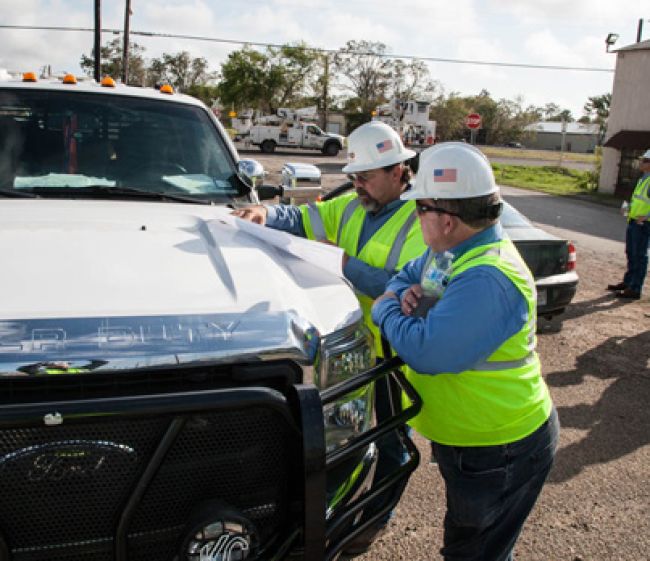
Solving the Safety Culture Puzzle
Have you ever thought about the similarities between solving a puzzle and transforming a safety culture? For one thing, the challenges of solving a puzzle – no matter if it’s a jigsaw puzzle, a Rubik’s Cube, a riddle or a maze – range from simple to difficult, just as the challenges of a safety culture transformation do. And second, people approach solving puzzles and creating cultural transformations in myriad ways.
Whether you’re trying to solve a puzzle or transform the way your organization handles safety, two things are for certain: to be successful in your mission, you must have all the necessary pieces before you get started, and you must then fit them into their proper places. In the safety world, those pieces include a clear vision, commitment, a positive attitude, accountability, clear communication and leadership support. As you fit each piece into its appropriate spot, you take one step closer to your goal – a strong safety culture. But a piece placed in the wrong spot, or one that’s missing altogether, can lead you in the wrong direction.
So, how do you begin to transform your organization’s safety culture if it is missing pieces, has interdependencies and can be approached in more than one way?
The First Step
The first step is to evaluate the present state of your safety culture. From there you can develop a plan and build a foundation, both of which are critical to success. During this step you should ask yourself some important questions. For example, do you have a hard time getting employees to comply with wearing personal protective equipment or to follow other standard operating procedures? If the answer is yes, you must take the time to explore why these issues are occurring. Is the PPE uncomfortable? Are other procedures difficult to comply with due to external factors? Is something else going on?
If you don’t ask why, you will never fully understand your company’s safety culture nor what needs to be changed. Culture is built on traditions established over time, and as time passes, some employees may become complacent. Sometimes these complacent employees are even rewarded because they prioritize production over safety. It’s situations such as these that end up driving an unsafe culture, and you must find out why they’re happening if you want to change them.
As you learn more about how to keep your employees engaged and concentrate on making safety a value rather than a priority, it’s important to keep in mind that you are asking both management and employees to embrace a culture that may be unfamiliar to them. Because culture is built on traditions established over time, as noted above, cultural changes take years to achieve, and you should expect there to be many backslides during the process. As a leader, the most important thing to remember is that you cannot force change. You cannot make anyone hold safety as one of their values. Instead, you must humble yourself and look to employees in the field who have hands-on experience to help you find the right solutions. Ultimately, their lives depend on making the value shift from productivity to safety, and the organization will achieve greater buy-in when field personnel are involved in the process.
Setting Goals and Taking Accountability
As you develop your plan, think about the way you set goals for employees. Are the goals driven by numbers, such as budgets or production hours? Do you ever include goals for safety? If goals are based on numbers and don’t include anything about safety, you have already demonstrated to employees that production is the greatest priority. Not only that, but if you also act as though production has a higher value than safety, your actions reinforce the written policies and procedures. Employees are always looking to see what you do, so you must be accountable for both your words and actions. If you talk about safety but don’t budget for it or take the time to implement safer work practices, employees will recognize that. Management must exhibit their buy-in of safety as a core value before others will follow. But be cautious. If a goal or performance indicator could incentivize unwanted behavior, you may be doing more harm than good. The same goes for what is being measured within your company. If you are focusing on the wrong metrics, you can incentivize undesirable behaviors.
It bears repeating that personal accountability is paramount in a successful safety culture transformation. Everyone in an organization must be held accountable for their actions. If an employee is injured, the incident investigation should not focus only on the employee and his or her actions – it should be viewed through a broader lens. For example, did the employee review the job safety analysis prior to beginning work? Did management provide the employee with the proper training to successfully perform his or her job? Were crew members looking out for their fellow employee? Was there appropriate, transparent communication at all levels? If the answer to any of these questions is no, there is an issue that needs to be resolved. Asking the right questions aids in determining the incident’s root cause, and once the root cause has been identified, the organization can implement solutions based on that cause, not assumptions.
Communication and Lagging/Leading Indicators
Communication can be one of the greatest challenges when working to change a safety culture. People often just want to start a job and complete it – that’s human nature. But if safety is briefly covered during a morning tailboard meeting, that’s likely not enough to ensure work is done safely throughout the day. Communication also is critical as the job is happening, where the true hazards exist.
Lagging and leading indicators also are pieces of the safety transformation puzzle. As a safety culture matures, reactionary lagging indicators, such as recordable incident rates and preventable motor vehicle accidents, will move toward leading indicators such as training, behavioral observations and good catches. Organizations with mature safety cultures have time to focus on leading indicators because they have made significant strides in the reduction of injuries and accidents. If your safety culture’s maturity level is on the lower end of the spectrum, you are still trying to get to the heart of your issues. You need time to focus on the underlying factors that are contributing to injuries and accidents before you can focus on leading indicators.
Prevention is Key
Because prevention is the key to keeping employees safe, you must ensure your company offers a robust training program that gives employees the proper foundation to work safely. OSHA 30 and OSHA 10 training were identified at the company I work for as a level of improvement. In the past, we trained employees on lockout/tagout and confined space, fall protection and a multitude of other safety topics, but we never provided the foundation for why they are so important. In addition, the training was not aligned at an enterprise level to ensure that everyone received it. Today, all managers and foremen are required to take the OSHA 30 training, and all individual contributors receive the OSHA 10 training, at a minimum. Our goal is to educate every employee about minimum safety standards. Through this training, we are teaching them to recognize hazards and minimize their fear of saying that something isn’t safe, even if they aren’t entirely sure. Every one of our employees is empowered – and has the responsibility – to stop a job they believe to be unsafe. Having the courage to do so is more difficult. That is why these foundational training programs are so important.
Safety Leadership
Once the initial elements of your safety culture transformation are in place, you can then focus on teaching and coaching personnel in safety leadership. You can’t expect people to lead safely if they haven’t been given the proper tools to do so. Teaching employees how to be safety leaders must focus on experiential learning, meaning that those individuals learn by getting directly involved and doing the work. If you study the different ways that people learn, retention rates are low when information is delivered via lectures, reading and visual materials. On the other hand, retention rates jump considerably when learners are directly involved in discussions and demonstrations of work. Of course, teaching frontline managers to use their OSHA 30 training – to get out there and help their team work more safely – is not an easy task. Among other things, training should focus on how to speak to your employees about safety issues, including coaching and mentoring, conflict resolution, crucial conversations, analytics and problem-solving.
No safety culture can mature without three elements: education, support and empowerment. And while every organization is going to have different puzzles to solve, all of the groundwork should be the same – which means starting with a solid foundation and building on wins that propel you to reach your overall safety goals. You are not going to change the minds of the masses overnight, but if you continue to collaborate and find advocates who want your safety culture to mature, you will get there. Just like having all the pieces to a puzzle, it makes a difference when you have the right people on board engaging in the right conversations. A strong safety culture is not about the numbers; it’s about the way we care about and value each other.
About the Author: Andrea M. Guadarrama, MBA, STS, is senior manager of safety and health for San Antonio, Texas-based CPS Energy. She is the primary contact for creating and implementing People First services to enhance and improve the safety culture and work conditions that propel the Zero Harm focus for the company. Guadarrama holds a bachelor’s degree in applied arts and sciences from Texas State University, and a master’s degree in business administration and a change management certificate from Colorado Technical University.