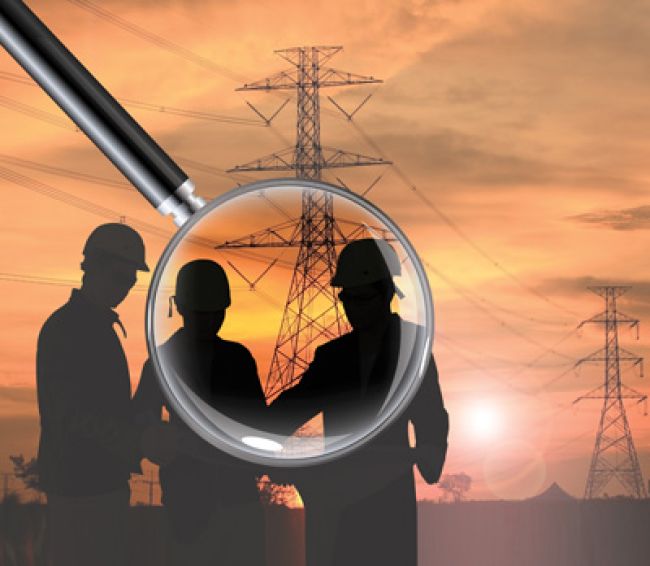
Establishing and Evaluating a Value-Driven Safety Culture
“Safety” is a word many of use daily in our line of work. Within our organizations, we have safety manuals, safety procedures, safety meetings and even entire safety departments. But I often wonder how many times workers have truly considered the question, “What does safety mean to me?”
Safety is “the condition of being safe from undergoing or causing hurt, injury or loss,” as defined by Merriam-Webster. If you were to come up with your own definition of safety, what would it be? Some common responses I’ve heard include having the ability to go home at the end of each day, not getting injured and following all of the rules.
Whatever their definition of safety happens to be, most people don’t head to work each day planning to get hurt – but it does happen. And the reasons why often reflect the safety culture of the workplace. Relatedly, how an organization’s leadership team defines safety has an enormous impact on the company safety culture.
Compliance vs. Value
Generally speaking, there are two perspectives on workplace safety: those who favor compliance-driven safety and those who favor value-driven safety. One of these perspectives will help to create and cultivate a healthy safety culture. The other will help to destroy it.
Compliance-driven safety focuses solely on worker adherence to rules and standards. For instance, let’s say OSHA comes out with a new rule; a compliance-driven organization will implement a new policy or process to comply with that rule. That sounds like a good idea, right? After all, we are taught to always follow the rules.
However, the problem here is that the organization has put its focus on the new rule itself – not the reason why the rule was created. Workers probably will still comply with the rule because it’s mandatory to do so, but without an explanation of why it is needed, they may see little to no value in the rule beyond the fact that they have to obey it.
Value-driven safety, on the other hand, is an approach in which an organization takes a hard look at why safety rules were created: because hazards exist. Workers are much more likely to follow rules and find value in them when they understand the underlying reasons behind the rules’ creation.
What Does a Safe Workplace Look Like?
So, what does a safe workplace really look like? We know that following all of the rules is part of creating and maintaining a safe environment, and we know that workers need to understand the reasoning behind safety rules, but we can follow every single rule every single time and still get hurt. There must be more to it, right?
Simply put, safety is about identifying hazards, assessing risks, and effectively controlling those hazards and risks. That may not sound terribly complicated; however, there are some major issues that can make these tasks difficult to execute. Perhaps the biggest challenge we face to properly implementing safety is ourselves, the human beings who comprise the workforce. Often, our perception of workplace hazards and risks is inaccurate, so the controls that we implement may not be effective. This is especially true when we are familiar with a task to be performed and have completed it many times before. Over time, we become comfortable with the associated hazards and risks, and thus our perception of them drifts.
Why does this happen? In large part, it’s typically because leadership hasn’t effectively communicated and demonstrated that safety is a value within the organization. Safety may be considered a priority, but other items – such as production, performance and quality – also are likely to be priorities. And an organization’s list of priorities can change based on circumstances or environment. Values, however, are fundamentally different. Everyone has a set of values that they live by, and those values are used when making nearly every decision. Whether or not workers perceive safety as a value often is a direct reflection of whether safety is a core value to leadership.
How Do We Evaluate Safety?
If you want to cultivate and grow your company’s safety culture, it’s important to evaluate where you are today. Traditionally, lagging indicators (e.g., incident frequency rates, experience modification rates and DART rates) have been used to measure and evaluate safety within organizations. These indicators can still be very useful; however, they are based on events that happened in the past.
A more accurate way to evaluate safety is to utilize leading indicators. Worker observations, near-miss reporting, training and worker feedback will offer insight into what organizational safety looks like in the present.
Worker Observations
Worker observations can be a proactive way for management to evaluate and measure safety. However, some workers have a negative reaction when they hear words like “observation” and “audit,” and there is a justifiable reason for it. The intent behind an observation should be to evaluate why and how work is being performed and to identify potential areas for improvement. For some workers, though, their experience with observations has consisted of someone trying to catch them doing something wrong. That is a clear indicator of an organization’s safety culture. If workers believe they’re being observed primarily so they can be caught and punished for their errors, it is critical that leadership work to identify why that’s the case and then act to correct the issue.
Near-Miss Reporting
Organizations that have strong safety cultures typically have systems in place to report near misses. It’s also true that some organizations with near-miss reporting systems have poor safety cultures. Simply having a system in place doesn’t ensure success; it’s how the system is implemented, used and managed that will ultimately reveal whether workers see value in it or not. For it to be successful, workers need to be educated on the definition of a near miss as well as the importance of sharing information when one occurs. After workers begin reporting near misses, leadership has the responsibility to do something with that information. Regular communications from leadership to the workforce about near-miss occurrences and associated action plans are critical to success.
Training
It’s no secret that training is an essential component of a successful safety program and culture. But it’s important to keep in mind that there is a significant difference between training and effective training. From a regulatory perspective, there are many times when safety training is required – and, unfortunately, that is the only driver for some training programs. When evaluating any required worker training, consider whether training is focused on education about safe work practices or if the training will merely check a box because OSHA mandated it.
Worker Feedback
Simply asking workers for feedback on their organization’s safety processes can identify areas of success as well as those in which improvement may be needed. Implementing safety-related solutions that workers bring to leadership provides opportunities for workers to take ownership of their personal safety and the organization’s safety processes. However, if no one within an organization is asking for feedback or providing it, that likely is a clear indicator of an unhealthy safety culture.
Re-Evaluate Regularly
Lastly, it’s critical for an organization to re-evaluate their safety processes on a continuous basis. Sometimes leadership will engage in all of the positive actions mentioned above, but doing so doesn’t always produce the desired results. If an organization isn’t getting the results it wants and needs, it’s time to re-evaluate to identify new methods to achieve the intended results. Be sure to always determine what the intended results are before implementing something new. Engage in benchmarking by studying how other organizations within the industry drive a successful safety culture. Another option is to bring in an outside party to provide an objective evaluation of the organization’s safety processes. Whatever method is used, it is important to keep in mind that any organization with a successful safety culture also has an environment in which safety processes can be proactively measured, evaluated and improved.
About the Author: Matt Edmonds, CUSP, CHST, CET, is vice president of SET Solutions (https://setsolutionsllc.com) and has over 15 years of safety management experience. He has helped electric power organizations throughout the U.S. develop and implement successful safety strategies. Edmonds also is an OSHA-authorized instructor who has delivered presentations at Incident Prevention and ASSP conferences.