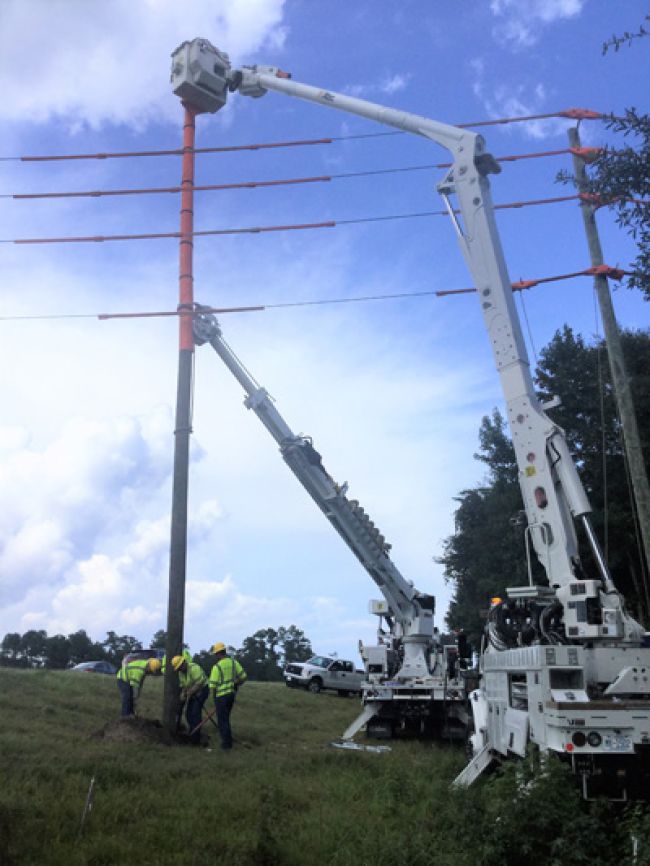
Key Concepts of an Insulate and Isolate Program
Most utilities and contractors that perform work on energized conductors use some form of cover-up program or process. Culture plays a big part in how we currently cover for protection. When a new lineworker joins the crew, that person learns the ways of senior members of the crew, and later that knowledge is passed on to the next new person. Having control of what we work on also has played a significant role in how we cover. If you have control of the energized conductor or equipment you are working on, you may not need as much cover for protection, right? The problem is, in numerous cases, something unexpected has occurred, resulting in a flash or contact event.
There also are other reasons why we continue to have flash and contact events. Today, there is more work to do than there are qualified lineworkers available to perform the work, so sometimes companies advance lineworkers through the ranks faster than they would have in the past so those employees can perform energized work. In addition, we don’t have the luxury of doing as much de-energized work as we once did. Sadly, according to the U.S. Bureau of Labor Statistics, over a period of five years – from 2011 to 2015 – there were 62 fatalities related to electrical contact.
So, what does all of this information point to? Simply put, it is time for us to take what we have learned from the past and train today’s employees on how to insulate (cover) for those times when things could go wrong. Then, if they lose control of what they are working with, no injuries will occur.
That’s easy to say, but changing a company or department’s culture is not an easy thing to do, especially when the company or department employs longtime workers who have found repeated success with the control-and-cover method. Many companies have spent countless hours and dollars to improve their cover-up processes – and many times observations and audits indicate their crews are working just fine – yet events continue to occur. It’s no secret that lineworkers deal with differences of opinion about how cover should be applied.
In order to put in place an effective insulate and isolate (I&I) program, both employers and employees first must understand the concepts of I&I, including why things go wrong, differences of potential, current path, the differences between contact and flash protection, and how to perform an effective hazard analysis. Once those concepts are truly understood, workers can apply them in any energized situation, whether it’s distribution overhead, underground construction, substations, primary or secondary. Then employers can put the decision back in the hands of qualified lineworkers to analyze each job and determine what cover is needed to safely work energized conductors or equipment. In the following paragraphs, we’ll take a closer look at some of these important I&I concepts.
Why Do Things Go Wrong?
No one wakes up in the morning and says, “It’s my turn to have a contact event today.” So, why do things go wrong on job sites? There are a variety of reasons. For instance, do workers have a lack of knowledge or experience? Are they facing time pressure, uncertainty or heavy workloads? Have they formed bad habits over time? Do they feel that doing things safely requires too much time and effort? Do they have a willingness to take risks, i.e., do they feel that nothing is going to happen to them because they are in total control? Once workers understand that something will go wrong on a job site from time to time, that’s when they are ready to truly learn about I&I.
Insulating and Isolating
I believe most industry workers understand that to insulate something in the electrical world, they must use a cover rated for the voltage they are working on to protect themselves from electrocution or flash. The idea is to insulate adequately so that you can’t place yourself between two differences of potential, causing an electrical shock or contact event. To prevent a flash event, you would insulate adequately so that anything being directly worked on – whether it is grounded or energized – would not come in contact with anything else of a different potential.
Isolating is the process of separating a normally energized conductor or piece of equipment from any source of feed so that it cannot become re-energized. It also is possible to isolate a worker from differences of potential associated with what they are working on so that the opposing potentials are not accessible to the worker unless special means for access are used. Body position is everything.
Differences of Potential
Anyone who has ever been shocked by static electricity has experienced a difference of potential. Essentially, if something accepts an electrical charge, it has potential. Most electrical equipment operates based on the concept of two differences of potential working together in a controlled manner as a ground and an energized wire. When differences of potential get together in an uncontrolled manner, there usually is a reaction; for example, when a primary and neutral get together, there will be a violent reaction. If the path of travel is through the body, there will be current flow in the body. From an I&I perspective, when working around energized conductors or equipment, you should always OPT to work on One Potential at a Time and insulate the others so there is no chance of contact. Some examples of differences of potential are energized conductors of different phases; any grounded object versus any energized conductor; energized mechanical jumpers versus any grounded object; and a wooden pole versus an energized conductor.
Current Path
Current will always travel a path of different potential. For instance, let’s say an energized conductor tail gets away from a worker and contacts a grounded object, such as a guy wire, another conductor or even the pole. When this happens, a new current path is created. If you are between the differences of potential, the new current path will be through your body. In the case of the new path being a guy wire or even a wood pole, that new path would put employees on the ground at risk of touch or step potential. Touch potential would be an issue if you were touching the object bringing the current to the ground, as you would become part of the new current path to ground. When current runs to the ground or earth, the point of contact with the ground will produce the highest amount of voltage, but it will dissipate the farther you move away from the point of contact. If you are walking across this grid, one foot will have one level of voltage and the other foot may have a different voltage level, causing the voltage to try to equalize through your body via step potential.
Contact and Flash Protection
When learning what cover is needed for protection, it may be easier to break that protection into two different parts: contact protection and flash protection.
Contact protection covers all differences of potential from what an individual is working on – within reach, extended reach or areas where it is possible he or she might fall – to prevent the individual from contacting two differences of potential at the same time.
In a flash event, two differences of potential could make contact relatively close to a worker, causing heat extreme enough to seriously injure the worker. This normally involves extended reach where conductor tails or jumpers have not been secured, or the different potentials that the tails can reach have not been covered properly. The idea is to secure mechanical jumpers or limit the lengths of conductor tails. Once this is done, any that can still reach a different potential if physical control is lost must be covered in case something goes wrong.
Body Position
Body position is critical when considering contact protection, and you don’t necessarily want to work completely comfortably. What I mean is that you want to work at about eye level; this causes you to have to reach to work, which can be uncomfortable. Don’t overreach your rubber gloves; when you overreach your gloves or work too high, you expose unprotected body parts that may be at risk if something goes wrong. Another important aspect of body position is to make sure you don’t position yourself next to something that has potential that is different from what you are working on, especially if you can move or rotate away from the second potential so you can’t possibly reach it, yet still perform your work. That may eliminate having to cover the second potential.
Hazard Analysis
Finally, performing an effective hazard analysis is the most important part of the job. Identifying the hazards that exist and a plan for mitigation of those hazards are items that need to be discussed and documented during a pre-job briefing. By taking those steps, everyone understands the task at hand and has an opportunity to provide input. Mitigation should be based on the possibility that something – or multiple things – could go wrong, not what you think you can control or handle without error.
Summary
I never said that building an effective I&I program would be easy. By doing so, remember that in a sense, you also may be changing your company’s culture. Your company may employ lineworkers who have worked in the industry for 15 or 20 years or more and never experienced a flash or contact event, and now you have to convince them to buy in to this new way of doing things. The I&I program must be built on strong principles and accountability. There must be commitment from the top down, not the other way around. There must be a strong training program that is built on the mindset of eradicating flashes and contact events. The I&I program must be built so that when a mistake is made, nothing bad happens and everyone goes home safely.
About the Author: Danny Bost, CUSP, provides inspection, safety training, coaching and auditing services for Power Consulting Associates headquartered in Nashville, Tennessee. Prior to his current role, he spent 43 years working for a major utility. Bost can be reached at danny.bost@pca-llc.biz.