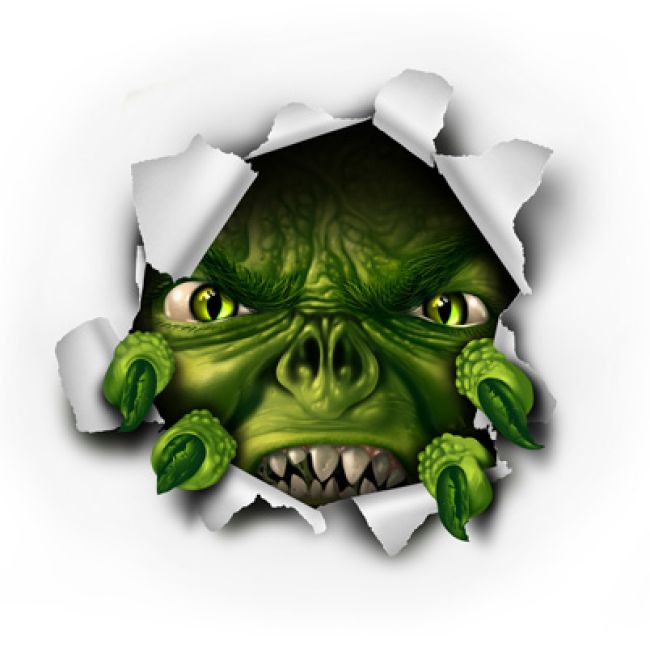
Are Compliance Grungs Taking Over Your Organization?
Do you have a safety culture that focuses solely on safety compliance and the use of personal protective equipment? If so, you probably also have the dreaded Compliance Grungs, which can secrete poisons throughout your organizational safety culture.
What exactly are Compliance Grungs, and how do deadly creatures relate to anything associated with safety? Deadly creatures kill, destroy, and cause suffering and pain. They wreak havoc and generate a great deal of harm. Individuals who work for organizations that promote safety only as a rule or compliance issue may experience similar phenomena without understanding why their safety culture is suffering.
To put it simply, Compliance Grungs are rules, policies or procedures that are considered more important than their application. They destroy a culture by promoting safety as a rule instead of a personal value, thereby strongly devaluing the importance of safety. Statements like “They don’t care about me,” “Management only wants to cover their own behinds” and “That rule is so dumb – they don’t know anything about our work” are sure indicators that you are suffering from an invasion of Compliance Grungs.
OSHA promulgates rules based on recognized hazards that cause or are likely to cause death or serious physical harm to employees. When compliance is prioritized over hazard identification, your culture will shift toward compliance-driven safety – that is, Compliance Grungs – instead of value-driven safety. Compliance-driven safety focuses on the rule, mandates compliance with the rule and places blame on rule violators. Value-driven safety focuses on two things: designing for safety and applying for safety, which we will discuss in greater depth later in this article. But first, let’s be clear. Rules and procedures are necessary for an effective health and safety process, but in a value-driven safety process, compliance becomes a byproduct – not the goal. This occurs because employees understand the value of safety and the role compliance plays in their personal safety.
Recognizing Compliance Grungs
If you answer yes to any of the following five questions, your organization may have Compliance Grungs.
- Do you copy OSHA standards and mandate compliance as a company safety rule?
- Are employees confused about how to apply rules and keep themselves safe?
- Are employees pencil-whipping the required safety documentation?
- Is noncompliance occurring in more than one work group?
- Are safety rules and procedures developed with little to no employee input?
Or, if you answered no to the questions above, do you and your colleagues instead identify the hazards OSHA promulgated its rules to address, determine if the hazards are present in your work locations and then identify the best methods to effectively eliminate or control the hazards to comply with the rules? If that is what is happening, employees rarely will be confused about how to successfully apply a rule for their personal safety. On the other hand, vaguely written rules and procedures that management or employees may not know how to apply create an environment of mistrust and drive a no-win culture of compliance-driven safety.
Don’t assume your organization doesn’t have Compliance Grungs. You must solicit feedback from employees and get everyone involved in identifying them. Use observations and audits to determine if your rules and procedures effectively control hazards and that employees understand them and are applying them correctly.
Eliminating Compliance Grungs
Compliance Grungs need to be eliminated in your organization to ensure safety success. The elimination process requires an organization to move from a compliance-driven safety process to a value-driven safety process. A value-driven safety process means everyone in the organization buys into and actively participates in a systematic approach of designing for safety and applying for safety.
Designing for Safety
Designing for safety requires the integration of hazard identification and risk assessment methods when designing rules, processes and procedures. In other words, a hazard must be identified before a rule or procedure can be developed to control the hazard.
According to ANSI Z10, “Occupational Health and Safety Management Systems,” a hazard is a “condition, set of circumstances, or inherent property that can cause injury, illness, or death.” Hazards can be assessed both in terms of severity (how bad is the potential outcome?) and exposure (how likely is an occurrence?). “Risk assessment” is the term used to describe the process of identifying hazards and risk factors that have the potential to cause harm. When designing for safety, be sure to ask the question, “How much risk am I willing to accept?”
Once hazards are identified, they must be controlled to eliminate or reduce the risk of serious injury or harm to workers. It is important to mitigate hazards using the hierarchy of controls, which identifies the most effective to the least effective method of controlling hazards. Keep in mind that use of PPE is considered the least effective method of controlling a hazard, so it is an employee’s last line of defense and should not be emphasized over other methods, such as engineering and administrative controls.
Applying for Safety
Applying for safety requires employees to take personal responsibility and accountability for applying rules and procedures intended to keep them safe on the job. For this to occur, organizations must design clear rules and procedures, communicate them effectively for mutual understanding, and provide regular coaching and feedback concerning their application.
Many organizations struggle with writing clear rules and procedures, so they default and copy OSHA standards. Unfortunately, copying OSHA standards can prove problematic as they are sometimes confusing and may have multiple interpretations. It is imperative to include employees who perform the work when developing safety rules and procedures that affect them. The following tips can help you simplify rule-writing and save you from using OSHA language.
- Make rules specific. Each one should be clear, concise and apply to a targeted area of concern.
- Make rules achievable. Every rule you write should be one with which employees can realistically comply given the work environment.
- Make rules relevant. A rule should have direct significance and connection with the work being done by company employees.
- Make rules trackable. Each rule should be able to be monitored for compliance or noncompliance.
Once clear rules and procedures are developed, they must be communicated for mutual understanding. Mutual understanding means we understand each other and mutually agree on the end results. Communication must include more than reading the rule in a safety meeting and mandating compliance. That type of communication is one-sided and rarely will result in success. Details must be communicated regarding the hazard, the risk associated with the hazard and the controls used to mitigate the hazard. Employees must know and apply the following: What is the rule? Why is the rule important? When do I follow the rule? Where do I apply the rule? How do I apply the rule?
For compliance to become a byproduct of value-driven safety, leaders must provide effective coaching and feedback. Coaching reinforces safe behaviors and strengthens relationships between management and employees and employees and their peers. It establishes and maintains standards of action, behaviors and expectations. An effective safety coach will support safe behaviors and offer useful and helpful feedback regarding at-risk behaviors.
Summary
Compliance Grungs destroy your safety culture and cause great suffering and pain. It is extremely important to recognize, identify and eliminate Compliance Grungs in your organization if you want to create a value-driven safety process. Emphasis should always be on hazards and the application of controls to eliminate hazards through designing and applying for safety. When employees buy into safety as a personal value, Compliance Grungs will be exterminated for good.
About the Author: Pam Tompkins, CUSP, CSP, CUSA, is president and CEO of SET Solutions and a 39-year veteran of the electric utility industry. She is a founding member of the Utility Safety & Ops Leadership Network and presently serves on the executive board. Tompkins has authored and presented technical papers on high-voltage electrical safety issues at iP conferences, IEEE workshops, ASSP conferences and for many other organizations. She is an OSHA-authorized instructor who specializes in helping electric power organizations in the U.S. and abroad comply with today’s safety and training requirements.