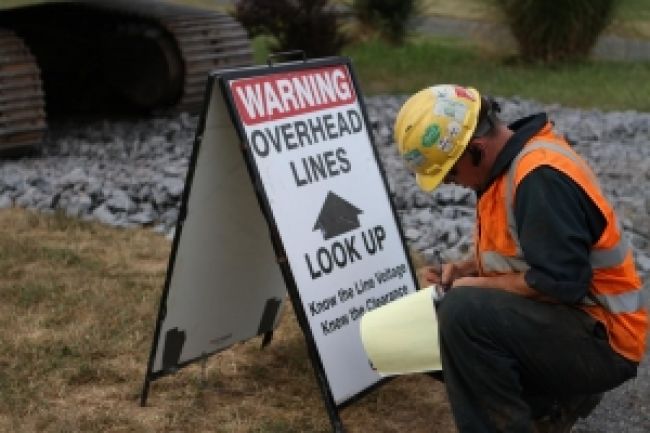
Foundation Drilling Safety: The Aldridge Electric Story of Success
According to the Bureau of Labor Statistics, between 4,500 and 5,000 people are killed in the U.S. workforce each year. Approximately 20 percent of those workplace fatalities are in the construction industry. According to OSHA, the four leading hazards that contribute to fatal injuries in construction are falls, electrocution, struck by object and caught-in/between.
In construction, especially in drilled shaft foundations, these four hazards are present each and every day. It could be argued that drilled shaft foundations are potentially one of the most hazardous types of construction work performed. Therefore, for any company to succeed in this type of work, two things must exist: The company must be committed to safety and have a comprehensive and progressive safety and health program.
Aldridge Electric is continually recognized as a leader in the field of drilled shaft foundation safety. The company attributes its safety success to a thorough pre-task hazard analysis program, site ownership, a comprehensive fall protection plan, enforcement of its safety and health program, and employee training.
The DTA – An Important Tool
Before any task can begin, a thorough pre-task hazard analysis must be performed. It is the policy of Aldridge Electric that the pre-task analysis be documented and reviewed with all crew members involved in the task. The pre-task hazard analysis documentation and review are accomplished through the use of a daily task analysis (DTA). The DTA is important for a number of reasons. It documents and verifies that all crew members have been made aware of the task to be performed and the hazards associated with that task. Further, if additional employees are to enter the work site where the task is taking place, they also will be apprised of the information on the DTA and must sign it before entering. Moreover, if any non-Aldridge Electric personnel wish to enter the work site, they are required to be apprised of the information on the DTA and must sign it before being allowed to enter. DTA review and signature prior to entering a work site are vital for site control, or more importantly, site ownership.
Site ownership is an important aspect of the Aldridge Electric safety and health program. Just as the DTA is important for federal liability, site ownership is important for legal liability. The DTA helps to ensure that any non-Aldridge Electric personnel shall not enter a company work site without full knowledge of the task at hand and all hazards associated with the task. Any non-Aldridge Electric personnel who has not received a full review of the DTA and has not signed off on it will not be allowed to enter the work area.
However, the biggest reason for site control or site ownership is the drilled shaft itself. The depth of a drilled shaft can range from 6 feet to 160 feet or more. Therefore, fall protection is critical to drilled shaft foundation work. Across the industry, there are many methods used to protect workers from fall hazards associated with drilled shaft foundations. Aldridge Electric relies on three methods of fall protection for drilled shafts. For drilled shafts where work is not taking place, the drilled shaft is completely covered with steel plates or large wooden mats. For drilled shafts where work is taking place, the preferred method of fall protection is to set steel casing at approximately 42 inches above grade. Where steel casing cannot be utilized for fall protection, a personal fall arrest system (PFAS) is used. The PFAS consists of a full body harness with a self-retracting lanyard affixed to an engineered concrete anchor block. At Aldridge Electric, incorporation of a PFAS for fall protection also requires the use of a physical perimeter erected at least 6 feet from the drilled shaft opening. The physical perimeter consists of yellow stanchions, yellow chain and warning signs indicating the existence of an open hole. Access into the perimeter is controlled and is identified with an “Enter Here” sign. Where the physical perimeter cannot be erected, a dedicated watchman is utilized to prevent unprotected access to the drilled shaft. Failure to incorporate the physical perimeter when using a PFAS, or entry into the perimeter area without a PFAS, will result in immediate disciplinary action against an Aldridge Electric employee. In addition, entry into the perimeter by non-Aldridge Electric personnel will result in that person being removed from the work site.
Enforcement of the safety and health program is critical to its success. As stated earlier, unauthorized entry into the perimeter area will result in immediate disciplinary action. At Aldridge Electric, not only will the employee who violated the perimeter be disciplined, but any co-worker who allows an employee to enter the perimeter without use of a PFAS also will be disciplined. This disciplinary action is part of the company’s zero tolerance policy and is the cornerstone of its safety and health program.
Three-Step Training Plan
Even the best safety and health program cannot be successful unless the workers for whom it was written, and is intended to protect, are trained in its elements. At Aldridge Electric, this is achieved in three ways. First, every new employee receives new-hire orientation prior to his or her initial job assignment. The purpose of the new-hire orientation is to introduce new employees to the organization’s safety and health program. The orientation, conducted on the first day of employment, not only provides the employee with a thorough explanation of the program, but also prepares the employee to recognize and stay safe from job site hazards associated with the work he or she is to perform. In addition, new-hire orientation is designed to strongly emphasize emergency response, incident reporting and the importance of the DTA. It also includes an explanation of the Aldridge Electric Green Hard Hat Program, which was developed to teach company safety policies and expectations in light of the organization’s rapidly growing number of new employees.
Upon completion of the new-hire orientation, the employee is issued a green hard hat and is then enrolled in the Green Hard Hat Program. Enrollment in the program is mandatory for any employee who has never worked for Aldridge Electric or has not worked for the company in the past two years. Wearing the green hard hat designates that the employee is in training. Enrollment ensures that the employee receives the necessary training and develops the appropriate skills to be a safe and productive worker in drilled shaft foundation work.
The Green Hard Hat Program consists of approximately eight weeks of on-the-job training with three superintendent and three safety representative evaluations. In each of the evaluations, the employee is assessed in both the knowledge of the company safety and health program (conducted by the safety representative) and safe work practices (conducted by the employee’s superintendent). Any deficiencies identified in an evaluation are immediately reviewed with the employee, and the employee is coached, corrected or trained to eliminate the deficiency. All evaluations are documented and can be completed electronically using an online application. Approximately eight weeks after the employee’s start date, he or she completes the final safety representative evaluation, which is an exam conducted by the safety representative. The exam is graded and used to assess the employee’s knowledge of safe work practices and company policy. Upon successful completion of the superintendent and safety representative evaluations, the employee graduates from the Green Hard Hat Program. Following graduation, the employee is issued a yellow hard hat and becomes eligible for the third element of the training process – formal training conducted by an Aldridge Electric safety trainer. This consists of first aid/CPR training, qualified signalman training, qualified rigger training, fall protection training, confined space training, flagger training and OSHA 10-hour training if the employee has not already received it.
About the Author: Gary Coleman, CHST, OHST, is a safety manager for Aldridge Electric. He has 30 years of construction experience with 12 years in construction safety, and holds a Master of Science degree from Northern Illinois University.
About Aldridge Electric: Aldridge Electric is recognized as one of the largest infrastructure contractors in the nation. With more than 60 years of experience and an outstanding safety record, the company serves customers in a variety of industries including rail transit, airport, highway, industrial, power generation, substations, transmission and distribution, drilled shaft foundations, access and clearing, ports and intermodal yards.