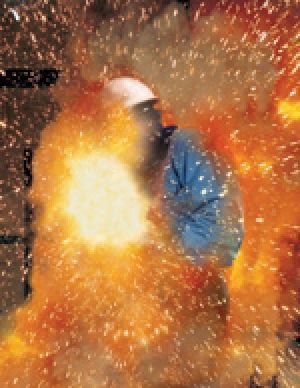
Keys to Evaluating and Comparing Arc-Rated and Flame-Resistant Fabrics
When determining what type of protective clothing to purchase, the first thing specified by a significant number of safety professionals is the flame-resistant (FR) or arc-rated fabric brand. The number, type and source of these fabrics have expanded dramatically in the last few years as new offerings chase profits in an expanding market. There have also recently been significant failures, making it more critical than ever to thoroughly research and select trusted, market-proven brands. These failures can occur on several levels; one recent issue involved the failure of a fabric to be flame resistant when new, while another involved FR failure after laundering. Other failure modes include huge numbers of garments that had to be removed from service within months instead of years due to very high shrinkage, and a dire situation in which the fabric itself was toxic, resulting in the hospitalization of more than 100 lineworkers in Australia.
The fabric choice is the single most important decision for many reasons: There are huge differences in protective performance, FR durability, comfort, shrinkage, cost and value. Major differences exist not just across fiber types – natural, synthetic and blends – but also within fiber types such as FR cotton blends. Evaluation and comparison of FR and arc-rated fabrics are therefore the most critical steps in the implementation of an arc flash protection program.
Utility safety professionals have been asked to do more and more with fewer and fewer resources as companies downsize. This dynamic has made it very tempting for some to rely on local distribution resources – or to simply select the most easily available or least expensive fabric that complies with the standard and arc rating threshold – and move on to other projects. This is frequently a huge mistake with regard to both safety and financials.
Compliance to NESC and/or NFPA 70E is important, but it is only a minimum bar, not a guarantee. Companies should never allow compliance alone to guide their choices. It is important to research a list of properties – especially track record – before making a decision. Following are six big questions you need to ask prior to selecting fabrics to keep your workers safe.
Does the arc rating meet your needs?
Protective performance ratings of FR fabrics, including arc rating, are based entirely on the fabric. We don’t get a rating on a blue coverall or a red shirt; the protective designations are specific to the fabric brand and weight. All single-layer garments made of that particular brand and weight of fabric will then carry that rating, regardless of garment type, manufacturer, color and so on. Protection is, of course, the reason PPE exists, so it is completely understandable that this property is the primary driver when selecting preferred FR and arc-rated fabrics to meet NESC or NFPA categories or hazard analysis data. However, two fabrics with similar arc ratings made of similar fiber blends can – and usually do – perform very differently over time.
How long does flame resistance last in real-world laundering and use conditions?
Protective performance tests are excellent, and the ratings are highly reliable and relevant to the hazards they address, but they do not prove long-term durability of flame resistance. ASTM F1959 uses fabric samples washed three times and dried once. Clothing made in compliance with ASTM F1506 requires FR durability through 25 launderings, so it is frequently specified by buyers. Some people then choose to look outside arc flash standards to NFPA 2112, which is a flash fire standard, because it measures flame resistance after 100 industrial launderings. The NFPA 2112 wash method uses perfect water chemistry, temperatures, detergents, load levels and procedures, so buyers should be cautious when assuming their results will be similar when cleaning in real-world homes or industrial laundering processes. The NFPA 2112 tested sample may bear very little resemblance to what your employee ends up with after 100 washings months or years later.
The standards are minimum compliance bars broadly written and intended to be inclusive, not exclusive. This is why so many safety managers insist on established, market-proven brands. Market proof is not based on de minimis standards, marketing spin or sales claims. Market proof is when the industry votes, over time, with its wallet. In other words, a product is specified, serves its purpose well and, when a replacement is necessary years later, the same product is selected again and again.
Valued characteristics are not limited to protection. Several other more basic garment traits – such as shrinkage, comfort, cost and appearance – are very important as well.
Will shrinkage be a potential problem for wear life and safe use?
A few fabrics are preshrunk prior to cutting and assembly of the garment, but many are not. It is advisable that a buyer work with sample materials prior to committing to a large purchase to compare comfort and to launder and check fit after extended laundering. A bargain fabric is no bargain at all if it has to be removed from service prematurely due to excessive laundry shrinkage. It can also become a safety hazard if it is not worn or is improperly worn because it is too small. Almost everything shrinks in laundering, but some fabrics shrink significantly more than others. More than 7 percent progressive shrinkage begins to impact wearability. Shrinkage control is achieved by compaction of the fabric at the end of the weaving process, and it is both difficult and expensive. For every 100 yards of fabric that enter the machine, only about 90 yards exit. This technology allows us to limit shrinkage experienced by the customer, ensuring a more reliable fit over time.
Is it comfortable enough that your employees will wear it – and wear it properly?
Comfort is an inherently subjective property and thus difficult or impossible to quantify. There are a few definitive knowns: Cotton and cotton-rich blends are perceived as the most comfortable; lab data is nearly meaningless in predicting comfort – the only truly predictive tool is an unbiased wear test; and lightest weight does not mean greatest comfort, particularly when the lighter fabric does not absorb sweat. You will need to decide what overgarments and undergarments will be allowed, and how the combination may affect arc rating. Fabric brand qualities like softness (new and over time), breathability, moisture management and drape have a major impact on the comfort of the wearer.
For many FR technologies, FR durability and softness are at odds – only a few fabric brands achieve both.
Do you understand the full life-cycle costs, not just the initial costs?
FR fabrics vary widely in price. On average, they represent more than half the cost of a finished FR garment. Since the fabric is the largest cost component, it makes sense to carefully consider options and performance characteristics and to specify the brands you trust. Performance isn’t limited to protection; there are significant life-cycle cost implications with other fabric brand properties such as shrinkage, FR durability, fabric durability and comfort. Purchase price is the most obvious first point of comparison, but market-proven performance in use should weigh heavily in the decision as well. A workforce that wears arc-rated clothing daily will often find that fabrics that are more expensive to buy are actually less expensive to own over time. On the other hand, in a task-based program where arc-rated clothing is donned once or twice a week, the life-cycle cost equation may be different.
Will the fabric’s appearance stand the test of time?
Garment appearance over time is not important to everyone, but in many cases FR garments are also considered to be uniforms, and thus a part of a company’s public image. No one wants to remove garments from service early because a red shirt turned pink or blue coveralls faded to gray. Less expensive dyes result in less expensive garments, but at the cost of poor color retention through laundering or UV rays. In addition, stiff fabrics can lead to streaks or “chalking” in darker colors because of abrasion at garment stress points. This negatively impacts appearance and can substantially reduce the garment wear life.
These differences can be quite significant across fabric categories like aramids versus FR cottons, but many people are surprised to learn there are also major differences within a fabric category such as one FR cotton brand versus another.
Conclusion
It’s easy to see why most safety professionals rate the FR fabric brand as the first and most critical decision in program implementation: The fabric is the key component of protective rating, durability of flame resistance, shrinkage, comfort, cost and long-term appearance. They also recognize that there are major protective and life-cycle cost differences from one fabric brand to another, even within functionally similar categories. And since the standards are a minimum bar, they do not obviate the need for research. There is simply no substitute for a thorough understanding of relevant FR and arc-rated fabric performance characteristics and market-proven performance before specifying preferred brands.
About the Author: Scott Margolin is the international technical director at Westex Inc. Prior to joining Westex in 2000, he was a firefighter for six years and spent 10 years at a major international chemical company, where he led its aramid flash fire business for four years. Margolin has extensive experience with the performance of many protective apparel fabrics, and has conducted or observed more than 3,300 flash fires and 1,200+ electric arcs at laboratories in the U.S., Canada and Europe. He is active in a variety of industry organizations, including EEI, the National Safety Council’s Utilities Division, ASTM and NFPA, and frequently addresses trade associations and groups regarding electric arc and flash fire hazards, body burn injuries, protective performance of FR clothing and related topics.