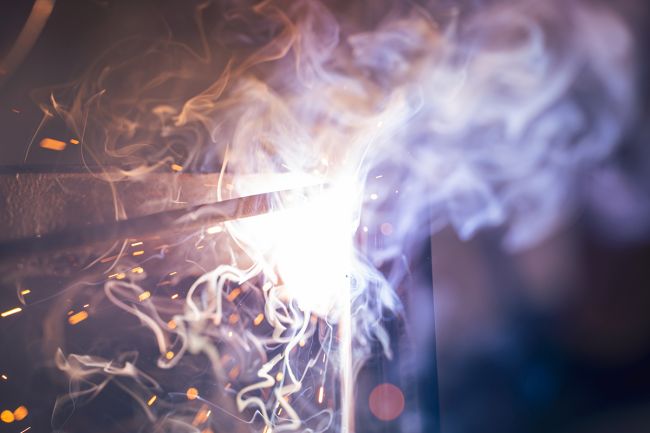
Hand Protection for Electrical Shock and Arc Flash Hazards
Subject matter experts provide updates on the evolution of hand protection for electric utility workers.
Hand protection has evolved in recent times, perhaps making the greatest advancements in the past decade. Although the primary focus of this article is hand protection for electrical shock and arc flash hazards, it also explores the multihazard protection incorporated into newer-generation hand protection, examines safe work practices and glove testing methods, and provides updates on international standards work.
A few decades ago, hand protection consisted of leather gloves (mostly cowhide) used mainly for mechanical protection. Hand protection evolved to address specific hazards, such as extreme heat or cold, vibration, cut resistance, conductivity, electrical (dielectric or voltage rated), and gloves that protect other gloves. Examining federal and consensus standards within the context of day-to-day tasks helps understand the need for multihazard protection.
Electrical Shock Protection
The specification for gloves used for protection against electrical shock is ASTM D120-22, “Standard Specification for Rubber Insulating Gloves.” This specification covers electrical, mechanical and limited chemical tests. The electrical (proof) test is performed on every glove by filling it with water and placing the glove into a water bath so that the water inside and outside of the glove is level. An electrode is placed inside the glove, and the voltage is ramped up until the desired test voltage is reached; the voltage is then maintained for three minutes. The leakage current cannot exceed 5 mA-25 mA, depending on the type of glove tested. The test voltage level is substantially above the maximum-use voltage since the gloves are not in a stressed condition when tested. This assures the ability to protect from shock when in use. Two destructive tests are performed on a sample batch of gloves: the AC moisture absorption test and the AC breakdown test. The breakdown test is performed at a few kilovolts above the proof test, and the moisture absorption test is performed on proof-tested gloves soaked for an additional 16 hours. Gloves may receive a halogenation treatment to reduce surface friction. The rubber insulating glove is electrically strong but mechanically weak against damage such as abrasions, cuts and punctures. The specialized rubber in electrical gloves is leached of the proteins that typically cause allergic reactions since the proteins found in natural rubber allow conductivity at higher voltages.
For care and use, OSHA 29 CFR 1910.137, “Electrical Protective Equipment,” references ASTM F496, “Standard Specification for In-Service Care of Insulating Gloves and Sleeves,” and includes some of the requirements in the regulations, making these mandatory. The standard requires that field care and maintenance include (a) air (inflation) testing before the first use each day combined with a thorough visual examination; (b) storage in the item’s natural shape in a cool, dark, dry place; and (c) performing electrical tests – using the ASTM D120 proof test – on in-service gloves every six months. A very important but often ignored requirement is that a designated person be assigned to inspect gloves to ensure that the user is maintaining the gloves in satisfactory condition. Manufacturer-recommended glove dust liners or cloth-type glove liners are highly effective at moisture and sweat management and do not reduce glove life like baby powder or common talcum powder.
For most instances, OSHA 1910.137(c)(2)(vii) mandates that protector gloves be worn over insulating gloves. The most common protector gloves are cowhide. Leather was prescribed as an overprotector glove up to the NFPA 70E-2021 standard (discussed later in this article). ASTM F696-24, “Standard Specification for Leather Protectors for Rubber Insulating Gloves,” summarizes that the purpose of the leather overprotector is to fit snugly and without undue wrinkles over rubber insulating gloves specified in ASTM D120-22. Protector gloves are not work gloves, and if used as work gloves, they cannot be used as a protector again per ASTM F496. Sharp objects can easily damage the rubber glove, so using a protector glove for mechanical and thermal protection is essential. Interestingly, the ASTM D120 standard does allow for storage of the rubber glove inside a dry protector glove but warns against using wet protector gloves. Wet leather is known to leach products from the tanning process onto the rubber glove, resulting in premature failure. This is one reason that overprotector gloves should not be used in wet locations or on bare hands due to sweat. A more important reason, however, is that wet leather is conductive and reduces grip strength. This was one of the driving factors in the development of ASTM F3258-23, “Standard Specification for Protectors for Rubber Insulating Gloves Meeting Specific Performance Requirements”: to allow materials other than leather to increase dexterity, grip and wear, and to quantify arc flash protection.
Power utilities and commercial electricians use rubber insulating gloves. Power utilities may need to use live-line tools for working on live or energized voltages above 36 kV. They will rely exclusively on being insulated through the tool and an insulating aerial lifting device (e.g., a bucket truck) and will not – for the most part – use a rated rubber insulating glove for those voltages. Electrically rated gloves, as shown in Table 1, have a maximum AC use voltage of 36 kV (AC). Specialized live-line barehand work is regulated by the National Electrical Safety Code, and OSHA 1910.269(q)(3) permits barehand work. However, these workers may need cut protection or arc flash protection so that the appropriate standards can still be used.
Table 1: Glove Voltage from ASTM D120-22
Class of Glove |
Maximum AC Use |
Maximum DC Use |
00 |
500 |
750 |
0 |
1,000 |
1,500 |
1 |
7,500 |
11,250 |
2 |
17,000 |
25,500 |
3 |
26,500 |
39,750 |
4 |
36,000 |
54,000 |
Cut-Resistance and Clean Rooms Requirements
Electrical workers in pharmaceuticals, semiconductor manufacturing, aerospace and food plants utilize various work methods to avoid using leather protectors because of clean rooms requirements or food/chemical restrictions. OSHA 1910.137(c)(2)(vii) doesn’t allow the removal of the leather protector gloves for clean rooms conditions as it only focuses on finger dexterity for fine and small parts. This made it difficult for electrical workers to perform permitted energized tasks, such as energized troubleshooting or voltage verification for control of hazardous energy (lockout/tagout). ASTM F3258-23 was first introduced in 2021 to address this gap. The standard allowed for testing and classification of protector gloves meeting the physical requirement of leather but allowing more classification using ANSI 105 hand protection selection criteria for cut, puncture and abrasion (optional) resistance. Testing certain types of leather with certain thicknesses showed relatively poor cut resistance, although the abrasion and puncture resistance of leather was reasonably good for most types of electrical work. Seamless coatings on the palm side of the gloves promoted grip even in oily conditions and allow more chemical resistance in many work settings.
Manufacturers have created multi-material gloves with cut-resistant layers, coatings and other features like impact resistance to improve gloves – and now specifically protector gloves – for electrical work. Knit gloves with a palm-side coating stretch over the user’s hands and provide a snug fit to promote excellent finger dexterity, grip and clean rooms usage. These benefits are countered by the fact that the snug fit may wrinkle the rubber glove, therefore being noncompliant with the ASTM F3258 and F696 requirement that protector gloves shall not wrinkle the rubber glove. However, other designs are becoming more available for protector gloves, and the new standard allows for even more innovation. During electrical work, especially energized/live troubleshooting and voltage measuring, users may need to don and doff the rubber gloves multiple times. If the rubber gloves are chosen to fit snugly to prevent the overprotectors from causing wrinkles, and there is sweat or moisture added to the mix, donning and doffing the gloves becomes challenging. This is the key reason that rubber gloves are selected to fit marginally loosely. Since the ASTM F3258 standard is new, manufacturers are still working toward innovative solutions to address these challenges. Unfortunately, as of press time, the most widely available ASTM F3258 gloves are for use on Class 1 rubber insulating gloves and higher.
Arc Flash Protection
Working on energized electrical circuits is required during troubleshooting, switching, controlling hazardous energy, emergency repairs or when design limitations prevent de-energization. When working live, the electrical worker may be exposed to (a) a shock hazard with no arc flash hazard, (b) an arc flash hazard with no shock hazard, or (c) both a shock hazard and an arc flash hazard. Traditionally, rubber insulating gloves with leather overprotectors worked well for arc flash protection. Over time, nylon straps and polyester cuffs were introduced with no arc test requirements. In higher incident energy cases (>8 cal/cm² or >Cat 2), these have melted and caused injury. The latest edition of ASTM F696 (2024) now requires polymeric materials in the cuff to withstand a minimum of 20 cal/cm² or be an arc-rated material or the leather used in the glove. Arc rating of the protector is optional for leather, but many manufacturers now offer arc-rated leather protectors. Protector gloves that test above 14 cal/cm² are optimal for utility workers requiring shock protection per OSHA 1910.269(l)(8)(v)(A), which states, “Arc-rated protection is not necessary for the employee’s hands … if the estimated incident energy is no more than 14 cal/cm².”
ASTM F2675, “Standard Test Method for Determining Arc Ratings of Hand Protective Products Developed and Used for Electrical Arc Flash Protection,” was first published in 2013. This test method allows for testing of all gloves, including rubber insulating gloves, leather overprotectors, knit cut-resistant gloves and multi-fabric gloves. It requires ignition testing for gloves that are not proven to be flame resistant. Both ASTM F696-24 for leather protectors and ASTM F3258-23 (leather, fabric or composite gloves) recognize arc ratings using ASTM F2675. ASTM F3258-23 protectors must achieve a minimum arc rating of 4 cal/cm² to prevent ignition of rubber insulating gloves. The ASTM F3258 standard and the fact that OSHA uses the term “protectors” (without using “leather”) are key reasons for dropping the word “leather” from “protector gloves” in the NFPA 70E-2024 edition.
International Standards
IEC 60903:2014, “Live working – Electrical insulating gloves,” referenced in NFPA 70E-2024, is not referenced in OSHA. It differs from the ASTM D120-22 standard in several aspects. There is no thickness requirement on electrical gloves, meaning that gloves meeting only the IEC standard may not be as durable as those meeting ASTM D120-22. However, they also include composite gloves, which are coated over a lining or other technology that enhances the mechanical properties (puncture and cut resistance) and are intended to be worn without protector gloves. These are common in Europe as they do not currently have a protector glove standard like ASTM F696-24 or ASTM F3258-23. From a U.S. perspective, this standard is important to watch as ASTM D120-22 is currently balloting adding composite electrically insulating gloves to the standard. In arc testing, they are much higher in protection, but the downside is that they are stiffer in use. Time will tell whether they are approved for use in the U.S. by OSHA and, if accepted, become common in live-line work.
An IEC project team has also been working on IEC 63232 (in process), which contains arc testing methods and an arc-rated glove and protector glove standard for international use. This new standard will be like the standards already in use in the U.S.
Concluding Remarks
When exposed to arc flash hazards without exposure to electrical shock hazards, any arc-rated glove with a proper arc rating is adequate. Arc-rated, cut-resistant gloves are ideal for switching and racking operations when no shock hazards are present.
If shock hazards are present, arc-rated protector gloves (leather or non-leather/ASTM F3258 or ASTM F696) are used with rubber insulating gloves up to 36 kV AC. OSHA requires arc ratings on gloves when the arc flash prediction is greater than 14 cal/cm2. Rubber insulating gloves with protectors meeting the latest specifications (ASTM F696-24 or ASTM F3258-23) ensure that melting cuffs are removed from the field.
Presently, there appears to be no ideal option for low-voltage installations (<600 volts) in clean rooms that present both shock and arc flash hazards (usually <12 cal/cm²). But with the rapid advancement of glove developments, a solution may not be that far off.
About the Authors: Zarheer Jooma, P.E., is a partner at e-Hazard (https://e-hazard.com). He has convened and chaired arc flash safety standards and is a member of both ASTM F18 and IEC TC 78. Jooma performs electrical network design, arc flash studies, electrical safety training, incident investigations and auditing. He is the technical paper review chair for two IEEE journals and chair for the IEEE Electrical Safety Workshop 2025.
Hugh Hoagland is retired from ArcWear (www.arcwear.com) and e-Hazard. An expert on arc flash and electrical safety, he continues to write standards for ASTM and IEC/ISO and also provides consulting services.
- Make It Safe To …
- October-November 2024 Q&A
- The Meter Base Checkout Procedure
- Trailers, Brakes and Common Usage Errors
- Reduce Risk with New Strategies for Operator Training
- Empowering Utility Workers: Integrating Job Control and Resource Availability for Enhanced Safety
- Designing Safe and Inclusive Work Systems for a Neurodiverse Workplace
- Hand Protection for Electrical Shock and Arc Flash Hazards