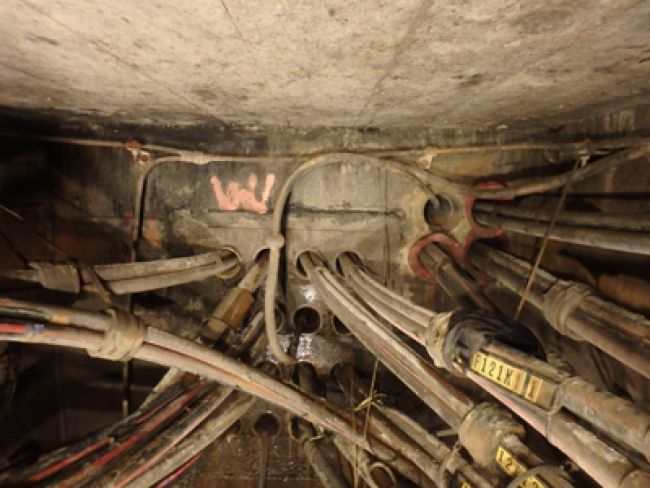
Underground Electrical Vaults: Safety Concerns and Controls
There are hundreds of thousands of man-accessible vaults in North America, with potentially tens of thousands of utility worker entries into those vaults each year. And it’s likely that every worker who enters a vault appreciates the safety procedures that govern the work. The combination of high-voltage electrical cables and aging infrastructure can exponentially complicate even the most routine vault-related task. In addition, many utilities across North America continue to report electrical vault failures, some of which lead to violent explosions.
For the most part, utility owners have a good understanding of the risks of entering man-accessible vaults and conducting work inside of them. There are many stories and equally as many opinions as to the safety and stability of the underground electrical network. The intent of this article is to summarize some known conditions your employees may face during execution of work in underground vaults. Although explosions may constitute the bulk of catastrophic events, thorough consideration of all hazards should be included in risk analyses.
The Vault
There is no uniform standard pertaining to vault configurations, but utilities regularly have an engineering standard. Man-accessible spaces can be as shallow as 8 feet deep with 340 cubic feet to approximately 30 feet deep with 3,000 cubic feet. Each vault is connected to others in the underground system through ducts and can have one to several high-voltage cable circuits passing through it. Some cables pass through directly while others contain splices, connections, transitions and some high-voltage switchgear or similar equipment. Most common cables are cross-linked polyethylene – often referred to as XLPE – or lead cable circuits. There is the potential for other systems to be present in spaces associated with lower voltages and communication cables. Some vaults have standard manhole lids while others have latch plates. The number of combinations is endless, but hazard exposure in these spaces is similar and can be categorized into exposure tables. When conducting your risk assessments, it is generally accepted in most jurisdictions to group your spaces by similar configurations of space and type. This will help organize information, reduce the volume of documentation and provide your field crews with clear data to safely perform their work.
Location
Many vaults are accessed along roadways. Traffic control is critical as vehicle traffic represents the greatest immediate hazard to workers at these vaults. Consider positioning your work vehicles in such a way that workers and the access point are protected from being struck by out-of-control vehicles and inattentive motorists. Additionally, configure your work zone to restrict access to the public, and install physical barriers around the open vault access point, which is a fall hazard.
Air Quality
Because vaults are interconnected spaces, this complicates a crew’s ability to ensure clean, respirable air for workers. If a crew is unable to seal off one vault from another, unknown contaminants may be introduced into the space. Just like water can flow along the ducts from space to space, other hazards – such as the following – have the possibility to infiltrate the vault.
• Hydrogen sulfide can be the result of organic matter buildup and filter in from adjacent sewers.
• Explosive methane may be present if a vault was constructed near old or existing waste facilities. Explosive gas may be found in a vault as a result of natural gas leaking into the space due to construction activity that caused damage to nearby supply lines.
• Carbon monoxide can be a result of combustion through work processes, motorized water pumps, generators and ambient concentrations of vehicle exhaust around the work zone.
In addition, oxygen deficiency may be caused by rusting components, microorganisms and displacement from infiltrating contaminants.
It is recommended that a vault be continuously monitored for atmospheric hazards throughout the course of the work inside the space, in order to provide immediate notification to workers if the air quality has been compromised. Oxygen, hydrogen sulfide, carbon monoxide and lower explosive levels (LEL) must be subject to baseline monitoring. Providing ventilation in the space for fresh air exchanges also delivers an additional barrier, especially if the work produces contaminants such as fumes from melting lead or LEL vapors from cable cleaning products. Assessing and understanding the sources of contaminants will help determine the most effective means of control.
Keep in mind that in certain situations, it will take more than air-quality monitoring and ventilation to provide vault workers with clean, respirable air. For example, heating lead will produce fumes at the source, exposing workers in close proximity to levels of exposure above safe and permissible limits. Similarly, drilling into concrete walls will expose workers to high concentrations of silica dust. Asbestos-containing materials also may be disrupted during the work process. Choose the correct particulate and organic filters and wear a half-mask respirator during such activities.
Biohazards
Vaults located in urban areas may be contaminated with a range of biohazards. This is because water from the street enters vaults and may leave potential biohazards behind. For instance, it is not uncommon in urban areas to find hypodermic needles in a vault. In extreme cases, utilities have reported finding several hundred discarded needles in a single installation. Discarded hypodermic needles are an extreme hazard and special training should be conducted on managing the risks. Their presence requires particular housekeeping procedures based on sharps protocols. The OSHA publication “How to Prevent Needlestick Injuries” is a good place to start. The information is for health care workers, but the risk here is exactly the same. Crews often overlook spaces that have no direct evidence of needles but are located in areas where the potential for needles exists. Looking on the ground may be deceiving because water may have caused a needle to float in between cables, just waiting for a worker’s hand to come into contact with it. Keep a sharps container handy and use designated pliers to handle the waste.
Vermin, Bacteria and More
A wide range of vermin may inhabit vaults and ducting. And by design, spaces can contain and promote the growth of various bacteria, fungi and mildew. Moderate to heavy buildup of matter should be handled by a qualified pressure cleaning and vacuuming service prior to the commencement of work. The use of disposable coveralls and impervious gloves is highly recommended in such cases, as are good hygiene practices prior to eating, drinking or entering the work vehicle.
Asbestos and Black Fiber Transite Ducts
In 2011, Canada closed its last two remaining asbestos plants after being one of the world’s largest suppliers. Asbestos-containing material (ACM) was once used in ducting materials, and its use was reportedly only discontinued in the early 1990s. Transite ducts contain 5 to 30 percent asbestos. Cable wrap also was once used extensively, containing 70 to 90 percent asbestos. Historically, black fiber ducts were commonly used and may release polycyclic aromatic hydrocarbons (PAH) if exposed to oil or other materials that break down the duct material. In all aging infrastructure, assessments are required to catalog the potential locations of ACM and PAH. Work procedures can then address the best and safest means of controlling exposure. At a minimum, a particulate respirator will be required for airborne ACM exposure, while impermeable gloves are required for exposure to PAH.
High-Voltage System Hazards
With regard to the hierarchy of controls, the best solutions are to de-energize, isolate and ground/bond high-voltage systems prior to work. Utility employees have the capability to perform these actions with some systems, but others restrict the ability to de-energize all circuits inside a vault. There are, however, a number of other controls to consider for work inside energized vaults. Keep in mind that electrical assessments must be made by competent personnel who have undergone the necessary training about high-voltage electrical cable. Upon entry into a vault, hands-off assessments that can detect hazards include:
• Looking at splices for leaks, swelling, collapse and other potential imminent failures.
• Listening for electrical tracking or arcing.
• Sniffing the air for a burning smell.
• Identifying loose high-voltage connections or loose cable racks that are stressing splices.
• Determining the temperature of the cables, splices and connections.
• Looking for vandalism. Many vaults can be accessed by the public, and I am aware of several reports of neutral conductor and ground/halo harvesting.
For supplemental information, see “Practical Underground Safety: Handling Neutrals and Rescue” by Jim Vaughn, CUSP (https://incident-prevention.com/blog/train-the-trainer-101-practical-underground-safety-handling-neutrals-and-rescue).
Temperature readings of splices and connections are the most common objective data used to determine a potential imminent failure. Utilities usually have engineering data that represents normal operating temperatures as well as temperatures that have been known to produce failure. Consider that cables and splices that have been submerged in water prior to worker entry may have been cooling and now – subject only to ambient air temperature – could pose a delayed failure risk. Monitor temperature regularly in such cases or in situations when readings are above normal or climbing. You should obtain system operating data from the owner of the system to use in your hazard evaluation. Advances in thermal imagining have resulted in the development of hand-held units that can quickly provide a visual spectrum of temperature values to determine hot spots. Considering some vaults can have more than 20 circuits, a method to quickly assess temperatures within the space is critical. For vaults that are already known to have a potential imminent failure, thermal cameras are emerging on the market to assess cables without the need for anyone to enter the vault.
Avoid leaning on energized cables and splices. Treat them as brush contact only. Take great precaution when climbing in and out of the vault not to step on a high-voltage connection, which may become inadvertently dislodged. Utilities normally perform arc flash studies on their systems to determine the level of arc flash clothing required. Obtain such information from the utility owner in order to understand and apply the PPE requirements. There is research available on the use of arc suppression blankets as an option to reduce the damaging effects of splice and connection failure. A good article by Michael R. Mulvaney and Victor L. Petrovic – “Arc Suppression Blanket Installation” (https://incident-prevention.com/blog/arc-suppression-blanket-installation) – provides more information on this topic.
Communication with the plant owner is essential. Verify all circuits in the space have been accounted for and that the appropriate circuit protections are in place. If you are fortunate enough to work in a vault that is clean with legible cable tags, never lose focus as cable configurations and circuits can change in adjacent vaults. Understand your orientation in the vault in terms of the prints you have been given. Once you are ready to work on a circuit, be sure to take the proper precautions and positively identify the cable prior to exposure. It is highly recommended that workers exit the space during any remote switching. Additional loading of circuits may elevate the potential for failure. Prior to commencing work, you should once again perform all temperature testing to verify that switching has not caused any increases.
Rescue
Most single-chamber spaces are accessible by ladder, so workers may be able to exit a vault on their own in the event of an emergency. However, in some cases you may be waiting for emergency services to arrive and conduct a rescue. Most emergency medical personnel will not enter a space, especially if electricity is involved. If your assessments indicate that there is moderate risk of the space becoming immediately dangerous to life and health, and rescue could be compromised, your system of rescue must include a means to safely extract workers. Some options are:
• Tethering your workers inside the space. Using a high-strength, high-heat-resistant rope, extracting workers from a single space can be performed quickly using a man-rated winch. Because traffic is a major hazard, there are options for open winch systems that remove the line from the winch in case a vehicle strikes the rescue system.
• A rescue stick that can be lowered into the space and, using a quick-release spring clip, attached to a harness and connected to the rescue line winch system. Keep in mind that this method is more appropriate for open-hatch spaces where the stick can access all areas of a space.
• Third-party self-contained breathing apparatus rescue. Train your workers how to perform this type of rescue, or contract with a third party that can provide specially trained personnel to act as standby crew members for the purpose of vault rescue. Hiring a third party is a reasonable option for more advanced vaults with multiple stages or chambers.
Underground vaults present numerous hazards, but thorough planning and communication with plant system owners can mitigate many risks and allow for safe access. Understand the nature of the spaces and work closely with your qualified electrical crews.
About the Author: Chris Grajek, CRSP, CUSP, has been Allteck’s director of health and safety since 2006. He leads a team of trades trainers and field safety coordinators for local and international construction and maintenance activities. Grajek is also involved with a number of transmission and distribution partnership task teams and provides instruction on a wide range of utility-driven training initiatives. He can be reached at cgrajek@allteck.ca.