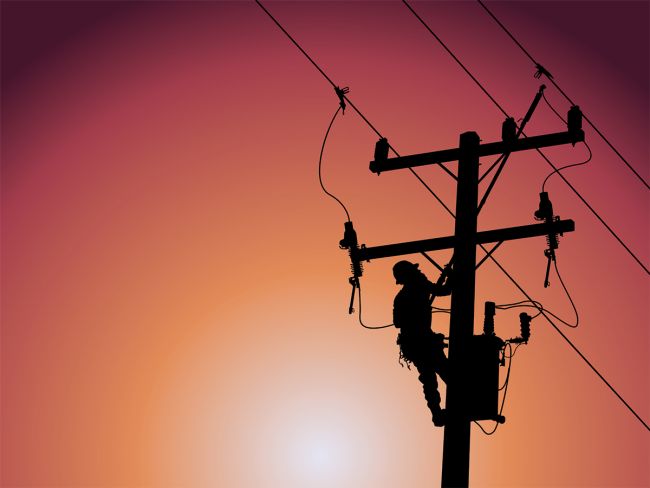
Actionable Safety: Modeling Change for Line Crews
Demonstrating simple strategies for teams to practice can begin to effect behavioral changes that improve safety.
When leaders model a specific safety behavior or tactic, we can achieve multiple positive outcomes, including initiating change in our organizations. It is critical, however, that we physically model the behavior with our actions – we must walk the walk, not just talk the talk. When we truly lead by example, we can expect our team leaders to model our behavior as well.
With that said, in this article, I’m going to present you with some simple, actionable safety strategies you can model that will begin to change your company’s culture of safety and crew dynamics.
The Confidence to Speak Up
During incident and accident investigations, it is not unusual to discover that someone saw the signs of what might happen but did not speak up. We seem surprised by this because everyone understands that anyone on the job has the authority to stop work, right? But as it turns out, there are many reasons why people don’t speak up. Amy C. Edmondson, a Harvard professor of leadership and management, has stated that we learn to preserve our self-image in about the third grade, so if we don’t want to look ignorant, we don’t ask questions. I know we have all been in situations where we were afraid to speak up, so how do we instill a sense of responsibility in our crews? Aren’t we all responsible for “if you see something, say something” – before things go wrong?
Let’s look at this in a different way. Telling our crews that they have stop work authority is a long way from them actually using that authority. We can provide bulletins on the topic, hold safety stand-downs and even write stop work authority into our job briefs. These all sound like positive and meaningful efforts, but when it comes time to use stop work authority to avoid an incident, someone must speak up and someone else must listen. A crew that actively practices these actions has a much higher probability of being successful at stopping work when necessary.
But is that – stopping work – really what we are striving for? If we need to stop work urgently because moving forward would lead to an incident or accident, then we are way too late. The signs that something may go wrong are usually present long before we reach the point of dramatically stopping work. What we are striving for instead is an environment in which our safety practices are modeled and learned long before someone acts upon their stop work authority. What we really want is to recognize early on when we need to make a change to the job plan to keep an incident from happening.
So, what would that look like? After an incident occurs, we spend lots of time, money and effort identifying causal factors, lessons learned and the root cause. But what if we took some of that time, talent and treasure and modeled strategies to avoid the incident altogether? Again, if we want workers to speak up, the first time they do so shouldn’t be just before things are about to go terribly wrong. What if, for example, leadership participated in job briefs, helping to model what an interactive brief looks like? In his book “The Checklist Manifesto,” author and medical doctor Atul Gawande describes the “activation phenomenon” as follows: “In hospital operating rooms when team members identified their roles prior to a procedure and expressed any concerns they had, it ‘activated’ them to speak up more easily to question or express concerns later during surgery.” In our industry, an apprentice who is asked during every job brief to identify their role and express any concerns has the chance to model the desired behavior so that when something comes up while work is being performed, there is a greater chance they will feel comfortable speaking up.
Of course, it must be safe to express concern without repercussion. During a job brief, we think we are right on target when everyone nods their heads in consensus, but we gain exactly zero insight from a nodding head. Insight comes from the one person who may have a dissenting opinion or a different idea. So, we must also model how to acknowledge someone with a differing opinion to encourage the confidence for this behavior to continue. We’re not required to like the person or the idea, but we do need to listen to understand that person’s perspective. Then, our subconscious will sort all the information we’ve received, process it and make connections that will pop into our consciousness at some future point – uninvited. That’s how we make connections; not by our own genius but by the collective genius around us.
Pausing and Soft Stops
Pausing or engaging in a “soft stop” is another practice that can be modeled. The idea is that before making a critical move or when our intuition signals that something might be amiss, each of us should create a practice of pausing for 10 seconds. Our conscious mind processes 40 to 50 bits of information per second. That means in 10 seconds, your mind can process 400 to 500 bits of information. Imagine a crew of four individuals each pausing for 10 seconds. That’s upward of 2,000 bits of information processed in a very short period. Once the pause is complete, it’s important to weigh the consequences of anything you learned during that time and then act on what you’ve learned. If needed, make slight changes to minimize the risk you gleaned from the exercise.
A simple, actionable strategy is for you or another leader to model the practice of soft stopping. To begin, pick a critical move, such as switching or removing a jumper. Just before you perform the move, visualize what you are about to do for approximately 10 seconds. Then, weigh the consequences of whatever information you gleaned from that 10-second pause. For example, maybe there’s a better position for switching, or the jumper may sag too far when you take your end off, so you ask your partner to remove their end first. You can also make use of the pause by writing down what might have happened and then communicating that effectively to the team. While there is no tangible reward for things that don’t happen, this is part of changing our culture – and that is a reward in itself!
Mental Simulations
The best athletes in the world use mental simulation and visualization techniques before they perform their tasks. Mental simulation fires the same neurons in your brain as if you were physically doing the task, so it’s worth the time and effort to try these simulations with your crews. Give workers uninterrupted time to look at the work to be done and mentally visualize themselves doing it. We want to encourage them to review the work, visualize what it will look like and then share their mental pictures in a discussion. We may learn that often, we all see the same things, just a bit differently. By modeling this practice for the crew or team, they can see how the practice – especially when done consistently – can make a real difference.
Here’s a mental simulation you can try with a line crew. Let’s say one of the crew members makes an electrical contact and is now unconscious in the bucket. OK, go! Ask the team to discuss what they would do in response, which will simulate some of the stress of a real situation. Run through the simulation until everyone is satisfied that they have the best sequence of events. Ask questions, such as, is the truck energized, who calls 911 and when, where’s the AED, who starts CPR, and who will continue after two minutes? When a real event occurs, you don’t want that to be the first time the crew responds. And we shouldn’t practice until we get it right – we need to practice until we can’t get it wrong. Further, the mental simulation should be practiced regularly with different variations. These simulations will cause our brains to begin making connections to help us avoid electrical contacts altogether.
Conclusion
Modeling simple strategies for teams to practice can begin to effect changes in behaviors that can improve safety. The tactics described in this article are actionable ones that can be practiced with crews to improve crew dynamics and promote a safer, more proactive culture. Let the games begin!
About the Author: Bill Martin, CUSP, NRP, RN, DIMM, is the president and CEO of Think Tank Project LLC (www.thinkprojectllc.com). He has held previous roles as a lineman, line supervisor, project manager and safety director.
- Security in the Field: A Largely Unnoticed Need
- Lineworkers and Line-Clearance Workers: Understanding Their Similarities and Differences
- Containing Contagions in Close Quarters
- Actionable Safety: Modeling Change for Line Crews
- From My Bookshelf to Yours: ‘The 7 Habits of Highly Effective People’
- Just Like the Real Thing: Training the Next Generation of Lineworkers
- December 2021 – January 2022 Q&A
- Installing Fiber-Optic Cable in Electric Supply Spaces