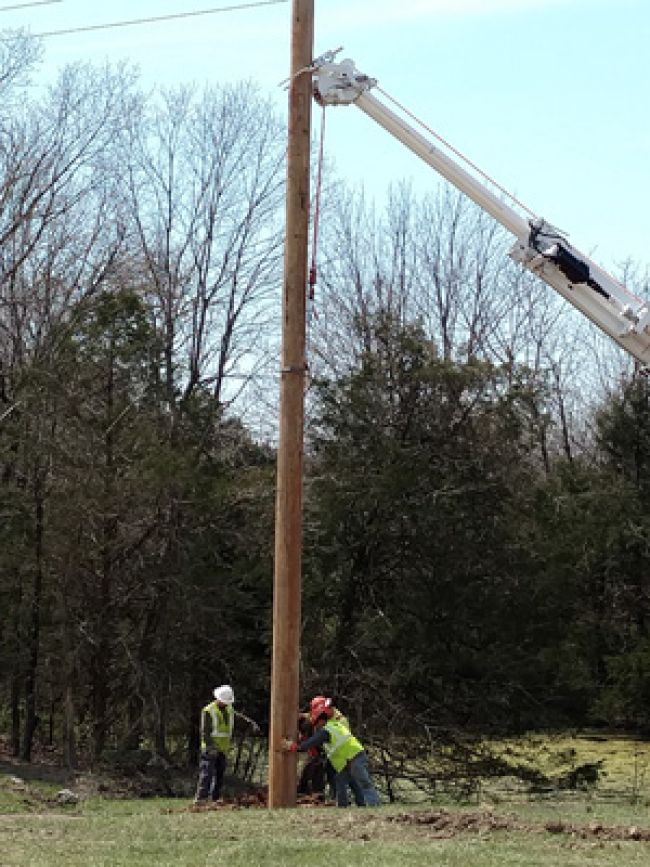
Safety Concerns When Setting Wooden Utility Poles
On an invigorating and beautiful late-spring Sunday afternoon, Frank decides to take his young family for a drive in his brand-new van. Frank, his wife and their two young daughters are cruising along with a scenic view of the mountains. He is enjoying this priceless quality time with his family. While listening to some good music on the radio, the van approaches a tight curve on the road. Suddenly, Frank notices a large wooden utility pole ahead that is carrying lots of wire and leaning excessively toward the road. Frank jams on the brakes, but he cannot stop in time. He hits the pole, and the impact splits the pole and damages the van. All wires are hanging low, but they’re not touching the van or the ground. Frank parks on the side of the road and then checks on his family. Thankfully no one is hurt. However, Frank gets a headache just thinking about the deductible he is going to have to pay his car insurance company to fix the vehicle.
Later, police and emergency personnel arrive on the scene. Frank’s family is taken to the nearby hospital for checkups. Everyone is OK. The police summon the local electric utility to the accident site. The utility responds immediately and assigns the emergency to Bob’s crew. Bob is a foreman with many years of experience; he is known to be tough and demanding yet compassionate. Over the years, his co-workers have nicknamed him “By-the-Book Bob” and “S&P Boss” – “S&P” standing for “safety and productivity.”
Bob assembles his crew and instructs them on the situation. He then reminds them of his basic “CSS” rule that applies while any utility employee is behind the wheel. The three components of the rule are as follows:
- Cellphone use is banned while driving.
- Seat belts must be worn when the engine is running.
- Speed limits must be obeyed.
After meeting with the crew, Bob gets in his pickup truck and heads to the accident site. Upon arrival, he checks out the situation, identifies all hazards and plans mitigation. The police officers on-site inform Bob that they must leave soon to attend to another emergency, so Bob calls the control center to request flaggers to control traffic in the area. Soon, both the flaggers and the overhead emergency crew arrive. Construction trucks are positioned next to the broken pole. Overhead facilities are hanging low. Bob assembles all crew members and flaggers to perform the pre-job briefing, as required by OSHA 29 CFR 1910.269(c) and 1926.952. All aspects of the job are discussed. Crew members ask questions and address safety concerns. Everyone signs the pre-job briefing form, and then they get to work. Bob deploys the flaggers to their spots to control the traffic flow around the job site. He makes sure that all the flaggers are wearing the required PPE, and that they are using the “Stop” and “Slow” paddles on 6-foot staffs. He knows that flagging operations must adhere to the Manual on Uniform Traffic Control Devices.
Digging Procedures
Once the work setup is complete, the crew begins to stabilize the situation. Due to concerns for the safety of the public, Bob decides that the broken pole must be replaced immediately. He calls the control center and requests that a new 50-foot, Class 2 pole quickly be delivered to the site. A CCA-treated southern yellow pine pole is soon loaded onto a pole trailer and properly secured per Federal Motor Carrier Safety Regulations. The overhanging pole section is clearly marked with red flags, and a light bar is attached to the end of the pole. The pole is then delivered to the job site.
Bob then makes an emergency call to the Dig Safe center to report the emergency dig requirements. All operators of underground facilities within a 15-foot radius of the digging spot are notified. However, since there is no time to wait for responses from the operators, hand-digging with extreme care commences. The crew starts to hand-dig a foundation hole a few feet behind the broken pole, which had been set too close to the road curb line. Although this is an emergency situation, Bob knows that for non-emergency, planned cases, it is recommended that the following digging procedure be followed:
- Call the Dig Safe center two to 10 days before the dig is set to begin.
- Write the Dig Safe ticket number on the pre-job briefing form for the job site.
- Read the Dig Safe ticket information carefully before any digging begins.
- If there is a delayed response from any operators of underground lines, contact those operators before any digging starts. If any digging is to be done, it must be hand-digging performed with extreme care.
- Using the internet, verify from the job site that all underground facilities are clear. Check the status of existing tickets, or obtain a printed copy of the one-call response ticket from your supervisor when possible.
- Always hand-dig if you are working within the 24-inch zone on either side of the mark-out line.
- Always hand-dig if the ticket information states “unverifiable,” “discrepancy” or another disclaimer.
- Complete all the following tasks if an unknown, unreported underground line is inadvertently hit:
- Immediately notify your supervisor and the line operator.
- Call 911 and start the evacuation process if the line is gas, petroleum or another dangerous substance.
- Safeguard the area and keep all non-emergency responders away from the site.
- Safeguard all unguarded or unprotected pole holes to avoid an accidental fall into a hole; for more information, see OSHA 1910.269(q)(1) and 1926.964(a)(3).
Assuring Personal Safety
Since the replacement pole must be set near energized conductors, Bob knows that OSHA mandates the following requirements be met to assure personal safety:
- Cover up all energized conductors and equipment before the pole is raised with the boom and winch of the line derrick truck (see 1910.269(p)(4)(iii) and 1926.959(d)(3)(i)).
- Ground the line truck with the best available ground – in this case, the system neutral – and keep all personnel away from the grounded truck unless an equipotential mat is placed on the ground and the truck is barricaded (see 1910.269(p)(4)(iii)(C) and 1926.959(d)(3)(iii)). Use 2/0 copper conductor grounds or another conductor size depending on the expected available fault current at the site.
- Any person near the line truck or touching the truck must wear approved rubber gloves with leather protectors and insulating sleeves.
- While the pole is being raised, the person guiding the pole to the foundation hole shall wear approved rubber gloves, leather protectors and insulating sleeves, and none of his or her body can touch the pole (see 1926.964(a)(3)(ii)).
- Assure that the pole, the winch line or any part of the boom does not damage any existing overhead lines. Relocate any lines as needed to avoid inadvertent contacts.
- Use a pole cover or insulating guard, especially on any pole parts that could contact live conductors.
- Make sure the hole that’s been dug is deep enough. Usually, the rule of thumb is to get a nominal depth, in feet, equal to 10 percent of the pole length plus 2 – this is the butt-to-ground line distance used by ANSI 05.1 for poles set in ordinary soil. However, if the pole is set at curves, corners or points of extra strain, the best practice is to increase the nominal depth by approximately 6 inches, and if the pole is set in a rock hole, then the nominal depth could be reduced by up to 12 inches.
- Align the pole once it is embedded in the hole. Since the pole will support angled facilities, it should be raked, using key and crib, to minimize leaning once the lines are transferred from the broken pole. A strong and properly sized anchor guy, connected to a screw anchor, which must be set deep enough in virgin soil, also must be attached to the pole to prevent any future leaning as well as any future accidents.
Once the pole is set and secured, with all clean backfill properly tamped around its perimeter up to grade, Bob’s crew starts the prep work to transfer all required electric facilities to the new pole. In addition, the non-electric facilities are roped to the new pole to keep the area safe. All telecom operators are notified accordingly. After the work is done, all debris is picked up and the area is cleaned. Bob reassembles the crew and performs a post-job briefing, noting any lessons learned. Bob is satisfied and proud of his crew for a job well done.
About the Author: Luis Ortega, CUSP, works for Northline Utilities LLC as a safety specialist. Prior to assuming his current role, he retired from Consolidated Edison Co. of New York City after a 30-year career. Ortega holds a technical certificate from Power Technologies Inc. and earned a bachelor’s degree in civil engineering from the City College of New York. He can be reached at lortega@northlinellc.com.