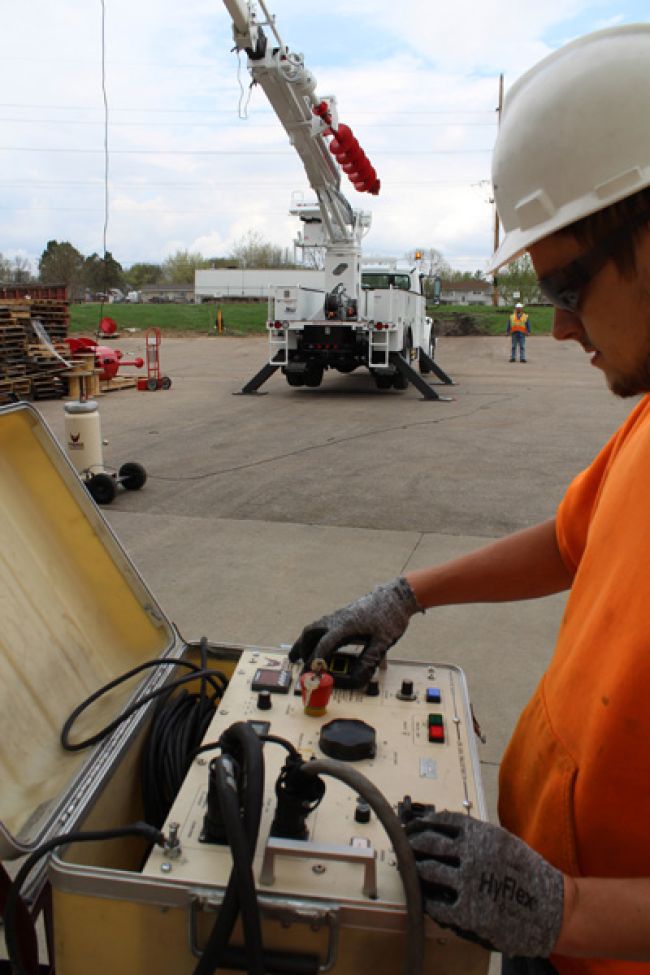
When Insulating Booms Fail Dielectric Testing
Insulating boom aerial devices and insulating boom digger derricks are designed to provide secondary protection to help prevent workers from being electrocuted. Maintenance and dielectric testing are critical and required by law to verify that the insulating portion of the machine is functioning as designed.
A new boom is dielectrically tested at the factory following ANSI requirements for a qualification test to verify the insulating rating. Additional tests are performed to confirm the insulating value after units are finished and operational. Once insulating equipment is placed in service, maintenance tests are required to be performed for a variety of reasons. Periodic testing in accordance with the ANSI A92.2 or A10.31 standard is required. If the equipment has not had a dielectric test performed within the last 12 months, as required by ANSI and OSHA, it cannot be considered insulating. Dielectric testing also should take place after repairs or replacement of components in the insulating sections, when a problem is suspected or after incidents of contact with energized power lines.
Environmental factors can affect the results of a dielectric test. The environment of use, exposure to sunlight, surface condition, damage, and cleanliness of the boom and internal components could lead to dielectric test failure. Following are some of the procedures a boom test technician performs when booms don’t pass a periodic test. Periodic testing usually is conducted annually, but many owners perform tests more frequently when weather or harsh conditions warrant them.
Troubleshooting Procedures
The external insulating portion of the boom is checked to be free from scars, gouges, scuff marks and wear-pad marks. The boom should be clean inside and out. If needed, the technician will clean the external boom thoroughly with a nonabrasive mild cleanser and a fine abrasive pad.
Next, for unsealed booms designed for inspection and maintenance access, the technician will inspect the interior of the boom, looking at the hoses and leveling rods. If a sealed boom fails after exterior treatment, the seals must be removed, and the interior inspected. Debris found will be cleaned out, and the interior surface of the boom will be washed out with a mild soap. Harsh detergents and pressure washers are not used, as they will remove the wax on the boom’s interior. High-pressure washers are not used against hydraulic hoses, which could strip off their jackets. The interior is flushed with clean water to remove soap residue. Steam is never used to clean the boom, inside or out. Besides possibly damaging hoses, steam can remove wax and cause water to be absorbed into the boom.
After internal washing, the boom usually needs to dry for a minimum of 24 hours.
Next Steps
After the boom has been inspected, cleaned and dried, the technician will perform the dielectric test again. If the unit still fails to pass the test, the problem must be identified by process of elimination.
If the test technician also is a qualified mechanic, he or she may need to begin removing components inside of the boom one at a time and retesting. If the boom tests well with a component removed, the component is either replaced or, if practical, repaired to like-new condition. After the mechanical repairs are made, the boom gets waxed or treated with silicone as specified in the unit’s maintenance manual, and the dielectric test is performed again.
If all the components inside the boom have been removed and the unit still fails to pass the dielectric test, there is a problem with the fiberglass boom. Technicians may use mirrors or a camera inside the boom to inspect for carbon tracking, embedded dirt or damage. Carbon tracking creates an electrical path through the fiberglass. If rusty or dirty areas are found, the interior needs to be scrubbed. If the carbon tracking has burned deep enough into the fiberglass, it may require replacement.
After the inside of the fiberglass boom is cleaned, it gets tested again. If it passes the dielectric test, the interior is recoated with silicone or wax to restore water protection. The technician will again perform the dielectric test after reassembly before returning the unit to service.
If a technician is suspicious that the outer gel-coat is causing the dielectric test failure, he or she may perform a DC test on the gel-coat surface. The technician will use 100-grit sandpaper to sand a boom section at least 12 inches in length to remove paint and/or gel-coat finish around the entire outer surface of the boom in the insulated section. After cleaning the abraded surface, the technician performs the DC test. If the test shows significantly less leakage, the outer surface coating must be removed and recoated following the manufacturer’s instructions.
If the boom – with all components removed and the interior cleaned – still fails the dielectric test, it must be replaced. The new boom structure is mounted and tested, the internal components are installed, and the boom is dielectrically tested again following the qualification test procedure in ANSI because the original qualification test is no longer valid. With the boom’s dielectric strength confirmed, surface treatments are performed following the manufacturer’s procedures, and the unit can be returned to service.
About the Author: Joe Cisneros is a Terex national service technician with 47 years of experience in the industry. He has extensive experience servicing aerial devices and digger derricks and has been training for Terex since 1999.
The information in this article is adapted from Terex Utilities’ Tech Tip #51. The company’s Tech Tips provide additional insight into frequently asked questions that Terex service representatives receive and are a supplement to service manual instructions. For more information about Tech Tips, visit www.terex.com/utilities, click on Support, Technical Support and then select Tech Tips.
*****
What to Look for After an Aerial Device Makes Electrical Contact
If inadvertent electrical contact occurs, causing an arc or damage, aerial devices should be removed from service for inspection. It’s a good idea to interview the device operator to gather information to aid during the inspection. If an injury occurred as a result of the electrical contact, notify the proper authorities and the aerial device manufacturer. The qualified inspector should document all findings.
Start by determining the entrance and exit points of electrical current. There will always be at least two contact areas. Inspect the boom, tower, subframe and chassis prior to operation. Take pictures of the contact points and any carbon tracking on the boom, if present. Clean soot from the fiberglass boom and perform a dielectric test. If the boom fails the dielectric test, it may need to be replaced.
If metal portions of the boom have arc marks, photograph them and note the location, size and depth of erosion.
It is important to inspect the inside of the boom in case flashover occurred. Flashover could cause other components to be damaged and may be evident by discolored paint. Note the size and location of these flashover symptoms. Keep in mind that all components between all points of contact will need to be inspected for arc marks and damage in the path between the points. This includes but is not limited to cylinders and boom pivot points.
If both the entrance and exit points of contact are not identified, all components from point of contact to ground level must be inspected for arc marks. These items may include rotation bearings and fasteners, leveling systems, outriggers and cylinders, gearboxes, electric and hydraulic swivel joints, and the vehicle. Be careful during these inspections, as escaping fluid under pressure can penetrate skin and cause serious injury.
Finally, once all information has been gathered, contact the manufacturer to determine if additional steps should be taken and if repairs are required to return to service. Repairs can be made in-house or by a third party, but they must be done according to manufacturer recommendations. Testing required to return the unit to service is determined by the location of damage and the extent of the repairs. Testing must be performed according to manufacturer recommendations and ANSI guidelines. While there is no set limit on the number of times an insulating aerial device remains serviceable after being subject to electrical contacts, the unit must be able to pass a structural inspection and dielectric test following electrical contact. Any insulating portion of the aerial device that is damaged and will not pass a dielectric test must be replaced, and then a retest must be performed before returning the aerial device to service.