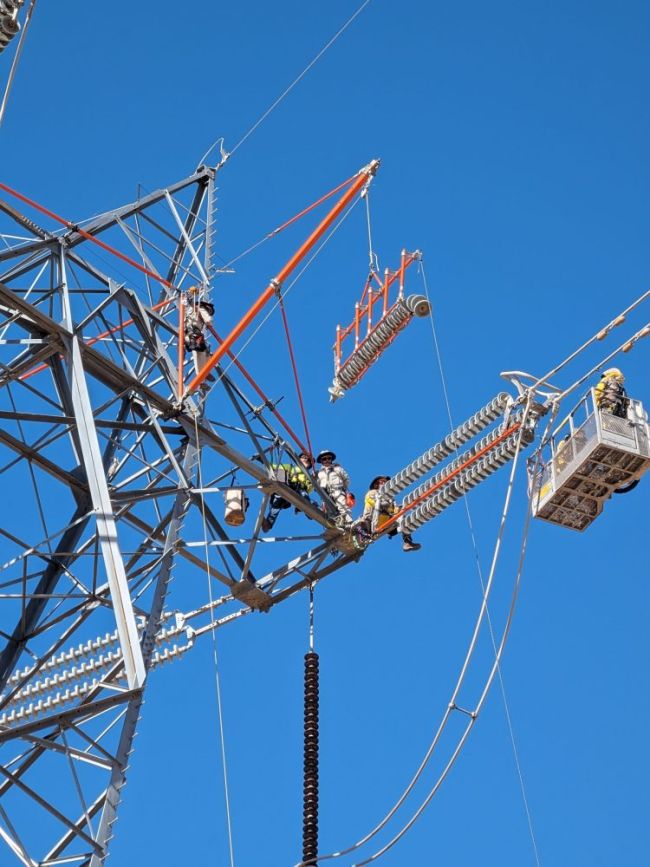
Beyond the ABCs: Fall Protection for Unique Tasks
Effective worker protection demands precise equipment selection, thorough worker training and well-rehearsed rescue procedures.
The electric transmission and distribution (T&D) industry often requires work in challenging environments. Whether crew members access tall structures by helicopter, use rope-access methods to climb lattice towers, or ride wire carts to install and maintain spacers along energized lines, their approach goes beyond standard ground-based operations. These specialized techniques can speed up projects, minimize ground disturbance – especially on protected and sensitive land – and reduce the need for site preparation (e.g., building roads).
Yet all of them present complex fall hazards.
Many readers may be familiar with the so-called “ABCs” of fall protection (anchors, body supports and connectors), but the tasks described above call for more advanced planning, training and equipment. The remainder of this article explores strategies to protect employees at height during such operations, with a focus on training, rescue planning, the competent person’s role, and equipment selection and inspection.
Understanding the Hazards
Using helicopters, rope-access methods and wire carts can be highly beneficial for T&D work. Helicopters allow crews to do their work without the need to build roads or clear land in sensitive areas, such as wetlands and wildlife habitats. Where it’s impractical to use traditional climbing methods or aerial equipment, rope access is often employed to perform energized tasks and move around transmission structures. Wire carts enable technicians to traverse energized conductors without making repeated ground ascents and descents, reducing outage times and worker fatigue.
Although these techniques can improve efficiency and shorten overall project timelines, they are not without their own specific hazards, described below.
Helicopter operations: When a lineworker is attached to the underside of a helicopter via a short-haul or long line, or positioned on an external platform, their harness can rapidly shift due to wind, rotor wash or abrupt maneuvers by the pilot. A momentary lapse in communication or an unexpected movement could become catastrophic if a harness, an anchor or another piece of gear fails.
Rope access on transmission structures: In environments that limit climbing or the use of bucket trucks, T&D rope-access methods are frequently employed to gain safe, controlled entry to lattice towers, poles and other structures. Crews rely on dual-rope systems (i.e., a working line and a backup line) anchored to secure points on the structure. If a rope system is poorly maintained or an anchor is inadequate, a single failure could lead to a serious fall. Rescue efforts could be complicated by proximity to energized parts and/or ground sources combined with changing weather conditions, increasing the importance of clear evacuation plans.
Wire carts: These carts enable workers to travel along conductors or messenger lines across multiple spans, greatly reducing climbs. However, carts can be suspended hundreds of feet in the air, so a sudden medical issue, equipment malfunction or shift in the line could cause a worker to lose balance. Teams must be ready to quickly rescue an incapacitated worker, especially if the span is long or the terrain below is inaccessible.
Training and Competency
Conventional lineworker training may not be sufficient for these advanced tasks. If that’s the case, workers and supervisors must receive additional instruction specific to the duties they’ve been assigned. Training should address:
- Method-specific fall protection: Crews must know how to inspect and don harnesses rated for dynamic or aerial loads and be able to manage the distinct forces associated with helicopters, rope work and/or wire-cart travel.
- Communication and coordination: Whether dealing with aviation or vertical rope systems, a single miscommunication can lead to dangerous movements. Well-understood hand signals, radio protocols and a clear chain of command help to avert sudden, unexpected maneuvers.
- Electrical awareness: Energized lines – or even de-energized lines with induced voltages – pose electrocution and arc-flash risks. Workers must be trained to understand safe approach distances, grounding procedures and how to use insulating tools.
- Rescue and evacuation: Specialized rescue training is vital to properly care for an injured or incapacitated worker below a helicopter, on a rope system or in a wire cart. Regular drills build familiarity and confidence.
Lastly, suspension trauma – also known as harness-induced pathology – must be covered in depth. Any worker suspended for an extended period is at risk if they cannot relieve the pressure on their legs; such pressure causes reduced blood flow that can lead to loss of consciousness and worse.
Suspension Trauma: Causes, Risks and Prevention
Suspension trauma occurs when a person suspended in a harness remains motionless, allowing blood to pool in their legs. In T&D tasks, this risk is elevated for helicopter workers, rope-access workers, and any worker riding a wire cart who could become stranded or incapacitated.
Here are four key considerations to help prevent suspension trauma:
- Proper harness fit: Harnesses with wide, padded leg straps or seat-like designs help to prevent blood vessel constriction. Ill-fitted straps can quickly cause circulation loss.
- Rapid rescue: Job planners must anticipate the need to bring a suspended worker to a safe platform or the ground within minutes. Frequent drills will confirm whether teams can lower or hoist someone rapidly enough.
- Suspension relief straps: Foot loops or relief straps built into a harness allow a suspended worker to briefly “stand,” encouraging blood flow to the heart and reducing fainting risk.
- Training and awareness: Workers should be taught to recognize the early signs of suspension trauma (e.g., dizziness, numbness, sweating) and how to assist a suspended co-worker until a full rescue can occur.
Equipment Selection, Inspection and Use
Helicopter-rated equipment: Recent proposals from the Federal Aviation Administration have suggested aligning fall-protection requirements by recognizing harnesses that meet ANSI/ASSP Z359.11 requirements as appropriate for human external cargo operations. It’s important to note, however, that this change has not yet been approved and remains a work in progress. Until the FAA finalizes any revisions, operators should continue adhering to the existing approved standards and guidelines. Additionally, keep in mind that use of a harness that meets ANSI/ASSP Z359.11 requirements does not ensure safety if the harness is poorly maintained or doesn’t meet the design requirements for the task. Any visible damage – including frays, broken stitching and rust – warrants immediate removal from service.
Rope-access systems: Rope access typically involves a working line and a backup line anchored to the structure. Clamps, ascenders, descenders and related hardware should be checked frequently for wear and damage. If any system component fails, workers may have little recourse, making redundancy and careful inspections crucial to worker safety.
Wire-cart attachments: Wire-cart setups must include secure attachments to the conductor or messenger line. A second tether or backup lanyard – ideally anchored separately – often is advised. Hardware such as bolts, cables and locking mechanisms should be inspected daily. Cart systems might experience significant sway or torsion when lines bounce or in windy conditions.
Oversight and Accountability
Industry regulatory bodies require a competent person to identify and address fall hazards, a critical role for safe execution of specialized tasks. This individual must be knowledgeable about the operation taking place and empowered to:
- Evaluate and approve gear. This includes verifying that the correct equipment is in use, from any FAA-recognized or -approved systems to properly rated anchoring devices and rope systems meeting OSHA, ANSI and manufacturer guidelines.
- Oversee training, ensuring that crew members are fully educated on method-specific fall protection practices, can identify signs of suspension trauma and are prepared for emergencies.
- Stop unsafe work. If conditions such as high winds, thunderstorms or equipment defects pose risks, the competent person must have the authority to halt operations until safe conditions resume.
- Record and investigate, keeping detailed logs of inspections, training sessions and near-misses to help pinpoint potential safety issues early on.
An organization that empowers the competent person to act encourages a proactive safety culture in which hazards are addressed immediately – rather than after an incident.
Effective Rescue Planning
Rescue capabilities are a necessity given the elevated risks involved in these specialized tasks. Possible rescue scenarios range from a worker who’s passed out in a wire cart to a jammed rope-access device on a tower to a lineman incapacitated under a helicopter. Here are some planning-related items readers will want to consider:
- On-site rescue gear: Rope systems, pulleys and even a designated rescue helicopter can be essential. Wire-cable backups or guiding lines allow rescuers to reach stranded workers.
- Rapid response to suspension trauma: Since circulation problems can intensify in minutes, teams must quickly be ready to free and lower a suspended worker. If a helicopter must leave the scene, ground crews should be prepared to take over.
- Dedicated rescue personnel: By including personnel focused solely on rescue operations, reaction times during high-risk operations can be significantly reduced. Regular drills and tabletop exercises further enhance crew readiness.
Conclusion
Managing fall hazards for helicopter operations, rope-access methods and wire-cart travel requires more than just the ABCs referenced at the beginning of this article. These tasks demand precise equipment selection, thorough worker training and well-rehearsed rescue procedures, particularly with respect to suspension trauma.
Leaders must invest in proper gear and training while fostering a “speak up” culture. Competent persons must be empowered to enforce safety decisions. And every worker – from those on the ground to those in the air – must carefully inspect their equipment, stay alert and promptly report hazards. To ensure both regulatory compliance and employee well-being, it’s also necessary for all personnel to stay current with industry regulations and guidance.
Ultimately, by blending modern, specialized equipment with proactive leadership and deep worker engagement, the T&D industry can continue to build and maintain essential infrastructure while keeping workers safe.
About the Author: Mike Starner, CUSP, CHST, has 30 years of combined operations and safety experience in the electric utility industry. He currently serves as the executive director of outside line safety for the National Electrical Contractors Association.
Photo: Courtesy of the National Electrical Contractors Association
- The Good Shepherd
- April-May 2025 Q&A
- A Checkup from the Neck Up
- Equipotential Grounding is the Law
- Safety By Design: Leadership and Employee Involvement
- Making the Safety Connection: The Impact of Total Well-Being in the Workplace
- Using the Prediction Model to Prevent Incidents and Near-Misses
- Beyond the ABCs: Fall Protection for Unique Tasks