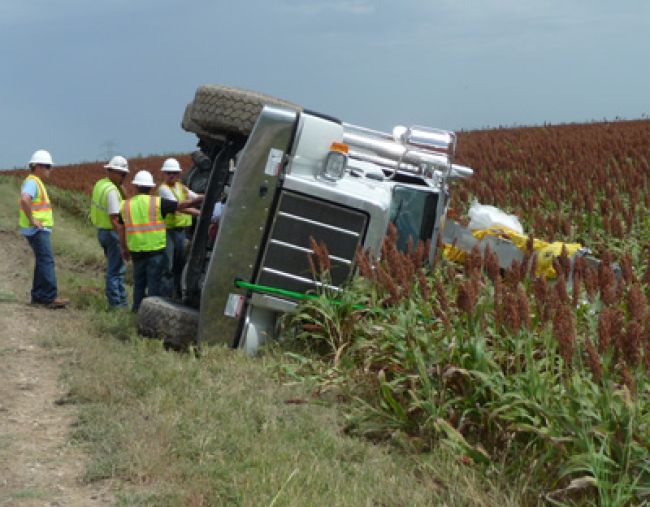
10 Tips for Better Incident Investigations
Several years ago, when I was serving as chief investigator for the NIOSH-funded Missouri Occupational Fatality Assessment and Control Evaluation Program, I was called to a scene where a 39-year-old journeyman lineman had been electrocuted while working for an electrical contractor. At the time of the incident, the lineman, his co-worker and the foreman had been working at an electrical substation. The city that owned the substation was in the process of switching their electrical service from a three-phase 4-kV system to a 12-kV system. There were several feeders on the structure, but only one was energized to provide service to the city. The lineman and his co-worker were on the steel framework of the substation when the lineman proceeded to work his way over to the incident point. He sat down on the structure next to the energized feeder and energized lightning arrestor and began to climb down the steel latticework. Typically the contractors accessed the structure with a ladder, but for one reason or another, the lineman chose to climb down using the corner latticework of the structure. At that point, the lineman contacted the energized arrestor with his forearm. His co-workers responded immediately and began CPR, and emergency personnel were summoned to the scene. Unfortunately, the lineman did not survive.
Despite our best efforts to protect workers in the field, incidents like these still occur and, as a result, you may find yourself leading an incident investigation. One of the primary goals of any investigation is to find out exactly what happened so that future occurrences can be prevented. With that in mind, I put together the following 10 tips designed to help you obtain quality information about each incident you investigate, put your interview subjects at ease, and determine an accurate account of what occurred before, during and immediately after each incident.
Tip 1: Be prepared.
A quick response is critical to any incident investigation. In some situations you may have to travel a significant distance to reach the incident site. If that is the case, make immediate contact with the supervisor or supervisors at the site so you can coach staff in advance of your arrival. It is important to note that all company employees should be trained on how to respond if and when an incident occurs on one of their job sites, and having written protocols in place will go far in preserving the site for the investigation.
You should also have your investigation kit stocked and ready to go at all times. Some kit essentials include your identification forms and credentials; a hard hat, safety glasses, boots and other necessary personal protective equipment; a camera with flash for photos and video, plus spare batteries; measuring tape; a notebook and a personal journal; your cellphone and charger; and a flashlight.
Tip 2: Ensure the incident site is safe and secure.
Again, all company employees should be trained on how to secure the site. If an incident occurs, immediately contact on-site management to make sure that company protocols are being followed and emergency responders are caring for any workers who sustained injuries. An on-site employee should take photos of the scene as soon as possible, before equipment or materials are moved. If OSHA must be notified of the incident, report the occurrence as required by law. Workers should be knowledgeable about how to prepare for an OSHA inspection in the event that you are not personally at the site when an agency representative arrives. Once you make it to the incident site, verify that anyone who sustained injuries has received appropriate medical assistance. You will also need to ensure that the site is safe and equipment has been de-energized. Next, confirm that your on-site supervisors have identified and collected names and contact information for all witnesses, employees and contractors.
Tip 3: Observe the incident site and collect the five W’s.
It’s important to get the full picture of the incident site. Site supervisors should be trained to take multiple photos from several angles to document the site. It’s also a smart idea to consider requiring site management to use an initial information form to get the information collection process started. All of this will help with your investigation in the event it takes you a considerable amount of time to reach the incident site.
When you’re observing the site, take care to note the locations of equipment, materials and any obvious damages. If work has resumed, ensure it is not compromising the incident site in any way. During your observation, you will also need to identify the five W’s:
• Who: This includes all individuals injured during the incident, as well as witnesses, emergency responders and any contractors.
• What: Determine what injuries occurred and the equipment damage sustained.
• Where: Write down both the location of the incident and the location of any injured individuals.
• When: Document the date and time the incident occurred.
• Why: What are the reasons the incident might have occurred? Did energy sources, equipment failures or environmental issues factor into the event? Record the answers to these and any other related questions.
Tip 4: Begin your root cause analysis.
Work to identify the direct causes and develop the chain of events that led to the incident. Determine the underlying factors that will help pinpoint the root cause. I use the agent/host/environment epidemiological triangle as seen in the figure below. Doing this helps me understand the relationship between these three factors. For instance, in the fatality investigation I described at the beginning of this article, the agent was 2400 volts to ground. The host was a 39-year-old journeyman lineman. The environment was a substation structure with multiple de-energized feeders and one unmarked, energized feeder.
When appropriate, use the 5 Whys technique, which is a simple yet effective tool that helps to identify the root cause of a problem or event. Essentially, you ask yourself “why” five different times. Let’s apply the technique to the journeyman lineman fatality I referenced earlier. Five questions you could ask to determine the root cause are:
• Why did the employee decide to climb down the structure instead of a ladder?
• Why didn’t management enforce the use of ladders and bucket trucks?
• Why didn’t the journeyman lineman remember that particular feeder was energized?
• Why weren’t the conductors insulated or covered up?
• Why didn’t management recognize that the energized conductors needed to be covered up?
You can choose from several root-cause analysis methods based on the event you are investigating, but the 5 Whys technique is a great method that’s easy to use.
You can also incorporate similar types of questions into your interviews with witnesses and management. In the case of the previously referenced journeyman lineman fatality, it would have been appropriate to ask how often employees free-climb down a steel structure and how often rubber cover-up is used on conductors.
Tip 5: Realize that interviewing employees can be tough.
Conducting interviews takes skill, and the process can be stressful on workers as well as investigators. For best results, ask to interview workers and witnesses individually. The more that employees talk to each other, the more the story may change, and witnesses could start to fill in the blanks with hearsay. It is also critical to gain the trust of the individuals you interview. If you don’t, they may not tell the whole truth, rendering the interviews pointless. I work to gain the trust of interview subjects by explaining that I am not attempting to find fault, place blame or get anyone fired. I let them know that my goal is to prevent such incidents from happening again.
Tip 6: Be sensitive.
When you are conducting an interview, keep in mind what your interviewee may have witnessed when the incident occurred and act accordingly. Investigators and all other company employees should receive training in critical incident stress. You need to be able to recognize the signs and symptoms of this type of stress, and you should be prepared for witnesses to experience emotional breakdowns during your interviews with them. Additionally, it is important for you to ensure that employee assistance is available through your human resources department. Lastly, be aware that if the incident was tragic, witnesses may block key elements of the event from their memory. Follow-up will likely be necessary as you work to piece together the puzzle of exactly what happened.
Tip 7: Put interviewees at ease.
No one likes to be investigated or audited, so try these tactics to ease interviewees’ stress. Instead of sitting directly across from an interview subject at a conference table, change into field attire and consider sitting next to him on the tailgate of his truck. Or, set up a couple of chairs outside in the shade or inside the construction office. Always allow the worker to share his story about the incident. Try not to take too many notes while the witness is talking. If necessary, jot down key words to help you remember important points. Afterward, go back through the account of the incident with the employee, separating the information into three parts: pre-incident, incident and post-incident. Ask the interviewee if you may contact him again if you have additional questions, and thank the worker for his help. Then, using the key words you jotted down, take the time to make detailed notes based on the interview.
Tip 8: Ask the right questions.
Start each interview with broad, open-ended questions that can’t be answered with a simple yes or no. Don’t be afraid to ask straightforward questions; there’s no reason to beat around the bush. Let’s say you were investigating an incident similar to the journeyman lineman fatality I referenced at the beginning of this article. Two questions it would make sense to ask are, how often does the crew use rubber cover-up for exposed conductors and, if they had cover-up available, why was it not used the day of the incident?
Tip 9: Engage witnesses and the injured employee to help prevent future incidents.
During your interviews, ask all witnesses and injured employees to provide their opinions about what caused the incident and what they would do to prevent it from happening again. Listen intently; the best investigators are the best listeners. After the interviews are complete, stress to each individual how important their input is to preventing a repeat incident, and thank them for their time and honesty.
Tip 10: Maintain a positive, objective attitude throughout the investigation.
Do not intentionally intimidate interview subjects, interrupt them or jump to conclusions. Do not show any inappropriate emotions or make wisecracks about the incident. Remember, nearly 60 percent of your communication is nonverbal while close to 40 percent corresponds to your tone of voice. Compile your investigation report by presenting the facts and providing valid prevention recommendations, while leaving your biases to yourself. Ask a good proofreader to review your report and make any necessary corrections before you submit it. Go over the report with a key witness or two to make sure they are on board with your facts and recommendations.
Summary
Applying these 10 tips to every incident investigation, large or small, will help you succeed in collecting the necessary information, make you a stronger investigator and ultimately assist in preventing future incidents from occurring. You will walk away knowing you have done the best job possible in some of the worst-case scenarios.
About the Author: Thomas Ray, CSP, CUSP, is a safety specialist for City Utilities in Springfield, Mo. He has more than 23 years of safety and incident investigation experience and can be reached at tom.ray@cityutilities.net.