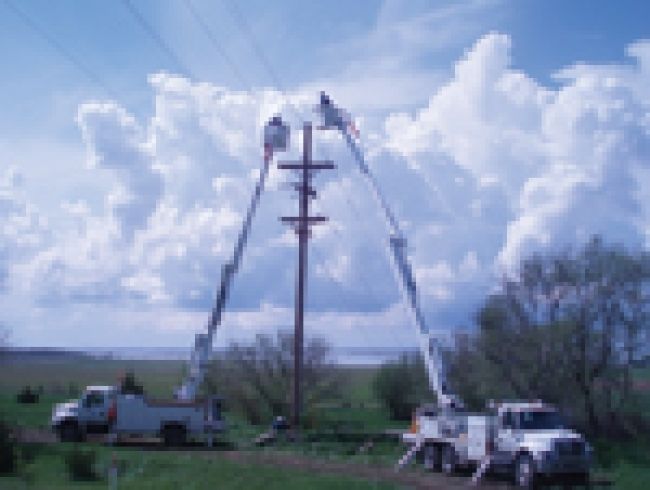
T&D Safety Management for Crew Leaders
In iP’s earlier installments of the Supervisory Series (April 2011, June 2011, August 2011 and October 2011), we discussed the importance of career development for lineworkers targeted for supervisory responsibilities. We also considered the supervisory skills required to be effective as a crew leader or foreman, including a full article on human behavior and communication skills. In the last issue we dealt with the concept of crew best practices.
In this installment, we will focus more on crew practices, specifically those concerning crew safety management.
Safety Attitudes and the Corporate Culture
Many crew foremen may ask, isn’t safety management the responsibility of the safety department? Crew members may be wondering the same thing. In one sense they are right, aren’t they? Management has a broad corporate and legal responsibility for safety, and quite often organizations will have a separate department to help manage their responsibilities. But in another sense – the bigger picture – safety is everyone’s responsibility. If the crew foreman and crew members are asking this question, they haven’t internalized the concept of safety as a personal responsibility. It could be that the corporate culture is to blame.
“Culture” is a word we often associate with the society of a nation or a region of a country. However, culture is also a concept that can be applied to a single company or even a department within a company. Every utility and every contractor has a company culture. Each department within that organization is likely to have its own culture as well. That departmental culture can mirror the culture of the larger organization or be at odds with broader culture of the company.
Often, cultural differences within the various departments of an organization are greatest when it comes to safety. For example, safe work practices may be enforced in the office or at the generating plant, but may be relaxed during field operations involving transmission and distribution (T&D) crews. It is, however, the T&D operations department of a utility or the field operations of a contractor that are frequently exposed to the greatest risk. Crews are expected to repair lines and equipment at night or during storms. But even during routine maintenance of the system, high-voltage electricity is unforgiving, allowing no mistakes without serious consequences. The lack of safe work practices often poses life-threatening hazards to lineworkers.
The safety culture of the organization’s T&D operations department, as we will see, is a key performance driver that determines how the employee internalizes safety as part of his or her job.
An Attitude of Compliance
We often find an attitude of compliance within the field operations of utilities and contractors. That sounds pretty good, right? If our people would just comply with the rules and regulations, everything would be fine. Why don’t they just obey the rules? When management has this attitude, we naturally see it permeate the culture of the organization from top to bottom. OSHA, NESC, DOT, the safety department, the safety manual – everyone has rules and regulations that need to be complied with. “It is my responsibility to comply with the rules and regulations,” employees think, and the company culture reinforces that thinking. The crew foreman becomes the champion of compliance, because too often, that is the only thing by which he is measured.
However, does management truly want the workers focusing on compliance, or does management want the workers doing what’s required to stay safe in the workplace? I think the latter. Is compliance with rules and regulations part of staying safe in the workplace? Most likely, but it is a means to an end and in reality just one of the tools used in staying safe. Compliance is not an end unto itself. When we demand that employees focus on compliance with rules and regulations, we miss the point.
The industry’s relationship with OSHA regulations is a good example. The agency has accumulated a wealth of important information about safety and safe work practices for our industry since its inception 40 years ago. The information is specific, often detailed and can be a valuable resource for a crew foreman in managing safety. Unfortunately, during that same 40 years, OSHA has earned a reputation for being a policeman – an enforcer of regulations, rather than the partner in safety that they truly wish to be. Too often, our crew foremen are forced to worry about OSHA inspections and fines rather than how OSHA regulations can be another tool for them in their safety tool bag. Compliance with everyone’s rules and regulations has a place in crew safety management – just not first place.
Where to Begin
The safety culture in any organization must begin with acceptance of personal responsibility for safety – your own and that of others. Safety for all workers is truly a value within an organization and the culture begins to change immediately when management accepts it as such. We talk about our values. We display our values. We are proud of our values and tell our customers why our values make us special. We expect our employees to adopt our values. Safety is a value and each employee has a personal responsibility to perform to the expectations of our values.
When the crew foreman has crew members who have accepted personal responsibility for safety and embrace safety as an important value for success, the foreman’s job is much easier. It’s then like he’s preaching to the choir. Safe work practices become an integral part of the job and are not seen as something extra or burdensome. Consideration for safety is integrated into everything the crew members do. Safety becomes front of mind, where it truly needs to be for superior performance.
On this foundation of personal responsibility and safety as corporate values, the crew foreman can create a safety tool bag that will serve him and his crew members well.
The Safety Tool Bag
Safety for powerline crews is not a thing – it’s a process and a rather creative one at that. Crews are expected to work on multiple job sites within a typical day and each one is likely to be different. This variety makes the job more interesting, but can be a safety hazard in itself. So, the crew foreman and crew members must not become complacent. They all must remain alert to the unique hazards that they face at this site that they didn’t face at the last one. For the foreman, this means that our plan for staying safe on this job is unique. A good pre-job briefing can help here. With everyone involved in observing and planning, hazards can be identified that are both typical to the work, but also unique to this job. We discuss the tools, equipment and work processes we’ll use and who is responsible for each part of the job. We’ll also discuss emergency action plans and not assume everyone automatically knows what to do if the worst happens. Good preparation can be a good safety practice.
Does the foreman need to know all the rules and regulations applicable to the work required for this job? Absolutely. Does he need to know this in case OSHA drives by or a company manager may be watching? Those concerns should be the last things on his mind. If the crew leader is following all the rules out of fear of retribution, he’s following them for the wrong reason. The rules and regulations are wonderful tools to help him keep crew members safe. Encourage the foreman to not just read them, but look beyond the printed words. Each rule, each regulation has a deeper message – a spirit, if you will. For example, OSHA’s 1910.269(a)(2)(vii) regulation states, “The employer shall certify that each employee has received the training required by paragraph (a)(2) of this section.” OK, so we’ll make sure that our workers are trained. We’ll talk about PPE at the next safety meeting. The foreman may be in compliance with the letter of the law by doing this, but he has completely missed the spirit of what is needed.
Training, in this sense, is referring to proficiency in both knowledge and skills. For powerline workers this will almost always be the case. Rather than just recite something, they need to perform it, to become proficient at it. For example, it’s not enough for a crew member to explain proper care, use and maintenance of PPE – he needs to demonstrate proficiency at it to truly be trained. Each rule and regulation has a deeper meaning and expectation that the foreman should understand. Compliance with the letter of the written word is not good enough.
The company safety department is another wonderful tool often available to the crew foreman. A tool? The safety department is a tool? Yes. The safety department is another resource for the crew foreman. The best-performing organizations have established the safety department as a support function to operations. They should not be the police department. The safety department is there to help the crew foreman do his job. Legally, management has the responsibility to enforce safety regulations within the company, but operationally, the foreman should be the enforcer. When the safety department is tagged with enforcement, they too often become the enemy of the crew rather than the partner in safety that they should be. This means that safety managers and representatives must have a servant attitude and recognize that their success is in direct correlation to how operations perceives and uses them.
The crew foreman’s safety tool bag is probably bigger than he realizes. We’ve mentioned a few resources above that are likely not considered a resource by the foreman. Sometimes the crew foreman’s own attitude may be his biggest hurdle in safety management. Often, when we look at things differently, they suddenly become different for us.
Begin With the End in Mind
Author Stephen R. Covey suggested that one of the seven habits of highly effective people is to begin with the end in mind. That’s a good idea for crew safety management as well. Where do we want to end up? What does success look like in crew safety management? In defining that success, most people will include the attitude of the worker. We want the worker on that crew to have a good attitude about safety. Another element of success may be personal responsibility. So many things become easier when we accept personal responsibility for safety.
Being accident- or incident-free, and sending our people home each evening with the same health they started with that morning, is usually a measure of success as well. The powerline crew foreman will have much influence on the success or failure of any measure we put in place. Let’s arm these crew leaders with the best management and supervisory practices available to help them succeed.
About the Author: Ronald J. Schenk, CUSP, is the executive director of the Institute for Safety in Powerline Construction (ISPC), an electric utility industry association focusing on safety and training for lineworkers. His career in the utility industry spans 21 years and includes 14 years on staff with an Engineering News-Record (ENR) Top 5 powerline contractor where he served as director of training for 1,800 lineworkers. For more information, call 866-880-1380 or email Schenk at ron@ispconline.com.