected from flying objects, thus mandating the need for face shields. Facial protective equipment must meet the ASTM F2178 test method and performance specification standard. Since the visor or goggle is tested to ANSI Z87.1, it is expected to withstand flyings (i.e., shrapnel) from an arc flash. However, if the hard hat and face shield are knocked off the worker, the use of safety glasses must be considered. In fact, NFPA 70E mandates their use. The utilization of the face shield and safety glasses is generally combined with hearing protection to protect against an instantaneous peak in sound level and pressure differential from the arc. This arrangement still leaves the neck and back of the head exposed to the arc flash incident energy, requiring the addition of a balaclava or hood sock. Laboratory testing showed no burns when the face shield/balaclava combination was exposed to a marginally higher-than-rated incident energy from various angles (front, back and sides). The back exposure handled more than three times its rating, as shown in Figure 2 below.
Figure 2: Rear arc exposure at three times the rating of the PPE with no burns registered on the sensors.
An alternative to the face shield/balaclava setup is the use of a flash suit hood. Hoods now allow the visor to be lifted when necessary. Visual light transmission and color rendering on new face shields and visors offer near natural viewing with good peripheral vision.
Conclusion
This article conveys practical considerations for initiating and updating a PPE program to address electrical safety. The need for such PPE is based on the exposure to either a shock hazard or an arc flash hazard. Certain tasks will require PPE for arc flash protection while other tasks may require both arc flash and shock protection. Most plants will require protection in the form of daily workwear and a flash suit. Organizations should decide on the appropriate protection levels and supply both garments to workers who are exposed to varying levels of arc flash energy and shock (voltage) levels.
The second article in this two-part series will help to guide organizations on a method to effectively communicate the adequate level of protection to workers via arc flash labeling techniques. The data that goes onto the label is generated from an estimation of the arc flash incident energy based on an arc flash engineering study or incident energy analysis.
About the Authors: Zarheer Jooma, P.E., joined e-Hazard U.S. (www.e-hazard.com) in 2016 after 10 years of managing e-Hazard South Africa. He earned a master’s degree in electrical engineering and is a registered professional engineer. Jooma performs electrical network design, arc flash studies, electrical safety training and auditing. He has convened and chaired arc flash safety standards and is a member of both ASTM and IEC electrical safety standards committees regulating arc-rated PPE. Jooma currently is working on updating IEEE 1584.1 regarding the scope of arc flash engineering studies.
Hugh Hoagland is one of the most active trainers and researchers in electrical arc protection. His NFPA 70E and OSHA 1910.269/NESC training programs are used by many Fortune 500 companies and governmental agencies. Hoagland has developed testing since 1994 and has performed over 50,000 electric arc tests (www.arcwear.com). His publications are numerous in IEEE and safety magazines, and he helped invent many arc-rated materials used today.