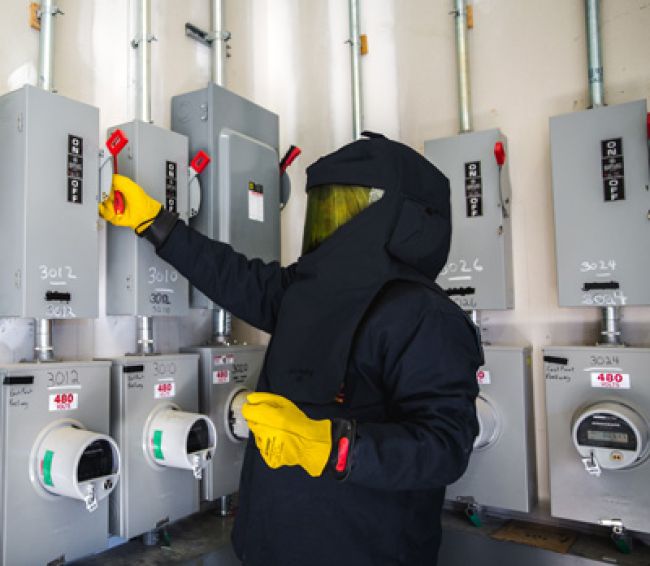
Maximizing Your Arc-Rated Gear
When designing your PPE program, how do you know which option will work best for your application? How can you get the most for your money? How can you get no-cheating compliance from your workers? With so many arc-rated (AR) and flame-resistant (FR) PPE products on the market, it can be difficult for a utility or utility contractor to make a sound decision. To start, complete an analysis to determine hazard levels, as well as the workers who will be exposed. Application, comfort and cost should be considered when deciding on the best product to purchase. In this article, we will help you see how to maximize your AR and FR gear. The process begins with making a choice that makes sense for your company and your application, and then you will need to know how to care for the PPE so you can get the most from your money and extend the equipment’s lifespan.
Application and Comfort
While there have long been arguments and marketing claims about the superiority of either treated or inherent fibers used for FR and AR clothing, the truth is that both can work well from a protection standpoint, and both have a place in the market. Determining which one to use depends on the application and properties the end user needs.
For instance, aramids are durable and can work well with exposure to certain acids and bases – as an example, para-aramid is sensitive to chlorine bleach, mineral acids and UV, but these do not affect its flame resistance – yet pure aramids do not work well with regard to molten metal hazards because molten metal sticks to the fabric. However, there are several aramid blends that work well with molten metal. Modacrylics are great for chemical resistance, but the fiber has a high amount of shrinkage in a thermal exposure and doesn’t pass some of the small-scale tests for flash fire unless blended. Cottons and a similar, regenerated cellulose FR fiber known as FR rayon are breathable, soft and relatively inexpensive, yet they do not perform well in acid exposures. They also have fair colorfastness, meaning that their colors can fade with exposure to light and laundering.
Through the years, ArcWear’s laboratory has completed many projects based on testing requests from end users who wanted to determine if their garments were still considered flame resistant by applicable standards. In those and similar future cases, ArcWear typically will perform the small-scale preliminary test cited in the ASTM F1506 specification and NFPA 2112 standard that is widely known as a “vertical flame test” (ASTM D6413), to determine if a fabric ignites and continues to burn. In our experience with garment failures, the fabric itself has not been the problem; failures we have found in investigations were determined to be caused by either improper laundering or improper application. For example, if the industrial setting contains bleach, FR cottons have had failures, but this is very rare and usually quite apparent. Each fiber has a unique set of characteristics and properties, and these properties should be considered prior to purchase to ensure you can get the most protection out of your PPE, especially now that there are more choices than ever before.
Fabric weight also can affect the wearer’s comfort. The availability of arc flash suits is increasing in the market, with lighter-weight options becoming widely available. Sometimes the cheapest suits feel heavy to the wearer, and the suits can contribute to heat stress when the wearer works in them for long periods of time. Ensuring workers are wearing FR and AR clothing reduces the risk of ignition and burn injury. An American Burn Association study found that there is over a 90 percent chance of survival if a person’s body burns are kept below 25 percent. Our accident investigation data derived from over 165 incidents indicates that less than 3 percent of workers investigated received greater than 25 percent body burn when they wore AR clothing that didn’t ignite and continue to burn. If the user is not comfortable, they may wear the PPE improperly – or they may not wear it at all – and thus picking the right fabric is the most critical issue for a company policy.
What About Other PPE?
Arc Flash Hoods
It is well-known that arc flash hoods can be cumbersome and uncomfortable. They typically are heavy, and the enclosed space of the hood area can make it a challenge for a user to breathe. Additionally, fogging can cause visibility problems. Some updated hood designs address common problems by incorporating hood fans or, more recently, lift-front designs that increase comfort. Fanned hoods have been around for some time, but lift-front designs are new; the lift-front reduces the fabric in the design and enables the wearer to lift open the front. It allows carbon dioxide release and fresh air intake, and one design even has an air pass at the top of the shield, making it more breathable. It should be noted here that fans in hood designs do not filter air to make it breathable – the surrounding air must be 19.5 percent oxygen and free of contaminants or a respiratory system may be necessary. Many workers have put oxygen sensors into hoods, and within a few seconds or minutes those sensors will sound, indicating less than 19.5 percent oxygen is present. This type of test is invalid because we exhale about 13-15 percent oxygen, so the sensors should sound. OSHA requirements for 19.5 percent oxygen do not apply to an arc flash hood, but if the oxygen level stays low, it can affect worker breathing. This should be assessed. Most companies require limits on time spent wearing an arc flash hood, use fans or lift-front hoods, or instruct workers to periodically fan the front flap of the hood to recirculate air. Newer hood designs have basically eliminated this issue, but many older-style hoods remain in use.
Arc Flash Gloves
Per OSHA 29 CFR 1910.269, if you are exposed to an arc flash hazard greater than 14 cal/cm2, your hands must be protected. The ASTM F2675 standard for arc rating gloves was released in 2013, and there are now numerous products available on the market with arc ratings. Gloves come with a variety of designs and material layups, and many boast cut and puncture protection in addition to an arc rating. In our third-party testing experience, these new designs could make leather obsolete in a few years and may make it less common in protector gloves when the new ASTM-proposed AR protector glove standard passes committee. Additionally, the 2018 version of NFPA 2112 is expected to include testing requirements for gloves to be labeled for flash-fire exposures and protection.
Proper Care of FR and AR Garments
Once appropriate PPE has been chosen and the wearer is as comfortable as possible, the PPE should be cared for to improve the longevity of the product. The current guidance on the care and maintenance of garments used in industrial FR and AR applications is:
• ASTM F2757-09, “Standard Guide for Home Laundering Care and Maintenance of Flame, Thermal and Arc Resistant Clothing.”
• ASTM F1449-08(2015), “Standard Guide for Industrial Laundering of Flame, Thermal, and Arc Resistant Clothing.”
• NFPA 2113, “Standard on Selection, Care, Use, and Maintenance of Flame-Resistant Garments for Protection of Industrial Personnel Against Short-Duration Thermal Exposures.”
Both home laundering and industrial laundering can be effective in cleaning PPE and removing contaminants. Industrial laundering should always be used in cases of chemical contaminations if the chemical is on the NIOSH list of chemicals inappropriate to remove from the workplace. This is not true of any utility chemical of which we are aware. Also, if the user can smell hydrocarbons on the clothing, it may require a rewash or special cleaning like industrial or dry cleaning. While home washing is convenient and inexpensive, industrial laundering can be good for garments with contamination too dangerous to take home. Home laundry is typically acceptable, assuming the manufacturer’s care instructions are always followed. A NIOSH study performed in 1997 at the direction of The Workers’ Family Protection Act of 1992 (see www.cdc.gov/niosh/docs/97-125/) found that workers bring contaminants home on both their clothes and their skin; recommendations were made to change out of contaminated clothes at work to be laundered by the employer and, if laundering at home, launder work clothes separately from family loads. NIOSH also provides a pocket guide detailing chemicals that should never be laundered at home. If any of these chemicals are present, an industrial laundry should be consulted for decontamination.
Section 6.2.3 of ASTM F2757 for home laundering of FR and AR garments instructs users not to use chlorine bleach, hydrogen peroxide, starch, fabric softeners, detergents or pretreatment products with chlorine bleach, hydrogen peroxide or derivatives of chlorine bleach or hydrogen peroxide for the laundering of FR clothing. A study was performed by ArcWear in 2016 to determine the effects of bleach in home laundry on a common brand of flame-resistant, arc-rated cotton-nylon fabric. In the study, three loads – a baseline, a load with oxygen bleach and fabric softener, and a load with chlorine bleach and fabric softener – were washed up to 250 times, with a limitation that testing was performed in soft water. The findings were interesting: The sample washed with chlorine bleach passed flammability testing after 50 wash cycles and failed at 100. It was also determined that color loss can be, but is not always, an indicator of flame resistance. Hard water or using more bleach than is commonly recommended by the bleach manufacturer could reduce the number of cycles to remove flame resistance. The FR manufacturer’s recommendations must be followed.
As stated earlier, it’s rare to hear of field issues with flammability on products previously tested for compliance. In our experience, failures on field-use garments have been pinpointed to be caused by either improper laundering (usually by an inexperienced industrial launderer) or contamination (usually mining contaminants). When properly cared for, we have found that many materials from reputable sources truly are flame resistant for the life of the garment.
You can maximize your gear by learning more about your options. Ask manufacturers about your particular hazards. Consider estimated wear life in your analysis and your budget, and keep your workers safe and comfortable.
About the Authors: Hugh Hoagland is an expert on electrical arc testing and electrical safety. He has helped develop many arc-rated products and helps write standards at ASTM, NFPA and IEC/ISO to protect against electric arcs and flash fires. Hoagland works for ArcWear (www.arcwear.com) and e-Hazard (www.e-hazard.com), performing arc testing, consulting and electrical safety training.
Stacy Klausing, M.S., is project manager for ArcWear and heads projects researching textile response in testing. Her master’s thesis was on used firefighters’ turnout gear.