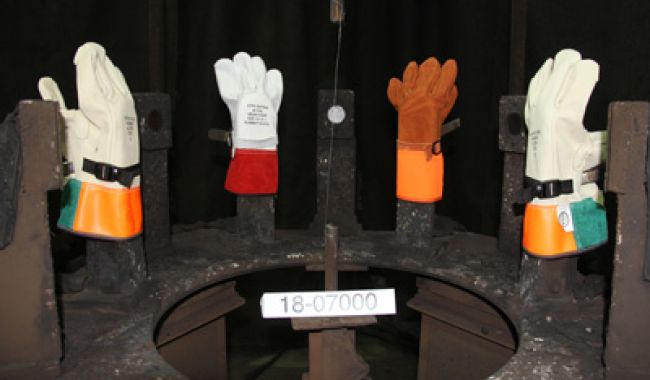
Specifying Arc-Rated and Flame-Resistant Gloves
Until recently, standard specifications and conformity assessments of flame-resistant (FR) gloves fell into no-man’s land. While many end users have requested FR gloves, there has not been a standard in the industry for manufacturers to use to specifically label their gloves as flame resistant. In 2013, ASTM F18 set forth a standard for testing gloves in arc flash exposures to provide an arc rating; ASTM F2675 offered arc ratings for gloves, but F696 protector gloves and D120 rubber insulating gloves were excluded. This did not prevent testing of rubber insulating or protector gloves, but many manufacturers would not label their gloves because of these exclusions. Most arc-rated (AR) gloves on the market are work gloves designed as ground gloves or for low-voltage operations to protect from arc flash, but they have no shock protection. This has created a challenge for manufacturers in the marketplace – they are left to decide on their own how to test and interpret their product to make such claims. To further complicate matters, gloves in the AR and FR PPE industry have become increasingly complex to offer better grip and protection from multiple hazards (e.g., impact, cut and puncture), with designs that include extra components that may ignite under certain conditions. With these changes in the market, how can you be sure you’re specifying what you need when it comes to hand protection?
Legally, hand protection is required for workers in many settings. The most common protection in the electric utility industry is for shock hazard. Rubber insulating gloves meeting ASTM D120 are the norm and are mentioned in OSHA, the National Electrical Safety Code and NFPA 70E. Other common needs are cut and puncture protection, either for the voltage-rated glove or for direct protection of the hand. Additionally, arc protection has long been assumed to be provided by leather protectors – this is mentioned in NFPA 70E – but over time leather protectors have migrated away from pure leather to include melting components like PVC polyester cuffs and nylon straps. OSHA specifically prohibits apparel with polyester but does not mention protector gloves. If gloves are worn against the skin, without the rubber insulating gloves, it should be assumed that this cuff could melt onto a worker. We recently investigated burns on a worker’s hands from melting gloves. The worker was racking a breaker with work gloves but was not wearing rubber gloves; the melting gloves caused life-changing burns to the worker’s hands. Most exposures in overhead line work would not be expected to ignite rubber or protector gloves. The PVC/polyester used has a flame retardant, but like the melting rainwear we used to use, it can ignite, and when it does it will melt and continue to burn. This testing was performed in December 2018 for the next ASTM F18 meeting and demonstrates the potential hazard of protector gloves on the market today, especially in conditions greater than 20 cal/cm².
Five Steps to Glove Specification
So, how can you specify gloves to get the PPE characteristics you want? Follow these five steps.
Step 1: Use the proper standard and understand its focus and limitations.
The right standard goes a long way, but you must fully comprehend the standard and how to apply it to your work conditions. We are in the infancy of AR and even FR gloves. New test methods in flash fire for gloves will help, and further specifications for AR gloves will make the landscape easier to navigate.
ANSI/ISEA 105
In the absence of a consensus standard to specifically address FR gloves, many manufacturers use ANSI/ISEA 105, the American National Standard for Hand Protection Classification, which is a document utilized for the classification of different properties of gloves. The standard includes classification for mechanical qualities, such as cut and puncture, but it also includes classification for gloves intended to protect from heat and flame. ANSI/ISEA 105 cites small-scale methods, like impingement flame and oven testing, but there is one problem with the classification system: There is no information on how to translate the classifications into what is considered FR in the marketplace. This standard also does not mention ASTM F2675, so for arc flash, one must use additional criteria to assure your gloves meet the criteria you need. The ANSI/ISEA 105 committee is adding impact testing to a new version of that standard, but the flame resistance needs a “buyer beware” warning. Make sure you understand what the manufacturer’s test data means. Cite additional tests if needed. ANSI/ISEA 105 is self-certified, so check the quality of the data from the manufacturer and ask for third-party data when available.
ASTM F2675
In 2013, ASTM F2675 for AR gloves was released. This is a test method – not a specification. It is a large-scale method for evaluating gloves in an arc flash, and the result is an arc rating or a probability of ignition, or both. The arc rating applies to materials that do not show evidence of melting and dripping or ignition in testing. Even this standard is improving with a required ignition withstand threshold for leather and other glove components that can ignite. This has been approved by the ASTM F18 committee and was published in January as ASTM F2675-19. The new version addresses how to properly test gloves with extra components – like thermoplastic rubber (TPR) impact protection – for their propensity to ignite, melt and drip. Our test lab has evaluated gloves for melting and ignition above the arc rating for several years, and now it will be required by the standard. Most TPR is ignitable at some level. AR gloves need special consideration as the arc hazard typically is calculated from 18 inches away. A worker’s hands often are much closer to the exposure, which means the incident energy is higher, but many factors must be considered, like movement and hand positioning. Our test uses a long arc, which produces more surface area of exposure to energy – and especially to the infrared energy – than the average arc exposure, so this test is quite harsh on ignition. This standard is self-certified, but all testing is done by third parties.
How is the AR/FR Glove Market Evolving?
Before we move on to Step 2, it’s important to reiterate that the glove market is changing, and soon compliance won’t be so complex. Gloves recently were added to the NFPA 2112-2018 flash fire standard, although it may be some time before you see compliant products on the market; a new ASTM standard is underway for arc flash protector gloves; and the IEC has added a standard to begin development for AR gloves in general. Current test methods also are being revised to better accommodate the products entering the market.
Through its Textile Protection and Comfort Center, North Carolina State University also is working on a new test called PyroHand – similar to ASTM F1930 – to test gloves for flash fire. This standard could be used in NFPA 1971, which includes gloves for firefighters, as well as NFPA 2112 and other standards. These standards currently use small-scale testing that has correlated to protection for firefighters. The PyroHand may be another addition in the future to help evaluate gloves in a large-scale exposure.
Arc Flash Glove Specification
A new standard for AR protectors is underway, and this standard is expected to encompass protectors designed to be worn over rubber insulating gloves and mittens – which may be made of materials other than leather. The specification will include details for testing the cut, puncture and arc flash properties of protector gloves using the ASTM F2675 test method. The protector standard will allow for a broader range of protector gloves that protect against multiple hazards. While leather has served well since the 1800s, it has limited cut resistance, and cut resistance can only be increased by thickness and stiffness, which, in turn, decrease dexterity. In addition, some end users feel leather does not provide adequate grip when it’s damp. There is an increased demand in the market for protector gloves that will protect users from multiple hazards and have other characteristics positive for the workforce. The new glove styles likely will be focused on low-voltage applications, which require increased finger dexterity, but lower weight and better cut resistance could be in the offering for lineworkers doing overhead line work.
NFPA 2112 for Flash Fire
The NFPA 2112-2018 edition has been released and does include gloves. NFPA 2112 requires third-party certification by an ISO 17065-accredited body; acceptable bodies in the U.S. include the not-for-profit Safety Equipment Institute and the for-profit UL. Previously, gloves were not covered by the scope of the standard, so this is the first edition that includes hand protection. No large-scale method is required for gloves, but a series of small-scale testing is cited for compliance, including a 500-degree-Fahrenheit oven test, flame testing and heat transfer performance.
OSHA recommends NFPA 2112 or an equivalent for those drilling in the oil and gas industry, so the addition of gloves, shrouds, hoods and balaclavas to the standard may create a higher demand in the marketplace for products that comply with NFPA 2112. Most leather will not meet this new standard since the specification was written around the firefighter glove standard testing, but many cut-resistant and AR gloves will meet the standard.
Step 2: Choose the levels of protection you want for your work location.
Common characteristics that companies may wish to consider in gloves – and that can be specified with the above standards – include arc rating; cut-protection levels; puncture resistance, which may be most important on the palm; impact resistance (specify that this not ignite at a certain level); abrasion resistance (leather is exceptional); dexterity; and chemical resistance.
Step 3: Educate your workforce.
If your company uses AR gloves, be certain that workers understand that an arc rating has no shock protection unless it is a D120 rubber insulating glove. Electrical workers will know this from their training, but this must be clear to operators if they have limited electrical training.
Step 4: Enjoy the new protective values and comfort of the products.
Innovation in gloves was very apparent at 2018 shows like the National Safety Council’s Congress & Expo and the American Society of Safety Professionals’ safety conference, where it seemed about 25 percent of the exhibiting companies were selling gloves with different characteristics. These new and upgraded standards are setting innovators free from leather as the sole material for gloves.
Step 5: Stay ahead of the curve.
When choosing gloves for an arc flash hazard, consider both the shock hazard and the arc flash hazard. If there is a shock hazard, ASTM D120 rubber insulating gloves should be worn under an arc flash protector, and most choose protectors meeting ASTM F696 at this time. Consider the distance from the arc flash in relation to a worker’s hands; calculations are performed 18 inches away, and the hands typically are closer to the hazard, but most companies still use the AR calculations for choosing gloves. The geometry, placement of gloves in proximity to the hazard and movement of the hands seem to back this for the time being. The OSHA 29 CFR 1910.269 standard requires AR gloves when the hazard is above 14 cal/cm². If the glove contains thermoplastic rubber or other ignitable components, you might ask to see a copy of the test report to verify that the finished glove has been checked at a level well above the ignition rating.
You may see gloves rated with HRC, PPE categories or AR protection levels in accordance with NFPA 70E. This is not required, but because many end users are familiar with the levels, a good number of manufacturers choose to include this information on labels. It is appropriate for gloves that have been arc tested to determine an arc rating.
As for flash fire, gloves recently were added to the NFPA 2112 standard, but because NFPA 2112 requires third-party certification, it will take time for compliant gloves to hit the market. In the meantime, choose gloves made of nonmelting materials that have been tested, at a minimum, to small-scale heat and flame tests to evaluate for the propensity to melt and drip or ignite. You might even ask for test results to the NFPA 2112 standard, even if full certification has not been completed, to show that the products at least meet the minimum testing requirements. Multihazard gloves soon may be entering the market to cover arc flash, flash fire and other common hazards found in the workplace.
Our recommendation is the same for gloves as it is for clothing: Consider the hazard, and specify for the real hazard, avoiding the simplistic terms “flame-resistant” and “self-extinguishing,” as these may not mean anything for your hazards. Flame resistance is defined by NFPA 2113 as the “ability to self-extinguish,” but the ignition source is not defined – and the ignition source is important to consider in the big picture of protection. “Self-extinguishing” really means nothing for protection in most cases. The same is true in consideration of other hazards like cut, puncture and chemical resistance. The ANSI/ISEA 105 classification document is very useful for these mechanical hazards, but it can be difficult to correlate the classification levels of the standard to real-life hazards. AR gloves are much easier to correlate than cut-resistance levels, for instance, but guidance is out there.
Further, one cannot assume that clothing or gloves that work well with a propane torch have the same functionality in an arc flash or flash fire exposure, so cite appropriate specifications, or even test methods, when they exist.
- Arc flash: ASTM F2675 for arc ratings
- Flash fire: NFPA 2112
- Mechanical protection (cut, abrasion, puncture): ANSI/ISEA 105-16
- Vibration protection, dexterity, heat and flame classification: ANSI/ISEA 105-16
- ASTM F696 can now be specified in all leather or with an arc rating, if desired.
- ASTM D120 can be specified with an arc test level. Rubber will ignite at some level, so specify a level at which you want no ignition based on your assessment.
With the new ASTM F2675 and the proposed ASTM protector glove standard, specifying gloves with a cuff that does not ignite and melt will be as easy as specifying the new standard. The other standards discussed can get you all the requirements you want to help keep workers protected and productive. These guidelines can help you make them a little happier, too.
About the Authors: Hugh Hoagland is an expert on electrical arc testing and electrical safety. He has helped write standards for ASTM, NFPA and IEC/ISO to protect against electric arcs and flash fires. Hoagland works for ArcWear (www.arcwear.com) and e-Hazard (www.e-hazard.com), performing arc testing, consulting and electrical safety training.
Stacy Klausing, M.S., is project manager for ArcWear, works on many standards committees, and heads projects researching textile and PPE response in testing. Her master’s thesis was on used firefighters’ turnout gear.