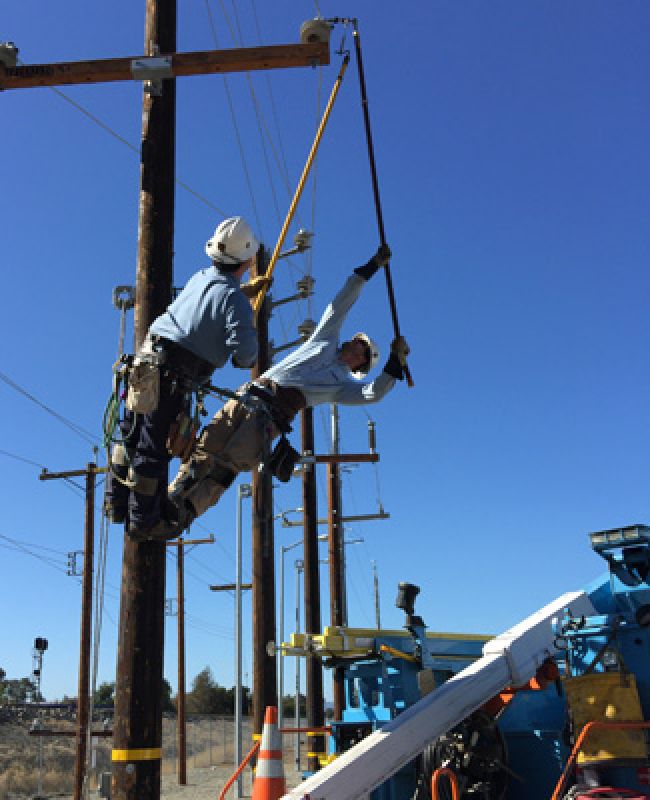
The Future of Ergonomics
Over the last decade, our industry has done a great job of reducing work-related injuries as a whole, but musculoskeletal disorders (MSDs) – also known as ergonomic injuries – are on the rise.
From 2008 to 2012, work-related injuries decreased steadily each year. During that same period, however, ergonomic injuries increased by approximately 15 percent, according to the U.S. Bureau of Labor Statistics.
As we know, OSHA sets standards and precise thresholds, such as those for vibration and noise exposure, in an effort to improve work site safety and prevent injuries. But there are no specific federal guidelines for ergonomics, and thus very few repercussions for employers if employees sustain ergonomic injuries, some of which can cause irreversible damage. According to a September 2015 article written by Jeff Sanford (see www.humantech.com/our-incidence-rate-is-down-so-why-are-our-msds-lingering), director and ergonomics engineer for Humantech, “OSHA can only fine your company for an ergonomics violation through the General Duty Clause (which is not specific to ergonomics).”
Sanford then goes on to say that “[m]any companies have a very good handle on lowering the risks associated with fatalities, amputations, and other life-altering injuries, but have not yet focused on eliminating MSD risk factors. The incidents associated with poor ergonomic design have always been on the OSHA log, they are just now rising to the top of your priority list with the decrease in safety-related incidents.”
The fact is, ergonomic injuries are completely different than general work-related injuries and therefore need to be managed differently – by measuring muscle effort as well as choosing the tools and work practices that are associated with decreases in muscle effort.
Technological Advances
As it relates to tools used by utility workers, the future of ergonomics is in technology – particularly electromyography (EMG) testing – that enables ergonomists to measure and analyze objective data and quantify a tool’s worth. Using state-of-the-art EMG analysis equipment and ergonomic evaluation software, today’s ergonomists can measure and record the amount of electrical activity produced by the skeletal muscles when an individual uses a tool. With this information, plus the knowledge of a worker’s maximal voluntary contraction (MVC) – a measure of strength – ergonomists can evaluate muscle exertion percentages. Those percentages can be compared against optimal muscle contraction values. Muscle exertion greater than 20 percent of an individual’s maximum strength (percent MVC) will contract the muscle to the point of partially occluding blood flow. Peak exertions over 60 percent MVC contract muscles to the point of stopping blood flow to or from the muscle. Contraction greater than 60 percent MVC may cause localized muscle fatigue and can be associated with increased risk of injury.
Today, thanks to technological advances in EMG testing, ergonomists can conduct task analyses and tool performance testing at the job site – instead of only in a laboratory – whether that’s a building or an outdoor work site where employees are leaning out of buckets or climbing poles. One of the many benefits of conducting on-site testing is that it offers ergonomists even greater opportunities to observe muscle contractions through individuals’ use of a variety of tools, in a variety of positions. Plus, they are able to collect grip strength and biofeedback information – such as heart rate, ECG waveform and skin temperature – in real time.
Whether ergonomists collect data in a laboratory or in the field, once they have completed their analyses, results can be shared with end users, which helps them understand the immediate safety and ergonomic benefits – or lack thereof – of utilizing the tools that have undergone testing. And this understanding, in turn, makes it simpler for individuals and companies to determine which tools to purchase for improved employee ergonomics.
Leading the Way
One company that is helping to lead the way in tool testing and analysis is Greenlee, a manufacturer of ergonomic tools. The organization recently launched the Greenlee ErgoLab, an industry-first ergonomics laboratory. According to Jeff Smith, Greenlee’s former director of engineering, “The idea came about when our ergonomics analysts saw the need to improve the quality of life for the next generation of utility and electrical workers. Our team began to identify the initial point of injuries and trace many repetitive and long-term injuries back to ergonomic issues that can be fixed through redesigning, re-engineering and improving work practices.”
The Rockford, Ill.-based laboratory offers state-of-the-art equipment to identify a tool’s ergonomic value through scientific testing, measurement and analysis. The company has also developed a mobile version of the Greenlee ErgoLab to offer job site analysis to end users.
About two years ago, Pacific Gas and Electric Co. (PG&E) partnered with Greenlee and began using the company’s Gator line of battery-powered cutting and crimping tools. This move continues to impact PG&E’s electric distribution operations, including more than 2,000 power lineworkers spread across 66 percent of California. During the implementation of the utility’s system-wide ergonomic tool deployment, at-risk tools were removed from service and more than 1,500 utility trucks at 100-plus work locations were outfitted with Greenlee Gator tools.
Through this partnership, PG&E has experienced reductions in worker injuries and associated costs. By using the Greenlee ErgoLab technology, PG&E has been able to not only measure the muscle effort reduction that resulted from switching to Gator tools, but the utility also has been able to quantifiably measure injury reductions and improvements in work efficiency. From 2013 to 2015, PG&E eliminated lost workday cases, moving from 26 cases in 2013 to zero cases in 2015. Similarly, the utility significantly reduced OSHA recordable cases by 61 percent, from 26 in 2013 to 10 in 2015. According to PG&E, reducing their OSHA recordable cases by 61 percent saves the company about $1 million per year. Eliminating the lost workday cases saves the company an additional $1 million per year. Regarding work efficiency improvement, PG&E determined that they saved 25,504 man hours – or $5.5 million – between 2013 and 2015 due to improved productivity. Overall, the company has calculated that the ergonomic intervention saves them more than $600,000 each month, or $7.3 million annually.
PG&E’s efforts to improve ergonomics within their organization recently led to the utility participating in the 19th annual Applied Ergonomics Conference’s internationally recognized Ergo Cup competition, which was held in March and featured best practices from all over the world. This is a historic achievement; not only is PG&E the first utility to be accepted into the competition with ergonomic tool interventions, but they were the Ergonomics Program Improvement Initiative Ergo Cup Winner, using tools from Sherman + Reilly and Greenlee. During the event, PG&E competed against companies including Gulfstream Aerospace Corp., Honda, GE and Johnson & Johnson to highlight their successful ergonomic solutions.
Trending Up
According to data published by Transparency Market Research (TMR) late last year, power tool sales are forecasted to increase 46 percent from 2015 to 2021. In 2015 they represented a global market worth of $26.15 billion; that’s expected to grow to $38.03 billion by 2021. Whether tools are being utilized by utility workers or by other individuals, one evaluation criterion users should consider prior to purchase is whether or not a tool meets ergonomists’ approval. And even before tools become available for purchase, it is critical for manufacturers and ergonomists to work together, beginning with the design phase and ending in consumer education. In the high-speed, growing tool industry, introducing the benefits that ergonomic safety offers will aid in decreasing the injuries of tool users around the world.
In summary, testing of ergonomic tools can include many subjective analyses – including those pertaining to maneuverability, adjustability and grip size – but the future of ergonomics is objective testing data, which is produced by electromyography. Understanding the procedural setup of sensors, electrodes and leads, and locating muscle groupings and muscle bellies, are highly specified tasks, the performance of which can translate into increased safety, financial savings and injury reductions. The costs are minimal and the savings are enormous. Therefore, as ergonomic injuries are rising and the reliability in measuring muscle effort has become greater than ever, you need to ask yourself: Are the tools you’re using ergonomist approved?
About the Author: Raffi Elchemmas, AEP, MBA, is a tool ergonomist who is board certified in professional ergonomics. He completed his kinesiology studies at Michigan State University, graduate studies at DePaul University in Chicago, and postgraduate studies in ergonomics, health and safety at Harvard University. Elchemmas is a member of the Human Factors and Ergonomics Society. He has presented at numerous international conferences and contributed to a variety of publications on health care and ergonomics. He can be reached at relchemmas@textron.com.