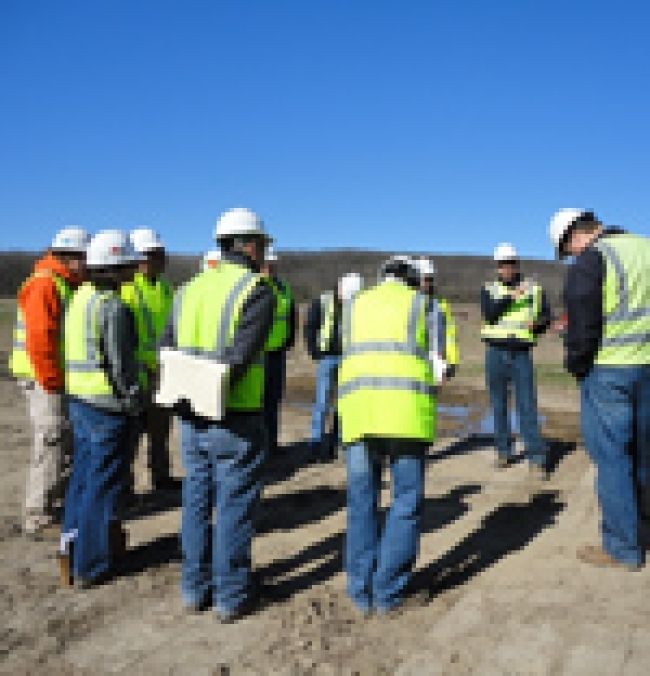
Implementing a Zero Injury Program
You’ve said it and heard it many times before: “Accidents happen.” It’s a phrase that essentially allows us to admit that accidents can’t be prevented. In business, that attitude has the potential to breed complacency when it comes to worker safety. A zero injury philosophy, however, maintains that there always exists some combination of tools, work practices and personal protective equipment that enables workers to carry out their assignments without being injured. Consequently, striving for zero injuries makes sense; it is a practical, achievable goal.
American Transmission Co., a transmission-only utility in the Upper Midwest, recently adopted the zero injury approach using the Construction Industry Institute as a resource. CII performed a study on which work practices, policies and procedures distinguished construction companies with world-class safety records from those with average safety records. They identified nine key topic areas that are distinctive of construction companies committed to zero injuries.
Tailor-Made Safety Program
ATC’s safety program is based on CII’s nine key topic areas with modifications that reflect the company’s business model, which includes system operations, construction and maintenance of the high-voltage transmission system. Like many company safety programs, ATC’s program contains uncompromising statements about a commitment to protect employees from being injured while on the job. The challenge faced by ATC in developing the program was its implementation – how to consistently apply safety principles during planning, execution and day-to-day operations. Even though ATC employees and contractors work in highly hazardous environments, company managers were confident when developing the plan that they could keep the likelihood of a catastrophic injury very low if everyone remained vigilant. They also knew that if complacency set in, an employee, a contractor, or a member of the public could be seriously injured or killed.
Because ATC is a management company that contracts all of its field work, it is imperative that ATC’s standard for contractors only include companies who share their commitment to zero injuries. However, according to CII research, an effective selection process is only the start of promoting safety among contractors; when management firms convey high safety expectations to their contractors, the contractors tend to work more safely. So at ATC, it is now a standard practice that managers ensure new employees and new contractors have high safety expectations.
Safety Program Principles
Incorporating CII’s research, ATC managers developed these 11 safety principles and founded the company’s zero injury safety program on them:
• ATC management, employees and contractors are all active participants in the zero injury process.
• ATC management, employees, and contractors buy in to and are in alignment with the actions needed to achieve zero injuries.
• All employee attitudes and actions are in concert with a zero injury work environment.
• Employee and contractor safety is a line management responsibility.
• ATC safety personnel support the zero injury program.
• Pre-job safety briefs must be performed prior to commencing work on all field projects.
• Department meetings are opened with pertinent safety topics. Safety alerts and messages are communicated to all ATC employees.
• ATC provides specific safety classroom training as appropriate.
• Drug testing is performed pre-hire. Random and for-cause drug and alcohol testing is also utilized.
• Near misses and safety incidents are investigated immediately and corrective actions are taken. ATC communicates investigation results to all employees and contractors.
• Zero injury milestones are established for projects and recognized when they are achieved.
Following is more detailed information about the five ATC safety program principles that have proven over time to be most critical.
1. ATC management, employees and contractors are all active participants in the zero injury process. Upper management is responsible for being the champions of safety, but if the program is to have meaningful impact – if it is to really protect people from getting hurt or sick – then everyone involved in ATC projects must understand ATC’s safety practices and be accountable for implementing them, including executives, supervisors, team leaders, individual contributors and contractors. This requires deliberate and careful communication, and ATC and contractor safety professionals work hard at this. They have a weekly safety update conference call and a bimonthly safety council meeting with construction contractors. This is one of the few meetings for which there is no teleconferencing because safety professionals believe face-to-face communication is necessary to maintain a team spirit. Experience has shown that the toughest challenge is communicating ATC’s safety standards to the consulting companies that occasionally come onto ATC properties. Technicians who inspect equipment and troubleshoot problems often do not receive the same thorough safety training that is provided to construction workers.
2. Employee and contractor safety is a line management responsibility. Placing the responsibility for implementation on line management is a powerful strategy for making zero injuries a reality. If supervisors set the proper example and convey clear expectations to their staff, the zero injury program will succeed. That’s not an oversimplification.
3. Pre-job safety briefs must be performed prior to commencing work on all field projects. Pre-job safety briefs are powerful safety tools for three reasons. One, they establish the credibility of the presenter, usually the first-line supervisor; two, they immediately precede the onset of the work; and three, the topic is specific to the work that is planned for the day. The most effective pre-job safety briefs take place on site and include all workers. When pre-job safety briefs are not given to combined groups, it is especially important to inform those being briefed about the other craftspeople with whom they will be interacting.
4. Near misses and safety incidents are investigated immediately and corrective actions are taken. ATC communicates investigation results to all employees and contractors. When something goes wrong in the field, it is promptly communicated and investigated. All of ATC’s construction contractors are aware of each other’s incidents and corrective actions. In fact, corrective actions are a standard agenda item at the bimonthly safety council meetings. This helps to stop near misses from becoming injuries, and single injuries from becoming trends.
5. Zero injury milestones are established for projects and recognized when they are achieved. There are multiple benefits to setting safety goals and celebrating their accomplishment. However, care must be given to reinforce safe behaviors rather than discourage honest reporting of injuries. OSHA has released statements urging companies to avoid any incentive program that is based on the frequency of injuries because employees may be less inclined to report injuries when they occur. OSHA has a point. It is common for workers to refrain from reporting injuries if they perceive either negative consequences – that they or someone else will be disciplined – or the withdrawal of positive outcomes such as an award not being won. One strategy is to keep celebrations modest, such as throwing a pizza party. Another strategy is to set milestones based on safety initiatives – such as number of audits, completion of safety training or participation in safety meetings – as opposed to injury rates.
New Hire Training
ATC’s managers want new employees to start with pro-safety attitudes and values, so the zero injury program has been incorporated into the onboarding process. Employees learn the zero injury philosophy during their first month of employment. Like many companies, ATC has a mission statement. ATC takes this type of communication a step further and also provides its employees with critical success factors, values and employee behaviors. Safety is the No. 1 critical success factor and also one of the company values. During an employee’s first quarter with ATC, supervisors meet with him or her to review a zero injury job aid, which lists the foundational principles of ATC’s safety program. For each principle, the job aid provides several examples of activities that can be used to implement that element on a day-to-day basis. This new employee/supervisor meeting is intended to impress upon the employee that he or she is a member of an organization that is committed to protecting employees and contractors from on-the-job injuries. Of course, if that good first impression about safety is going to be internalized by the employee, the value of safety has to be repeatedly reinforced on the job. That is why the daily behavior of the new employee’s supervisor and co-workers is critical. Their attitude about safety will be the dominant influence on a new employee’s attitude.
Because ATC does not have its own construction crews, it is not fair to compare ATC’s injury rate to electrical utilities that do have crews. But even when compared to other companies with similar risks, ATC’s accident rate is better than average. The core belief of the zero injury philosophy, however, is that better than average is not acceptable safety performance. ATC is an electric transmission utility, so even a single recordable injury in one year – while outstanding from a recordable incident rate perspective – could have devastating effects for the employee or contractor, in turn affecting the lives of countless others including family, friends and their ATC colleagues.
About the Author: Joseph Saccaro, CSP, CUSA, CUSP, OHST, is employed as a senior safety specialist at American Transmission Co. He has authored numerous safety-related articles and one book, “Developing Safety Training Programs: Preventing Accidents and Improving Worker Performance through Quality Training.” Saccaro’s current responsibilities involve electrical transmission; previously, he worked in nuclear and fossil generation.