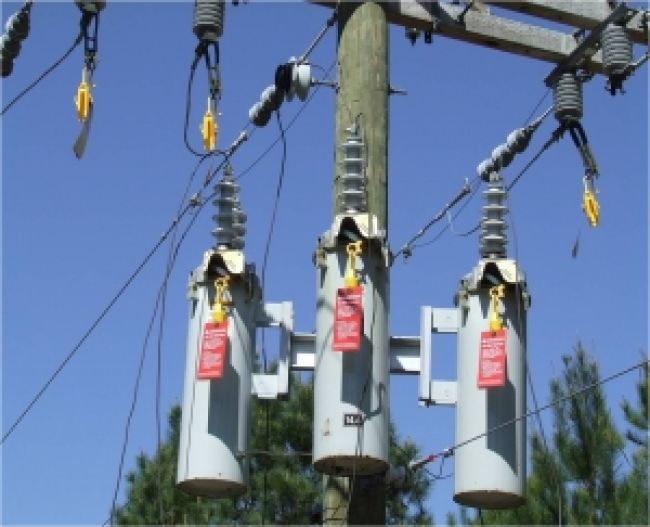
LOTO vs. Switching and Tagging
Electric utilities have unique issues that are not easily addressed in a traditional LOTO program. Traditional programs typically address equipment and system designs that rarely change. This is certainly not true with electric utility Transmission and Distribution (T&D) programs. LOTO procedures are dynamic, changing from day to day and sometimes from hour to hour.
So the question arises: What is the difference between traditional LOTO and switching and tagging programs? Several key differences are equipment source and load conditions that constantly change; various types of switches and disconnectors that may not look like a normal switch, such as an underground elbow; and switches that cannot be locked, such as a hard jumper, etc.
Developing and implementing LOTO procedures for employees working on de-energized lines and equipment can become extremely frustrating when trying to go through the maze of regulatory requirements. OSHA 1910.269, (commonly called the “maintenance standard”) paragraph (d) applies only to generation facilities and paragraph (m) applies only to T&D lines and equipment. Understanding the requirements of these two sections of the OSHA standard along with sections 442 and 444 of NESC-2007 can certainly add value to the design and execution of your LOTO procedures.
Generation LOTO
Traditional LOTO programs can work very well in a generation facility since these systems are typically static compared to T&D systems. Paragraph “d” of the “maintenance standard” addresses this issue and closely follows OSHA’s horizontal lockout/tagout standard found in 1910.147. Typically this means a generation plant will follow the same LOTO procedures developed for non-electric power related work.
OSHA requires a written program consisting of energy control procedures, employee training and periodic inspections along with equipment-specific procedural steps for shutting down, isolating, blocking and securing machines or equipment. Also, an annual review of existing LOTO procedures is a minimum requirement to ensure the procedural steps are correct and are being followed as written.
T&D LOTO
T&D procedures can be more complicated. LOTO is often called “switching and tagging,” which introduces new terminology to a traditional LOTO procedure. Switching and tagging includes requirements for a system operator, requirements for automatic and remote-controlled switches, clearance requirements and protective grounding. Although NESC terminology is somewhat different than OSHA, both standards address specific requirements for securing authorization before switching begins.
According to OSHA, a designated employee, shall contact a system operator to request permission for lines or equipment to be de-energized. NESC refers to a designated person typically as the system operator. Although these terms are inconsistent, they both have the same implication, requiring a qualified person to give direction to a field employee before switching begins and throughout the de-energizing, tagging and grounding procedure. Having a qualified person to review and approve switching who is not performing field work gives important checks and balances and helps maintain better field continuity.
Large utilities typically utilize system operators throughout all switching operations, but smaller utilities sometimes don’t have a good understanding of how to manage the function of a system operator when their system does not have a system control center. A good rule should include requiring an additional qualified employee who is not responsible for field switching to review and approve the switching order prior to the start of any work. A switchman should never write a switching order, review and approve the same order and perform the actual switching. When this occurs, the switching procedure has lost all checks and balances that help prevent critical mistakes from a field employee not understanding changes in system loading and/or source controls.
NESC requires the designated person (system operator) to “keep informed of operating conditions affecting the safe and reliable operation of the system and to maintain a record showing operating changes.” This means utilities should develop an organized process to ensure system changes are maintained and documented for future field use. Employees who make field system changes need to understand the importance of documentation, and system operators need to understand that field employees need the latest information for system reliability. Employee safety is also a very important issue, although field employees should never rely solely on documentation to identify system changes. Field verification must be completed to ensure a safe switching procedure.
T&D Clearance
The meaning of “clearance” can be somewhat confusing when used in a switching and tagging program. OSHA lists two definitions for the word “clearance” and NESC one. Due to the ambiguity of this word, many utility switching and tagging programs have elected to use other terminology. NESC defines “clearance” as the clear distance between two objects measured surface to surface.
The OSHA definition for “clearance,” when used in the context of work, means an “authorization to perform specified work or permission to enter a restricted area.” Clearance is typically used to denote a specific authorization given to an employee in charge to begin field work. A system operator cannot grant a clearance to the person in charge until the switch or disconnector has been operated, the equipment has been rendered inoperable, if possible, and tagged. A clearance cannot be released until the employee in charge notifies all employees of the release, determines all employees are in the clear, ensures all grounds are removed and reports to a system operator completion requirements.
T&D Tagging
Effective use of tags certainly ranks as an important concern for many utilities. NESC states “suitable tags shall be attached to all points where equipment or circuits can be energized.” Many times the question arises, does this mean every point? Many utilities have developed their tagging programs with a unit design philosophy rather than looking at each switch or disconnector. The purpose of a tag is to ensure all points of electrical potential are identified, to give information to field personnel concerning tag placement and to ensure the switch or disconnector cannot be operated until authorization is granted for tag removal. Tags must be used effectively and consistently whether the utility has one crew or thousands of crews.
Conclusion
Many issues, including training challenges, were not discussed in this article but should be addressed vigorously along with other energy sources including but not limited to pneumatic and gas systems. Although electric utilities face many challenges when developing and managing LOTO and switching and tagging programs, a well developed and managed process will result in a safer workplace and better system reliability.
About the Author: Pam Tompkins, a Certified Safety Professional and a Certified Utility Safety Professional, is President of SET Solutions in Lexington, South Carolina. The company specializes in helping small- to medium-size electric utilities comply with safety and training requirements. Prior to forming SET in 2000, Tompkins worked in the electric utility industry for more than 20 years.
video