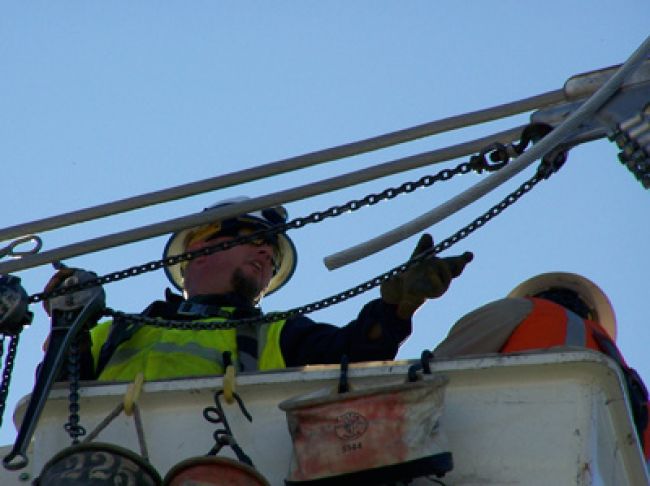
Marking a Safety Milestone at Silicon Valley Power
Clear minds, focused on the task at hand. Strict attention to details and checklists critical to the job. Precise and continual communication among the field, management and control teams. Ongoing training and safety manual review. Looking out for one another. Trust in the workforce’s skills with no micromanagement and with the boss’ door always open.
Such are the written – and unwritten – rules governing the field forces of Silicon Valley Power, the City of Santa Clara, Calif.’s municipal electric utility that recently marked a company milestone: 1,000 days without a lost day of work due to injury or work-related illness.
SVP serves 54,000 customers, including technology industry giants such as Intel, Owens Corning, NVIDIA, Texas Instruments and Applied Materials, and high-profile customers such as the San Francisco 49ers and Levi’s Stadium. Local generation resources include a 147-megawatt combined cycle natural gas plant, landfill methane gas and 20 megawatts of solar installations. Over 692 megawatts of renewable energy are imported from hydro, wind and geothermal partnerships and power purchase agreements; total renewables represent over 40 percent of the company’s power mix.
Health and Safety Success
SVP’s managers firmly believe that the company’s health and safety success begins with a multitude of safety briefings. These include weekly management conferences, mandatory shift start meetings and tailboarding before every job, regardless of scope.
And once the job begins, urgency is effectively tempered by caution. If safety may be jeopardized, there is never any pressure from the city or SVP management to hurry a job or push to restore power during an outage. Safety is first whether it’s in a project planning stage or when responding to an outage. Customer communications during an outage, including social media postings, stress that SVP will restore power as fast as its field force can safely do so.
Strong communication among employees also is key to health and safety success. “SVP found that one-to-one communication between one control operator and one troubleman led to very efficient and very safe troubleshooting practices,” said Mike Keate, senior water and electric system operator. “Like all utilities, everyone is on a radio and following a precise set of steps as the repairs are made. The success of the one-on-one process this past winter is pushing SVP to consider making it policy.
“We have the big picture in the electric control room,” Keate continued. “We have to trust the information our field crews give to us as the eyes in the field, and they have to trust the information we give to them. It’s basically a very strong partnership control operators have with field forces, with trust gained by the absence of safety errors.”
Offering Support and Maintaining Focus
The relationship between SVP field staff and management is equally supportive. Take a recent tailboard meeting before 18 linemen headed into the field for the day. Over an hour was spent discussing the day’s challenges, with managers consciously stepping back while field staff discussed the oddities of the assignments and gave advice to their colleagues about the work ahead.
SVP also is vigilant about what might cause someone to lose focus. For instance, when field crews said their protective rain gear caused them to heat up and sweat, the utility looked at the situation as not just a comfort issue but a safety issue. I then found and ordered PPE that should better maintain comfort and keep workers focused and healthy on the job.
In addition, “If someone’s worked long hours and is tired, we’ll get them a motel room or drive them home,” said Dave Padilla, senior manager of transmission and distribution. “We continually look for anything that might take focus away from a worker, and we encourage them to let us know if something is not right.”
Looking Out for One Another
Team building by freely sharing information and getting workers’ buy-in on most issues is part of the SVP culture. For instance, discussion at a recent T&D safety stand-up meeting included the pros and cons of a new bucket truck. Management listened intently while the crew discussed what piece of equipment would be safest and most efficient. Together, the group came up with a recommendation. “We’ll go with your choice,” Padilla told the group. Afterward he explained, “They have to know the equipment and work with it, so it just makes sense to leave the decision to the field staff.
“Meetings like [this one] are what we do all the time,” Padilla added. “You can see how close they are. They share information to protect their co-workers. Some of them take the lead on the conversations and I just let the group run with it. I don’t believe in micromanaging.”
Tony Ochoa, a 19-year SVP veteran who started as a lineman and is now crew foreman, emphasized the importance of discussing field intel at the meeting. “Thinking of our buddies’ safety when they come across something unusual is normal here. We all know that we don’t want dangerous surprises out there.”
One hazard faced by electricians and lineworkers nationwide is the presence of asbestos and lead in older equipment. SVP field workers are required to take courses in hazardous materials safety so that they can recognize and properly handle materials that can be dangerous to their health.
“Teamwork, being a professional and learning are all really important here,” said lineman Brandon Quijada. “It’s both a team environment and a family environment. The boss wants us to be successful.”
“I respect them, they respect me,” added Padilla. “Lose that respect and you have problems. The opportunity to cooperatively learn from mistakes is a huge part of our work. Our crew won’t hide a mistake, because they know we just want to correct it. We manage with respect, trust and high expectations, not by fear.”
Working with Contractors
Along with watching out for each other, field workers must monitor contractors.
“The other day I saw a contractor about to dig where I knew we had a 12-kV line,” said SVP utility locator Joe Gartner. “He didn’t have a USA called in. If I hadn’t stopped him, we could have had an injury or a fatality.”
Ochoa pointed to one more safety aspect that he said makes SVP special. “Our bosses don’t just see dollar signs when it comes to our safety. If our troubleman sees a situation that may not be 100 percent safe, we’ll de-energize the power to ensure safety even though it might be inconvenient for customers. Everyone wants to restore power quickly for the community, but shortcuts are simply not tolerated.”
That sentiment pervades SVP.
“My primary job here is to have my guys go home to their family every day in the same or better shape than they came in. That’s my philosophy,” said Greg Garcia, electric division manager – substations, as he watched foreman Chris Divens give detailed instructions to a group of contractors. The group was tailboarding before entering a substation switchgear that had failed due to excessive moisture delivered by extremely wet weather conditions.
When the substation assignments were made at that morning’s briefing, each job required a tailboard sheet that explained the job and related safety rules – noted by rule number – that applied. All tailboard sheets are reviewed with the field staff by a senior technician or another technician for a double check. The whole crew signs the sheet. It is sometimes described by managers as a “say it, read it, say it again and sign it” process.
“The tailboards are not the end of the safety process,” Garcia pointed out. “After the job is finished, the total quality compliance review that was signed at the start is filled in, citing completion of every aspect of the job, the PPE and materials related to the work procedures, with each item followed by the relevant rule number. Anything unusual is noted for discussion.
“Every Wednesday we have a safety meeting so that if there are any topics we need to discuss, or if someone wants to bring up a topic from the safety manual or from an event in the field, we talk about it,” Garcia continued. “Also, at any time during the week, any SVP crew member can bring up an issue and it will be addressed.”
He added that they “never miss a meeting. If there’s an outage or other emergency, we just postpone the meeting to the next day. If someone is off or on a job, they get briefed on the topic.”
See Something, Say Something
Crew members always watch out for one another and are instructed to say something if they see something. If anyone feels a situation is not safe, they stop.
“SVP safety policy requires that there is never a situation where someone must follow orders in the field if there is any question about safety,” Garcia said. “We also never have just one person do a job that has any possibility whatsoever of going wrong. When we are racking a breaker out, we have two people in arc flash suits and one guy is changing it out and one guy is some distance away, ready to help if something goes awry. Taking safety a step further, we’ve implemented a remote racking design to make distance our friend.”
Utilizing such modern safety measures is just one piece of SVP’s safety success, complementing management’s commitment to training, teamwork, trust and total buy-in from field forces for their safety practices and philosophy. This recipe has been noted within the industry.
“Silicon Valley Power’s mark of over 1,000 days without a missed workday due to accident or injury is very impressive and speaks well for the training provided by SVP to workers and the workers’ own attention to detail while doing their jobs in Santa Clara,” said Michael Hyland, senior vice president of engineering services for the American Public Power Association. “Santa Clara customers should be proud of this accomplishment by their city-owned electric service provider.”
About the Author: Damon Beck has been the compliance division manager for Silicon Valley Power since 2012. He is responsible for compliance in safety, health and the environment for the power generation sites, transmission and distribution and substation field crews. Beck started at SVP as an intern in 1997 and worked his way up the ranks. He has an academic background in environmental science and energy.