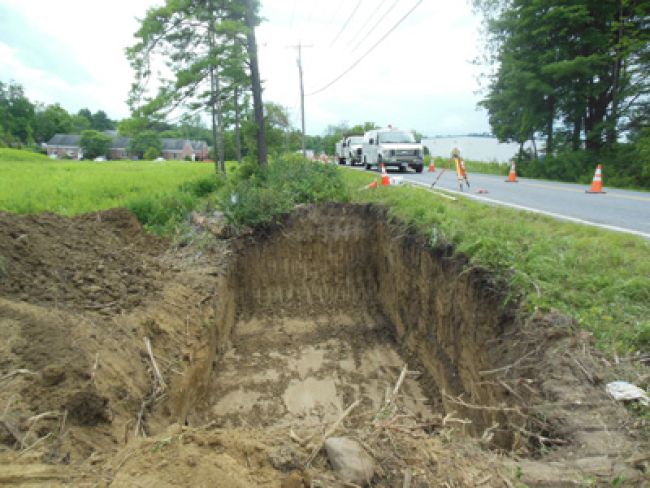
Protective Systems for Trenching and Excavations
This is the third installment of a four-part series on trenching principles. “Trenching by the Numbers” (http://incident-prevention.com/blog/trenching-by-the-numbers), the first article in the series, presented a simple method for recalling OSHA’s trenching and excavation requirements. The second article focused on soil mechanics (http://incident-prevention.com/blog/soil-mechanics-in-the-excavation-environment), taking an in-depth look at the behavior and characteristics of different soil types and their relationships with water and air. In this article, we will discuss the four different protective systems described in OSHA 29 CFR 1926 Subpart P, “Excavations”: engineered design, timber shoring, shield systems, and sloping and benching. Each system has its own unique strengths and weaknesses. Thus, depending on the environment and the circumstances of the work to be done, one system may be a better fit than the others. Let’s take a closer look at all four systems.
Engineered Design
Engineer-designed protective systems typically are not used in utility operations. Instead, this type of system is more likely to be seen on large-scale building foundation work, and it may also be used on complex construction projects, such as around waterways. In any case, some activities – like those that involve deep, poured-in-place vaults or occasions when a duct bank has to pass beneath water and sewer – may benefit from an engineer-designed system customized for the situation. The need for engineered design may be rare, but knowing what it is and why it is used is necessary information for project and safety planners.
This type of protective system has two primary advantages. First, although it can be used at any excavation depth, according to the OSHA excavations standard, this is the only system allowed to be used when excavations take place at 20 feet or more. Additionally, engineer-designed systems can be tailored to the work. For instance, in a horizontal bore, the engineer can design a protective system that will allow for the placement and recovery of large sections of pipe and equipment. In other systems, cross-bracing can make this difficult, if not impossible.
What are some of the downsides of engineered design? For starters, the engineer who completes the design must be licensed in the state in which the work is to be done. While this usually isn’t a problem, it can sometimes be a challenge for contractors and utilities that operate in multiple states. Another potential problem with engineered design is that the field foreman or crew chief has far less flexibility when attempting to solve issues that arise in the field. When unforeseen circumstances arise, only a professional engineer can approve alterations to design specifications.
Timber Shoring
Engineered design is usually the least likely protective system to be used for trenching and excavation, and timber shoring is the second least-likely system to be used. Like any of the four protective systems, it also has its pros and cons.
Although it is not utilized frequently across the country, timber shoring is the only system used in many large metropolitan areas. This is because of the great number of utilities that congest city streets and sidewalks. In New York state, outside of New York City, there are typically four to five utilities that are notified prior to an excavation. In New York City, that number jumps to 20 to 25 utilities. According to the OSHA excavations standard, the excavator has the responsibility to support and protect exposed utilities, and the timber shoring method is often best suited for this task.
Another pro is that the competent person has a larger degree of flexibility with timber shoring than with other methods when determining the size and shape of the protective system. A 20-foot trench shield, for instance, will always be 20 feet long. Timber shoring systems are “built to suit,” so to speak, and thus allow for a wide range of shapes and sizes.
One of the downsides to timber shoring is that there is a steep learning curve, especially if an organization is just getting started versus only having to train one or two new workers. In addition, training is tiered; the rank-and-file worker needs to understand how to build the system and what the components do, and the competent person needs to be able to determine what type of components – and how many of them – are needed.
Material availability can be a challenge as well. A large volume of timber often is required. To compound matters, once a timber is sized and placed, there is the possibility that it will be too small to be used again on the next system.
Shield Systems
Today, shield systems are probably the most commonly used protective systems in the field, and they have come a long way in terms of the features they offer. One of the upsides to conventional shield systems is their wide industry use; because workers are familiar with them, they provide a degree of comfort, and there is certainly a lot to be said for having confidence in your equipment. Of the four trenching and excavation protective systems, shield systems are also the most straightforward and simplistic, presenting less of a learning curve.
With that said, whenever workers become too comfortable with a work method, there is an increased risk of complacency. In the case of working with a shield system, the competent person can become lax about completing assessments – such as those required prior to system use as well as ongoing condition assessments – or may skip them altogether.
The temptation to cut corners is another potential risk of using shield systems. Obviously, this is a possibility associated with all protective systems, but it seems to be particularly rampant with regard to shield systems. Workers might substitute locking pins with nails, wire or bolts; increase the depth of a shield system by placing steel plates against the outside of the shield walls (an unauthorized system modification); or mix components of multiple shield systems.
Sloping and Benching
Last but certainly not least, utility workers have the option of sloping and benching when performing trenching and excavation activities. In my opinion, this is the safest of the four protective systems, primarily because the potential for trench collapse and the collection of hazardous atmosphere in low-lying areas is greatly diminished. Another advantage of sloping and benching is that, due to the sloped terrain, it is possible to introduce or remove workers, materials and equipment from just about any direction. This is a great benefit when an evacuation is necessary.
There are a few fundamental issues associated with sloping and benching. The first is that this method requires a lot of real estate when compared to the use of engineered design, timber shoring and shield systems. Because of this, sloping and benching often is not even considered when work is being done in an urban setting. And, since this method demands a lot of space, it can be more time consuming, plus collected spoils may need to be taken to an alternate site, even if just temporarily. In addition, the OSHA excavations standard does not permit Type C soils to be benched or stepped, and other less cohesive soil types do not bench well. Thus, the value of benching as a means of access is negligible. In these cases, soil must be sloped to the angle of repose. For more information, refer to Table B-1, “Maximum Allowable Slopes,” which can be found in Appendix B to the OSHA excavations standard (see www.osha.gov/pls/oshaweb/owadisp.show_document?p_table=STANDARDS&p_id=10932). Following is a copy of the table for easy reference.
Conclusion
As you probably have noticed, there is no silver bullet when it comes to selecting a protective system to use when trenching and excavating. Each system has its own unique strengths and weaknesses that need to be measured when planning the work to be performed. The key word here is “planning.”
Regardless of the system that is selected, there are some techniques that can be universally applied to make conditions safer and to increase productivity in the trenching and excavation environment. I encourage you to read the final article in this series, scheduled to be published in the August 2016 issue of Incident Prevention, which will highlight several of those techniques. Until then, stay healthy and stay safe.
About the Author: Jarred O’Dell, CSP, CUSP, is the safety director for Syracuse Utilities and an instructor at Rochester Institute of Technology’s OSHA Education Center. O’Dell has gained 12 years of experience in the construction and utility industries since serving in the U.S. Army. He can be reached at jarred.odell@syracuseutilities.com.