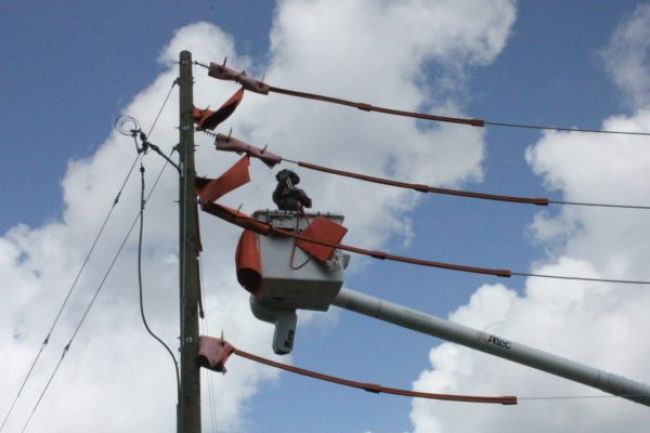
‘Avocado Hand’ and Scaling the Safety Message
Chew on this recipe for crafting or recrafting an organization’s safety culture.
Avocado toast has become all the rage at restaurants and on social media posts over the past several years. I eat it; it is delectable. You make it by toasting some bread, adding some ripe avocado and maybe some salt, and then maybe some tomatoes or sprouts. Easy, right?
Now, I want you to think of making this dish, but consider it from a safety angle. Avocado toast can be a hazardous dish to prepare. You must toast bread, which is a potential fire hazard, and you have to cut open an avocado. Unfortunately, people sometimes do this by holding the avocado in their hand, which can result in line-of-fire or knife-related cuts to their hands and wrists. In fact, these injuries are so common that they have a medical term – “Avocado Hand” – and account for thousands of emergency room visits each year.
You may be wondering by now, what does this have to do with utility industry safety and, more specifically, the topic of scaling the safety message?
When there is a task that injures thousands of our workers each year, we try to remove the hazard. Keep that in mind as you read the next part of this article. But first, I want you to do me a favor. Talk to your teenage child or your spouse about Avocado Hand. Explain that they shouldn’t hold an avocado in their hand when cutting it. Many of them will listen and cut it on a cutting board, keeping their hands away from the knife blade. Mission accomplished, right? We have trained some people to safely perform a specific task. But have we actually educated them as to why they need to do it this way? If we give them a different fruit or vegetable to cut, will they use the knife safely and apply the overall safety theory regarding the line of fire and hand injuries? Or will they default to what they know and are in the habit of doing? In other words, were the message and training scaled enough that they became ingrained in the culture of working safely?
A Common Issue
This is something many of us are facing in our industry. I spent many years at large utility companies where the safety culture was already established. You may be in the same boat, or you may find yourself in a position where you must create the culture from scratch. Regardless of what position you find yourself in, you may have asked the question, how do I change a safety program from one that is task specific to one that keeps workers safe regardless of the task?
When a workforce is already performing with a high level of safety, you might think this culture has already been achieved. Why reinvent the wheel if the numbers look good? But while you may have a successful safety record, you must consider whether the overall culture is too task specific, with the steps employees are taking on Task A not necessarily translating to Task B. This is where I went to work in my organization. We were safe when working on a specific task, but we left ourselves exposed when the task changed. Much of the time, we did not realize our exposures and hazards had changed and thus our mitigations also needed to change. We needed to operate more in the safety theory space. We needed to scale the message.
Scaling the Training
Scaling the safety messaging meant scaling training. Instead of selling the message of “if this, then that,” we started training using “when this, look for that.” Of course, this kind of change does have the potential to be dangerous, so it requires a lot of work and oversight; a shift in the safety theory of an organization can lead to events if not executed correctly. It takes a team to implement the change I’m writing about in this article. That team should consist of dedicated, passionate professionals who truly care about the workforce, training the next generation and working safely above all else. It takes commitment from operations, and it also takes relationship building within senior leadership. If an organization can align behind the idea of scaling the safety message this way, the results will almost certainly speak for themselves.
Admittedly, changing human performance is one of the most difficult things leaders must do in any industry, including ours. In the initial stage, there must be a concerted effort to build relationships and sell the new vision. But this first step isn’t all about talking. I promise you, if you try to sell your vision by doing all the talking yourself, you will fail. Before you begin to try to sell it, your vision must be informed by listening to your teammates and other leaders who have responsibility for employee safety.
As relationships are being formed and the vision is being cemented, training must also be implemented. I’m not talking about training of the end users or boots-on-the-ground employees at this point, but training of other leaders. I personally sat down with a member of my organization’s senior leadership and presented training that represented my vision. We talked through it, particularly the “why” behind it. He bought in. Today, leadership and safety move forward in one cohesive (i.e., not splintered) group. This is a vital step to properly scaling a safety message within an organization.
‘Arming’ the Trainer
OK, so, the vision is taking hold. Relationships are being formed. The company is moving forward cohesively. What’s next?
More training.
But we’re still not training the end users yet. It is now time to train the trainer. I know that’s a term that has just about run its course. Typically, it’s a term that provides cover for organizations that can’t or don’t want to provide the resources for a larger training program. One person gets trained, and then it becomes their responsibility to disseminate the information they learned to other workers. I didn’t like that idea for the work we were trying to do at my company. I didn’t want to put the responsibility to teach and train this new vision on someone who was just learning to understand it themselves. That is not fair, and it leaves us exposed to hazards. Because the whole goal is to lessen our exposure, I didn’t set out to train the trainer in the traditional way.
Instead, I “armed” the trainer. I traveled to operations centers and talked with the trainers, the leadership teams and the boots-on-the-ground employees. Everyone heard the same message directly. I was able to support the trainers when they would discuss the new theories and thoughts with the teams. We performed field and crew visits to speak directly with the workforce. We demonstrated to them hands-on, real-world applications of safe work practices that transcend specific tasks so they could understand the vision by witnessing it. Overall, employees were able to see the importance of this undertaking, leaders were able to understand it, and the safety department was able to coach, teach and train, all while senior leadership was supportive of the safety vision. It was cohesive, it was uniform, and it was effective.
Naturally, we did host more traditional training sessions among the safety team. We engaged in the typical PowerPoint presentations, hands-on practical trainings and lessons-learned conversations. What was evident during these meetings was how effective the arm-the-trainer approach was. Members of the safety team were taking the lead on coaching and training others. They would talk through different approaches to a task or job, explaining to others the myriad ways something could be done, all while doing it safely. Within a handful of months, the organization went from fully task-specific training and performance-based safety to a new theory-based safety program. Full integration is not yet complete, and the overall culture change will take more time, but the maturation that has already occurred is exciting.
Conclusion
Scaling a safety message is essentially crafting or recrafting a safety culture. It’s not that there was no safety culture in place, but now a new path is being forged. The hope is that this path will lead the organization toward a safer, more supportive and more productive output. Each of us wants our workers to go home safe and sound at the end of the day. “Go home the same way you came to work” is what I was always told. So far, I have been able to achieve that, and I want all of my team members – and yours – to achieve the same. I want them to know not just how to cut avocados but how to safely use a knife no matter what they are cutting. To sum up, the goal is to develop workers who have an outlook on safety that transcends their specific tasks.
About the Author: Jeffrey Sullivan is the director of safety and training for Homosassa, Florida-based F&H Contractors. He has been working in the electrical utility industry since 2001, first for two large utilities prior to transitioning to his current role. Sullivan has experience in overhead and underground line construction and maintenance as a journeyman lineman and foreman, and more recently with utility engineering and design management.
- Understanding and Preventing Ferroresonance
- ‘It’s a Wonderful Life’: Acknowledging and Safeguarding Our Blessings
- The Health and Safety Plan: A Project Management Tool
- December 2023-January 2024 Q&A
- The Art of Safety – A New Hierarchy
- Safety Signs and the Importance of Training
- ‘Avocado Hand’ and Scaling the Safety Message
- Safety and Innovation Lead the Way at San Diego Gas & Electric