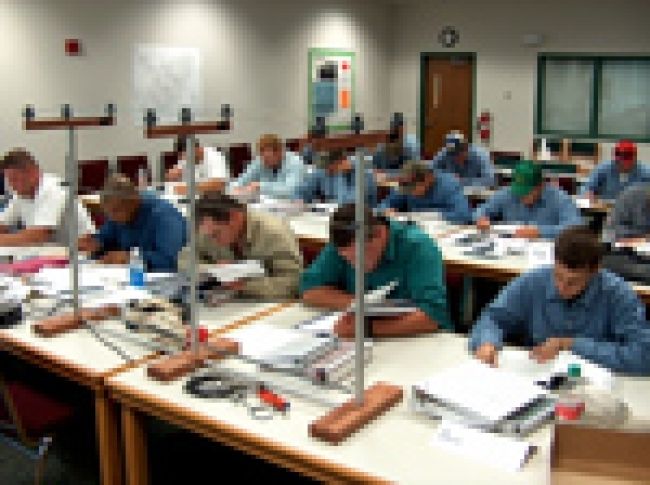
Employee Training: How Hard Can It Be?
We all know high-quality training must take place to ensure the overall development of employees. Does having a well-trained employee mean the employee only attends a monthly safety meeting to gain training knowledge? Certainly not. Training should provide employees with a continual understanding of job task requirements, task-associated hazards and the appropriate abatement strategies for their safety. A monthly safety meeting may help validate these issues, but it cannot be the sole delivery method for training. Unfortunately, many employees receive no additional training beyond apprenticeship other than safety meetings. Some employees, depending on their job classification, may never receive any additional formal training besides safety meetings.
Knowing that training is important and required may not always ensure it takes place due to time constraints and a lack of funds and resources. Many utilities and utility contractors hire employees, then leave training to time on the job and knowledge learned from existing employees who may use improper or unsafe work techniques. When no specific plan is developed for training, employees may never reach their full potential.
Developing a Plan
Developing a well-planned training process is not easy. Each training plan should address the desired length of training, the number of training steps with compensation ranges, and the requirements for employee completion and advancement. Ask the question: What knowledge is required to ensure full competency at the end of training? Academics, skills training, on-the-job training and demonstrated proficiency should all be addressed in the training plan. Plans must have full management and employee support to ensure success.
In many cases, a developed plan will change the structure of a job classification. This is especially true for jobs that only have one designation and salary range. Ensuring appropriate compensation for job knowledge and experience is a very important part of plan development.
Employees who work as customer service representatives, line designers and system operators or dispatchers need a developed plan no less than an employee who works on energized lines and equipment. Although these employees do not necessarily perform work on or near live energized parts, their jobs directly impact other employees as well as the public. Customer service representatives need to understand electric system fundamentals to determine customer requirements; the line designer needs to understand how to design a system that is functional and safe for construction and maintenance; and a system operator needs to understand how to operate the system to ensure safety and reliability.
Qualification Requirements
“Qualified” employees have specific training requirements defined by OSHA and the National Electric Safety Code (NESC). According to OSHA, a qualified employee is someone who is “knowledgeable in the construction and operation of electric power generation, transmission, or distribution equipment involved, along with the associated hazards.”
Training for qualified employees must establish employee proficiency in OSHA safety standards and utility-specific work practices. This means employees must demonstrate proficiency and safety in performing all required tasks. OSHA and NESC list major requirements for qualified employees in the standards which are fairly straightforward and easy to understand. More difficult is the requirement to identify all associated hazards with each job function and to ensure qualification for the specific work performed. For example, a major storm hits and a URD journeyman is assigned to an overhead crew. Although the journeyman has demonstrated proficiency for safely completing URD tasks, the tasks were not specific for the type of work required in overhead operations. To ensure proficiency and appropriate qualification, the journeyman must demonstrate the ability to safely work on overhead equipment and lines.
Employers must certify that employees are qualified and the certification must be maintained for the duration of employment. Additionally, if a task is performed less than once per year, OSHA mandates retraining before the work can be performed. OSHA further requires the employer to determine – through regular supervision and inspections conducted on at least an annual basis – that each employee is complying with all safety-related work practices.
Training Organizations
Many utilities use external training organizations for various jobs. Although external training organizations offer great educational opportunities, they should not be used as the certifying authority. OSHA is very clear that qualification does not specifically correlate to school completion. The employer is responsible for certifying that employees are trained and qualified to work on the specific lines and equipment owned by the utility.
Years ago I worked for an electric utility that participated in a state-sponsored lineworker school. Employees attended four weeklong courses that were offered over several years to achieve journeyman status. Several major issues became extremely evident. First, some employees finished training early depending on when the employee was hired and the scheduling of classes. Second, training was structured for a wide variety of duties and was not always specific enough since multiple utilities utilized the training. Third, people who had been on the job for years were complaining that employees were moving to journeyman status too fast to learn the proper skills and did not always feel an employee was qualified to perform the work, especially in outage restoration situations. This type of training had no organized method of promotion to journeyman other than school completion and time in grade. We learned that employees who completed the schools had vast differences in knowledge and skill level although they ended up in the same job classification.
Management addressed these issues by developing an organized training plan that addressed academics, external training and on-the-job training requirements. Written and practical reviews were attached to the training process. A training team was developed to ensure identification of hazards and proven proficiency of employees before various levels of qualification were achieved. This program made a profound difference at the utility because all employees understood the requirements for each level of qualification, supervisors had qualified workers, employees were being paid for the job they were doing and so on.
A well-developed training plan is extremely important for every job classification. Without a plan, training becomes fragmented and many times left to chance. Keep in mind the plan should ensure employees have a well-orchestrated method of development and an understanding of all specific requirements. Finally, the time taken to ensure training is developed and completed appropriately will equate to a well-trained, safe employee.
About the Author: Pam Tompkins is president of SET Solutions in Lexington, S.C. The company specializes in helping small- to medium-size electric utilities comply with safety and training requirements. Prior to forming SET Solutions in 2000, Tompkins worked in the electric utility industry for more than 20 years.